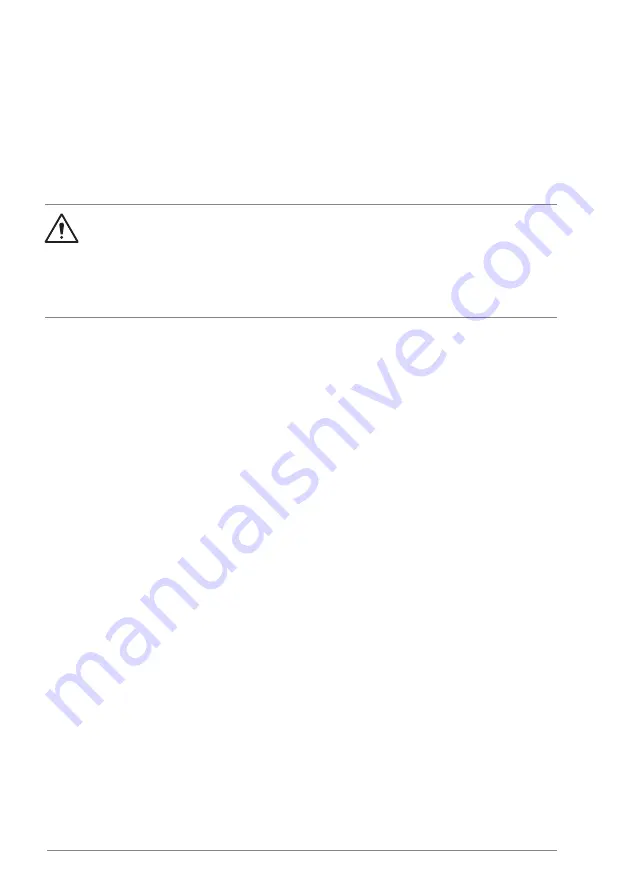
, the position values are retained over an error or
reboot; bit 6 of
is set however to indicate that an error occurred.
Note: With a multiturn absolute encoder, bit 6 of
is cleared at the next stop
of the drive if the encoder has recovered from the error; bit 4 is not cleared. The
status of the position counter is retained over a control unit reboot, after which
position calculation resumes from the absolute position given by the encoder,
taking into account the initial position specified by
WARNING!
If the drive is in stopped state when an encoder error occurs, or if the drive
is not powered, parameters
,
and
are not updated
because no movement of the load can be detected. When using previous
position values (
is set to
), be aware that
the position data is unreliable if the load is able to move.
Reading/writing position counter values through fieldbus
The parameters of the position counter function, such as
and
, can be
accessed from an upper-level control system in the following formats:
•
16-bit integer (if 16 bits are sufficient for the application)
•
32-bit integer (can be accessed as two consequent 16-bit words).
For example, to read parameter
through fieldbus, set the selection parameter
of the desired dataset (in group
) to Other –
, and select the format. If you
select a 32-bit format, the subsequent data word is also automatically reserved.
Configuration of HTL encoder motor feedback
1.
Specify the type of the encoder interface module (parameter
=
)
and the slot the module is installed into (
).
2.
Specify the type of the encoder (
=
). The parameter listing will be
re-read from the drive after the value is changed.
3.
Specify the interface module that the encoder is connected to (
=
).
4. Set the number of pulses according to encoder nameplate (
).
5. If the encoder rotates at a different speed to the motor (ie. is not mounted
directly on the motor shaft), enter the gear ratio in
and
.
6. Set parameter
to
to apply the new parameter settings. The
parameter will automatically revert to
7.
Check that
is showing the correct interface module type (
). Also
check the status of the module; both LEDs should be glowing green.
8. Start the motor with a reference of eg. 400 rpm.
96 Program features
Summary of Contents for ACS880 Series
Page 1: ... ABB INDUSTRIAL DRIVES ACS880 ESP control program option N5600 Firmware manual ...
Page 2: ......
Page 4: ......
Page 16: ...16 ...
Page 22: ...22 ...
Page 24: ...24 ...
Page 44: ...44 ...
Page 66: ...66 ...
Page 148: ...148 ...
Page 168: ...168 ...
Page 704: ...704 ...
Page 728: ...728 ...
Page 742: ...742 ...
Page 762: ...762 ...