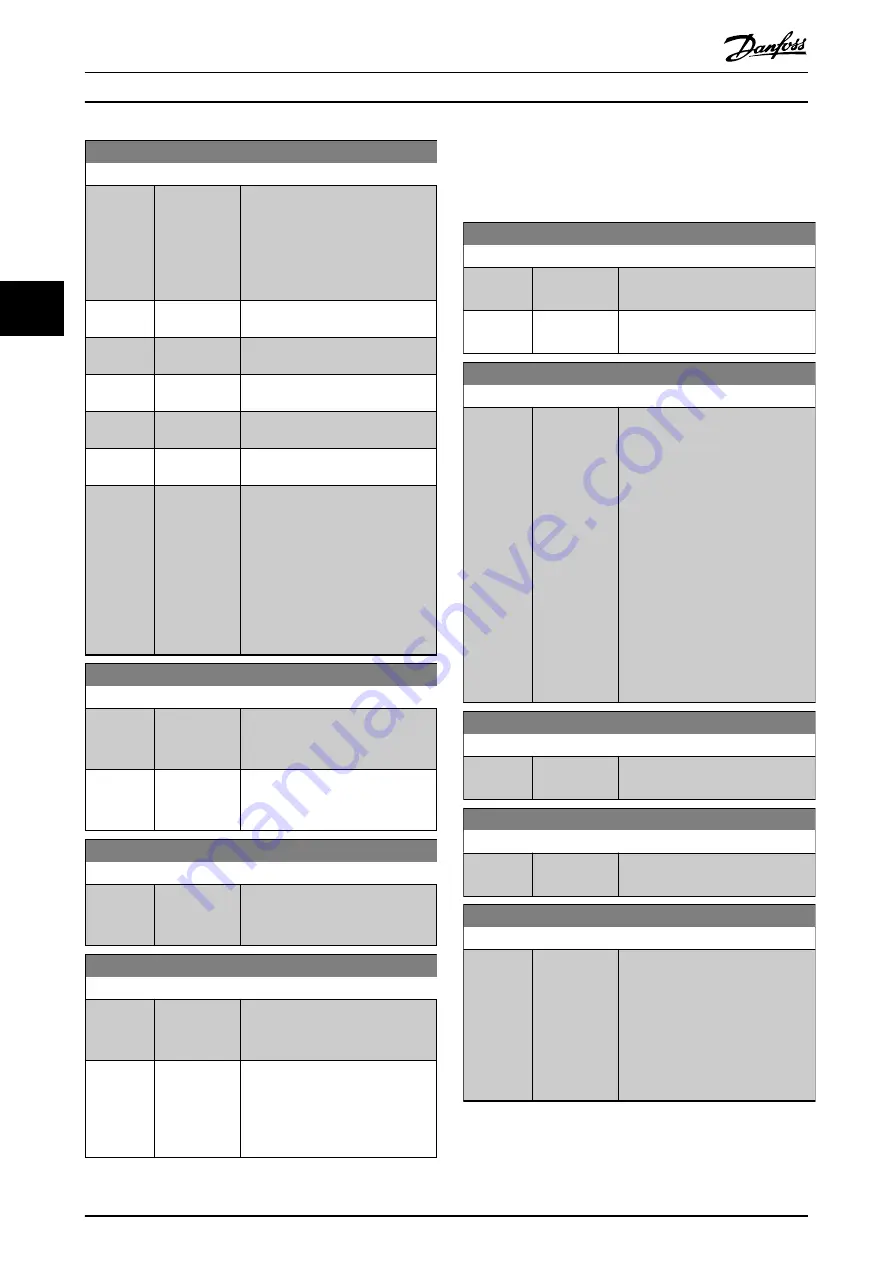
7-45 Process PID Feed Fwd Resource
Option:
Function:
[0]
*
No function
Select which frequency converter
input should be used as the feed-
forward factor. The factor is added
to the output of the PID controller.
This increases dynamic
performance.
[1]
Analog Input
53
[2]
Analog Input
54
[7]
Frequency
input 29
[8]
Frequency
input 33
[11]
Local bus
reference
[32]
Bus PCD
Selects a fieldbus reference
configured by
parameter 8-02 Control Word Source
.
Change
parameter 8-42 PCD Write
Configuration
for the bus used to
make the feed forward available in
parameter 7-48 PCD Feed Forward
Use index 1 for feed forward [748]
(and index 2 for reference [1682]).
7-46 Process PID Feed Fwd Normal/ Inv. Ctrl.
Option:
Function:
[0]
*
Normal
Select
[0] Normal
to set the feed-
forward factor to treat the FF
resource as a positive value.
[1]
Inverse
Select
[1] Inverse
to treat the feed-
forward resource as a negative
value.
7-48 PCD Feed Forward
Range:
Function:
0
*
[0 - 65535]
This parameter contains the value
of
parameter 7-45 Process PID Feed
Fwd Resource
[32] Bus PCD
.
7-49 Process PID Output Normal/ Inv. Ctrl.
Option:
Function:
[0]
*
Normal
Select
[0] Normal
to use the
resulting output from the process
PID controller as is.
[1]
Inverse
Select
[1] Inverse
to invert the
resulting output from the process
PID controller. This operation is
performed after the feed-forward
factor is applied.
4.8.5 7-5* Ext. Process PID Ctrl.
This parameter group is only used if
parameter 1-00 Config-
uration Mode
is set to
[7] Extended PID speed CL
.
7-50 Process PID Extended PID
Option:
Function:
[0]
Disabled
Disable the extended parts of the
process PID controller.
[1]
*
Enabled
Enable the extended parts of the
PID controller.
7-51 Process PID Feed Fwd Gain
Range:
Function:
1
*
[0 - 100]
The feed forward is used to obtain
the required level based on a well-
known signal available. The PID
controller then only takes care of
the smaller part of the control,
necessary because of unknown
characters. The standard feed-
forward factor in
parameter 7-38 Process PID Feed
Forward Factor
is always related to
the reference, whereas
parameter 7-51 Process PID Feed Fwd
Gain
has more options. In winder
applications, the feed-forward factor
is typically the line speed of the
system.
7-52 Process PID Feed Fwd Ramp up
Range:
Function:
0.01 s
*
[0.01 - 10 s]
Controls the dynamics of the feed-
forward signal when ramping up.
7-53 Process PID Feed Fwd Ramp down
Range:
Function:
0.01 s
*
[0.01 - 10 s]
Controls the dynamics of the feed-
forward signal when ramping down.
7-56 Process PID Ref. Filter Time
Range:
Function:
0.001 s
*
[0.001 - 1 s]
Set a time constant for the
reference first-order low-pass filter.
The low-pass filter improves steady-
state performance and dampens
oscillations on the reference/
feedback signals. However, severe
filtering can be detrimental to
dynamic performance.
Parameter Descriptions
VLT® AutomationDrive FC 361
92
Danfoss A/S © 03/2019 All rights reserved.
MG06J202
4
4
Summary of Contents for VLT AutomationDrive FC 361
Page 2: ......