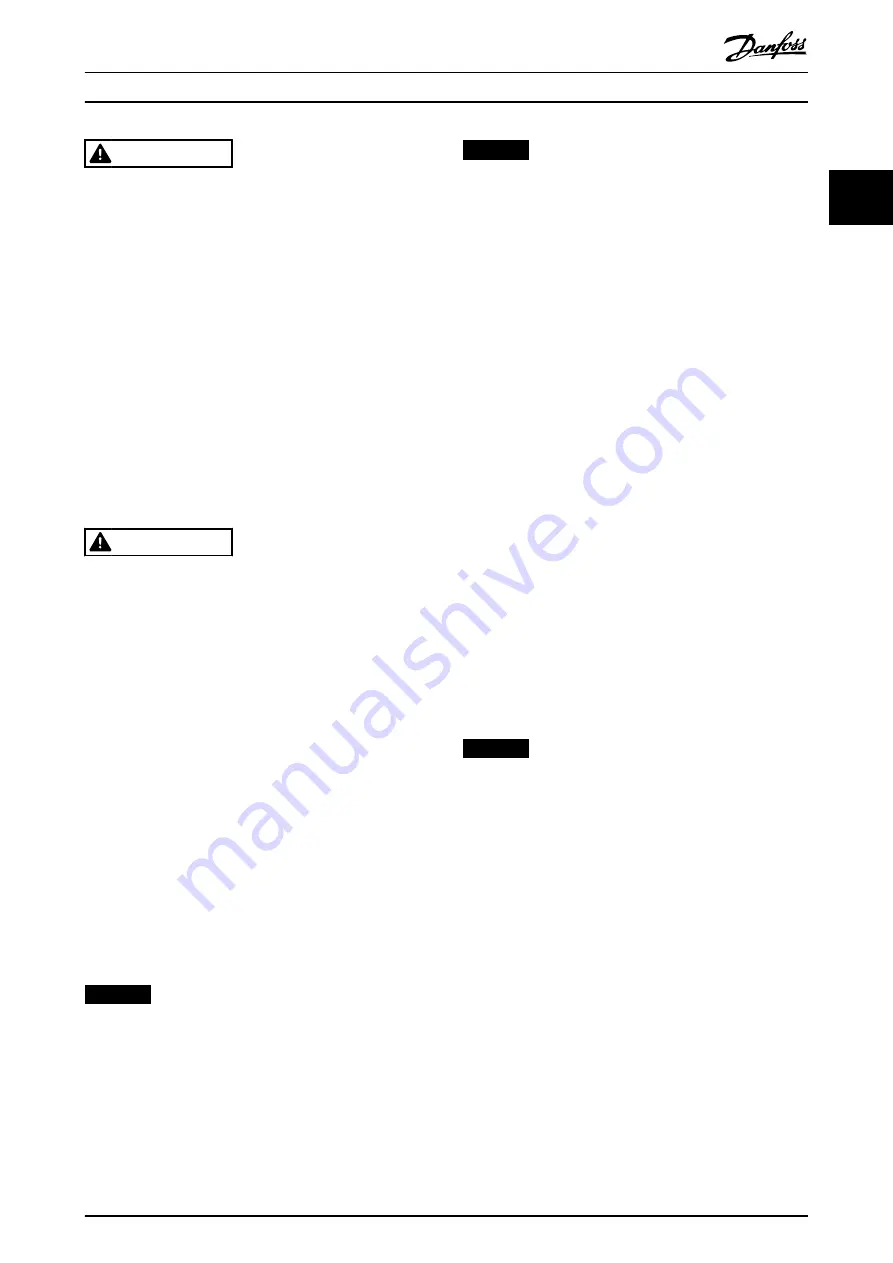
WARNING
UNINTENDED START
When the frequency converter is connected to AC mains,
DC supply, or load sharing, the motor may start at any
time. Unintended start during programming, service, or
repair work can result in death, serious injury, or
property damage. The motor can start via an external
switch, a serial bus command, an input reference signal
from the LCP, or after a cleared fault condition.
To prevent unintended motor start:
•
Disconnect the frequency converter from the
mains.
•
Press [Off/Reset] on the LCP before
programming parameters.
•
Completely wire and assemble the frequency
converter, motor, and any driven equipment
before connecting the frequency converter to
AC mains, DC supply, or load sharing.
WARNING
DISCHARGE TIME
The frequency converter contains DC-link capacitors,
which can remain charged even when the frequency
converter is not powered. High voltage can be present
even when the warning LED indicator lights are off.
Failure to wait the specified time after power has been
removed before performing service or repair work can
result in death or serious injury.
•
Stop the motor.
•
Disconnect AC mains and remote DC-link power
supplies, including battery back-ups, UPS, and
DC-link connections to other frequency
converters.
•
Disconnect or lock PM motor.
•
Wait for the capacitors to discharge fully. The
minimum waiting time is 20 minutes.
•
Before performing any service or repair work,
use an appropriate voltage measuring device to
make sure that the capacitors are fully
discharged.
NOTICE
Control signals from, or internally within, the frequency
converter may in rare cases be activated in error, be
delayed, or fail to occur entirely. When used in situations
where safety is critical, for example when controlling the
electromagnetic brake function of a hoist application, do
not rely on these control signals exclusively.
NOTICE
Hazardous situations must be identified by the machine
builder/integrator who is responsible for considering the
necessary preventive means. More monitoring and
protective devices may be included, always according to
valid national safety regulations, for example law on
mechanical tools and regulations for the prevention of
accidents.
Crane, lifts, and hoists
The controlling of external brakes must always have a
redundant system. The frequency converter can in no
circumstances be the primary safety circuit. Comply with
relevant standards, for example:
Hoists and cranes: IEC 60204-32.
Lifts: EN 81.
Protection mode
Once a hardware limit on motor current or DC-link voltage
is exceeded, the frequency converter enters the protection
mode. Protection mode means a change of the PWM
strategy and a low switching frequency to minimize losses.
This continues for 10 s after the last fault and increases the
reliability and the robustness of the frequency converter
while re-establishing full control of the motor.
In hoist applications, protection mode is not usable
because the frequency converter is unable to leave this
mode again and therefore it extends the time before
activating the brake, which is not recommended.
Protection mode can be disabled by setting
parameter 14-26 Trip Delay at Inverter Fault
to 0, which
means that the frequency converter trips immediately if 1
of the hardware limits is exceeded.
NOTICE
Disabling protection mode in hoisting applications
(
parameter 14-26 Trip Delay at Inverter Fault
= 0) is
recommended.
Safety
Programming Guide
MG06J202
Danfoss A/S © 03/2019 All rights reserved.
11
2
2
Summary of Contents for VLT AutomationDrive FC 361
Page 2: ......