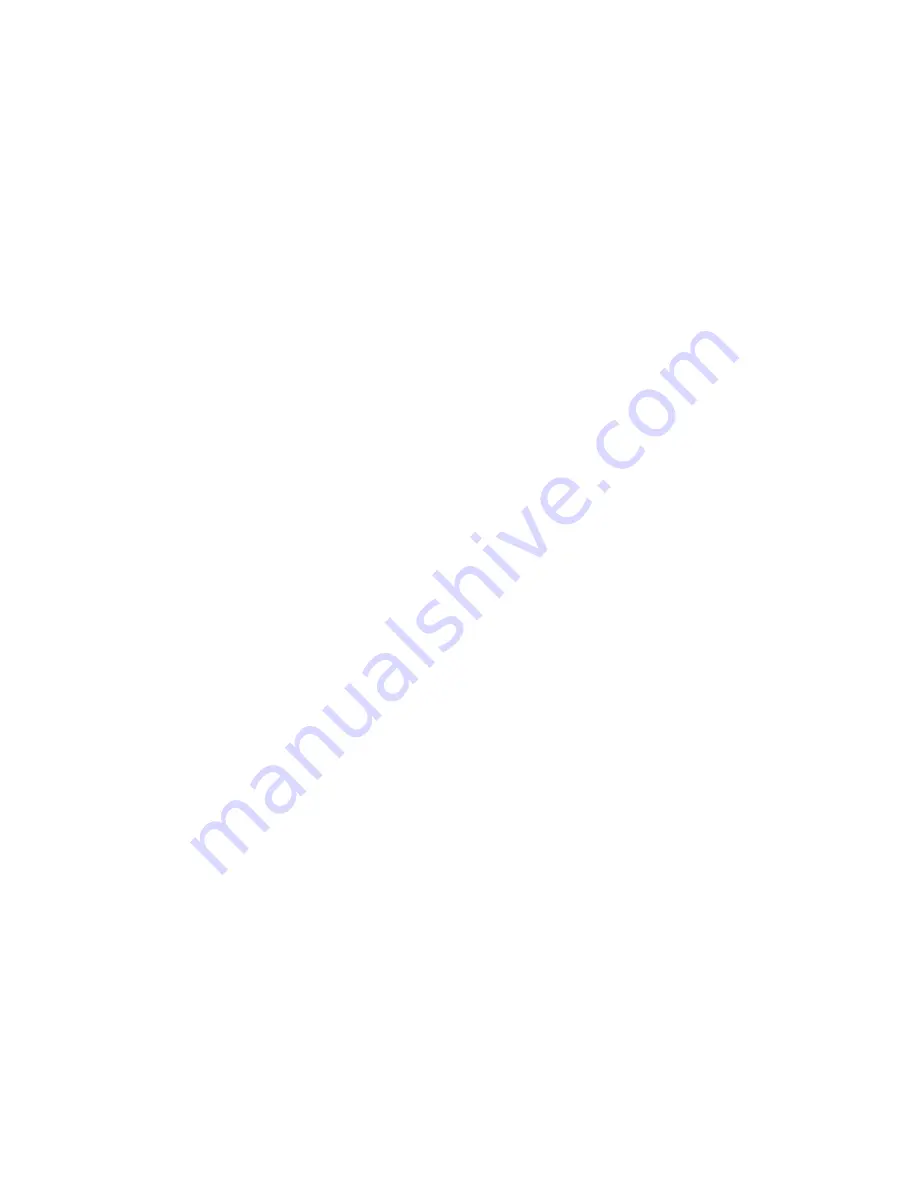
130
The fuel injection by new injector is accompanied by a charac-
teristic sharp sound. The absence of a sharp sound for used ones does
not mean reduction of quality of their work.
5
The tightness of sealing, joint and outside surfaces of low
pressure cavity check with compressed air with pressure 0,45
±
0,05
MPa (4,5
±
0,5 kgf/cm
2
). The passing of air during 10 seconds is not
permitted at air inlet from the side of a sprayer tip.
6
The tightness of “spray tip – spray tip nut” joints check by
compressed air with pressure 0,5
±
0,1 MPa (5
±
1 kfg/cm
2
) within 10
seconds at air inlet from the side of spray tip. The outlet of air bulbs
through spray nut thread at immersing it in diesel fuel is not permitted.
At the carbonising either contamination one or several spray tip
nozzles disassemble the injector, clean its details and carefully wash
out in the clean diesel fuel.
At absence of tightness on a locking cone the spray tip as unit
should be changed. The changing of separate details of the sprayer is
not allowed.
Injector disassembly carry out in the following sequence:
Injectors of 267-03, 261-11 models:
1
unscrew the injector cap;
2
unscrew the lock nut and unscrew against stop the adjusting
screw;
3
unscrew the spring nut on 1,5 - 2 revolutions;
4
unscrew the spray tip nut;
5
take off spray tip, having protected sprayer needle from drop
- out.
Injector of model 51:
1
unscrew the sprayer nut;
2
take off spray, having protected spray needle from drop -
out.
The carbon deposits from the spray tip case clean off by a metal
brush or emery paper with granularity not more rough than "M40"
.
The sprayer nozzles clean (fig. 67) with steel wire by a diameter
of 0,3 mm (for spray tip of 267-03, 261-11 injector models) and diame-
ter of 0,28 mm (for a spray tip of 51 injector model). Apply to clean
the internal cavities of the spray tip case and needle surfaces firm ma-
terials and emery paper is not permitted.
Summary of Contents for ???-238??
Page 18: ...18 Fig 4 Overall Dimensions of Power Units 238 2 238 238 2 238 18...
Page 20: ...20 Fig 6 Engine Longi tudinal Section...
Page 38: ...38...
Page 213: ...213...
Page 225: ...225...