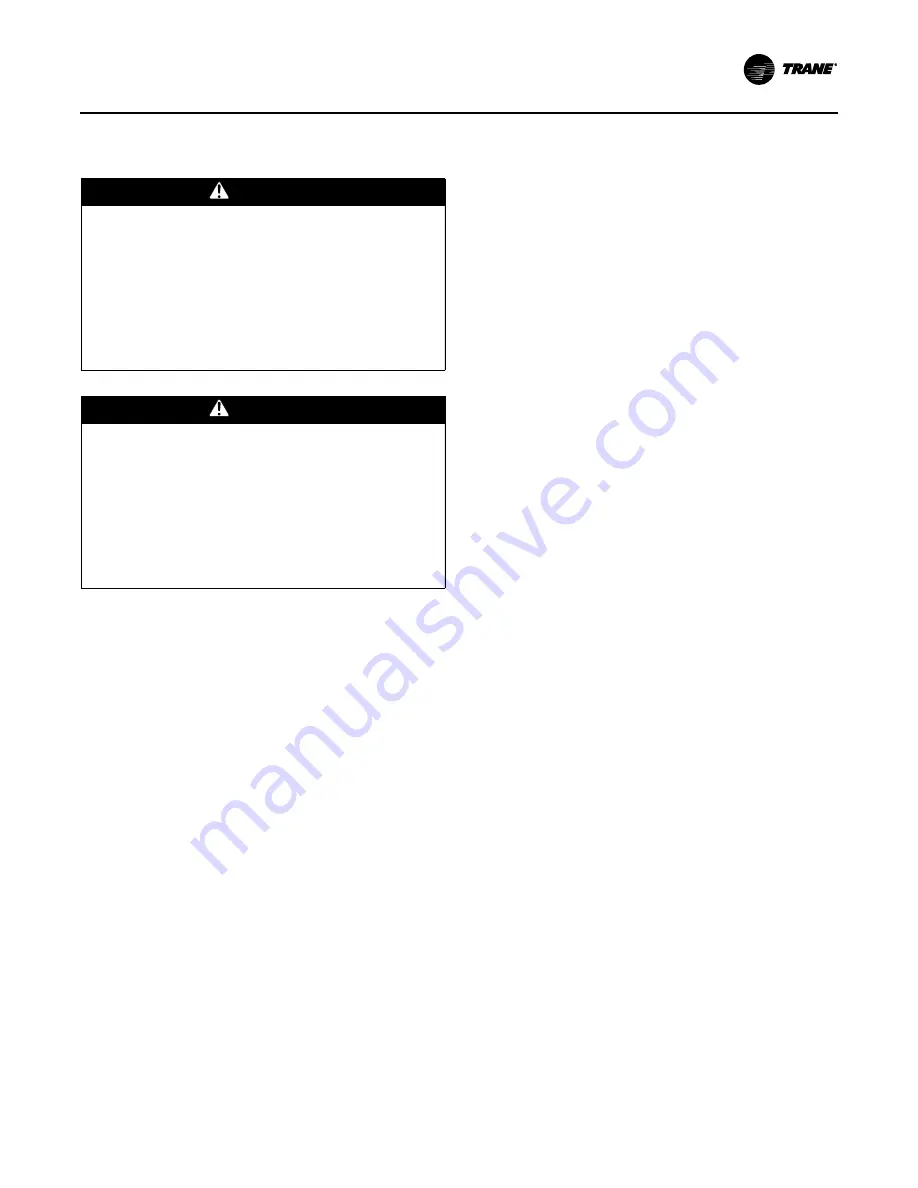
Unit Startup
RT-SVX24J-EN
165
monoxide, and a steady flame that minimizes nuisance
shutdowns.
Two Stage Gas Furnace
High-Fire Adjustment
1.
Use
Table 37, p. 110
to program the following system
components for operation by scrolling through the
Human Interface displays;
Gas Heat
Supply Fan (On)
Return Fan (On, if supplied)
Variable Frequency Drive (100% Output, if applicable)
RTM Occ/Unocc Output (Unoccupied)
Heat Stages 1 & 2 (On)
Turn the 115 volt control circuit switch 4S24 located in
the heater control panel to the “On” position.
Open the manual gas valve, located in the gas heat
section.
2. Once the configuration for the appropriate heating
system is complete, press the NEXT key until the LCD
displays the “Start test in __Sec.” screen. Press the +
key to designate the delay before the test is to start.
This service test will begin after theTEST START key is
pressed and the delay designated in this step has
elapsed. Press the ENTER key to confirm this choice.
3. Press theTEST START key to start the test. Remember
that the delay designated in step 2 must elapse before
the system will begin to operate.
4. Once the system has started, check the appearance of
the flame through the sight glass provided on the front
of the heat exchanger. In appearance, a normal flame
has a clearly defined shape, and is primarily (75%) blue
in color with an orange tip.
5. Check the manifold gas pressure by using the manifold
pressure port on the gas valve. Refer to
Table 48, p. 166
for the required manifold pressure for high-fire
operation. If it needs adjusting, remove the cap
covering the high-fire adjustment screw on the gas
valve. Refer to
Figure 118, p. 167
for the adjustment
screw location. Turn the screw clockwise to increase
the gas pressure or counterclockwise to decrease the
gas pressure.
6. Use a carbon dioxide analyzer and measure the
percentage of carbon dioxide in the flue gas. Refer to
the illustration in
Figure 117, p. 167
. Take several
samples to assure that an accurate reading is obtained.
Refer to
Figure 116, p. 166
for the proper carbon
dioxide levels. A carbon dioxide level exceeding the
listed range indicates incomplete combustion due to
inadequate air or excessive gas.
Combustion Air Adjustment (O
2
)
7.
Use an oxygen analyzer and measure the percentage
of oxygen in the flue gas. Take several samples to
assure an accurate reading. Compare the measured
oxygen level to the combustion curve in
Figure 116,
p. 166
. The oxygen content of the flue gas should be
4% to 5%. If the oxygen level is outside this range,
adjust the combustion air damper to increase or
decrease the amount of air entering the combustion
chamber. Refer to
Figure 120, p. 169
for the location of
the combustion air damper.
8. Recheck the oxygen and carbon dioxide levels after
each adjustment. After completing the high-fire
checkout and adjustment procedure, the low-fire
setting may require adjusting.
Low-Fire Adjustment
(850 & 1100 MBH only)
1.
Use the TEST initiation procedures outlined in the
previous section to operate the furnace in the low-fire
state (1st Stage).
2. Use a carbon dioxide analyzer and measure the
percentage of carbon dioxide in the flue gas. Refer to
the illustration in
Figure 116, p. 166
, Inset A. Take
several samples to assure that an accurate reading is
obtained. Refer to
Table 48, p. 166
for the proper
carbon dioxide levels. If the measured carbon dioxide
level is within the listed values, no adjustment is
necessary. A carbon dioxide level exceeding the listed
range indicates incomplete combustion due to
inadequate air or excessive gas.
3. Check the manifold gas pressure by using the manifold
pressure port on the gas valve. Refer to
Table 48, p. 166
WARNING
Hazardous Gases and Flammable Vapors!
Exposure to hazardous gases from fuel substances
have been shown to cause cancer, birth defects or other
reproductive harm. Improper installation, adjustment,
alteration, service or use of this product could cause
flammable mixtures and result in a fire. To avoid
hazardous gases and flammable vapors follow proper
installation and set up of this product and all warnings
as provided in this manual. Failure to follow all
instructions could result in death or serious injury.
WARNING
Hazardous Pressures!
When using dry nitrogen cylinders for pressurizing
units for leak testing, always provide a pressure
regulator on the cylinder to prevent excessively high
unit pressures. Never pressurize unit above the
maximum recommended unit test pressure as specified
in applicable unit literature. Failure to properly regulate
pressure could result in a violent explosion, which
could result in death or serious injury or equipment or
property-only-damage.
Содержание SEHJ090-162
Страница 40: ...Dimensional Data 40 RT SVX24J EN Figure 13 Evaporative condenser water connection locations RIGHT SIDE VIEW ...
Страница 48: ...Installation 48 RT SVX24J EN Figure 18 Ductwork conversion ...
Страница 58: ...Installation 58 RT SVX24J EN Figure 36 5 Connected tubes 6 install panels Connected tubes 5 6 ...
Страница 75: ...Installation RT SVX24J EN 75 Figure 51 Hot water coil piping Figure 52 Steam coil piping ...
Страница 87: ...Installation RT SVX24J EN 87 Figure 57 Typical field wiring diagram for 90 to 162 ton CV control options ...
Страница 89: ...Installation RT SVX24J EN 89 Figure 59 Typical field wiring diagram for 90 to 162 ton VAV control options ...