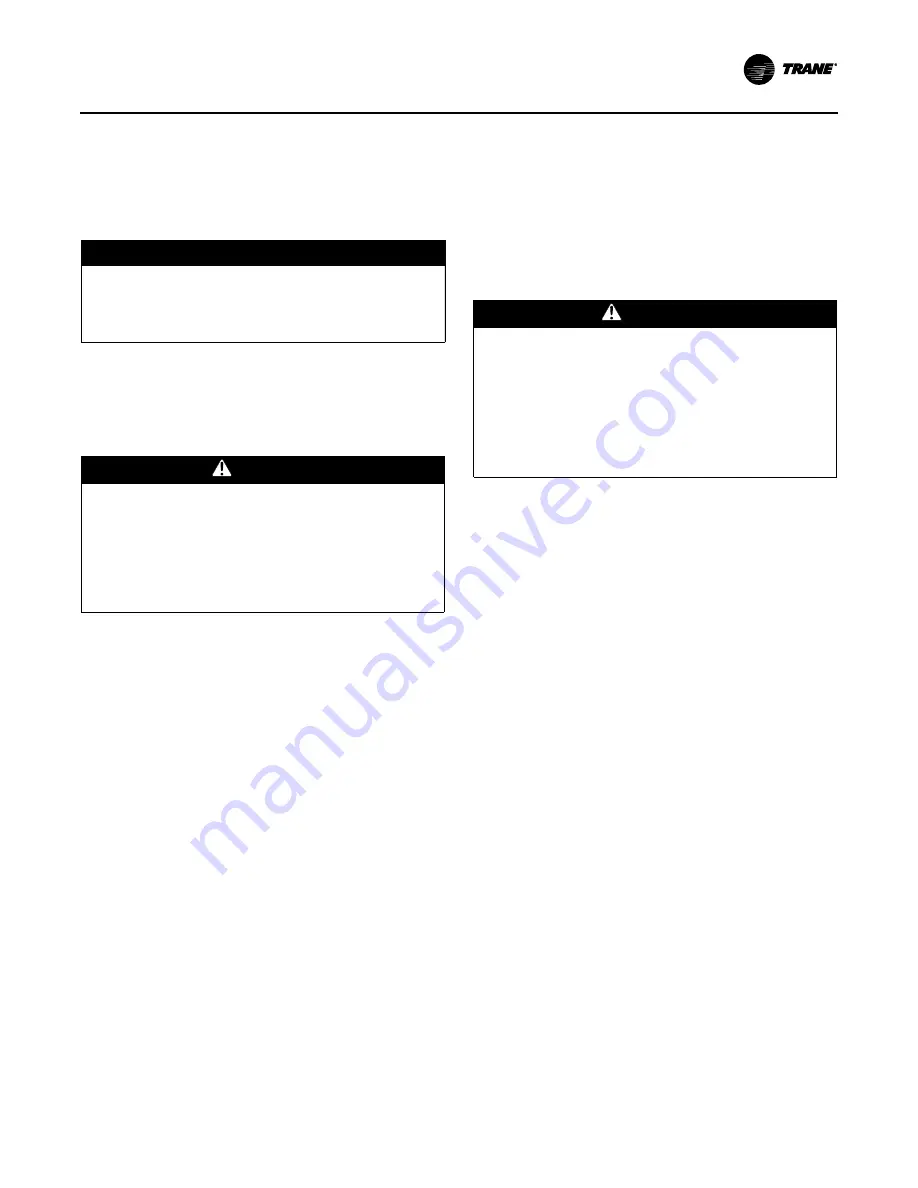
Unit Startup
RT-SVX24J-EN
159
8. Tighten the set screw to the drive shaft.
9. Stretch the belt over the pulley and engage it in the
groove.
Compressor Startup
1.
Ensure that the “System” selection switch at the
remote panel is in the “Off” position.
2. Before closing the disconnect switch, ensure that the
compressor discharge service valve and the liquid line
service valve for each circuit is back seated.
3. Close the disconnect switch or circuit protector switch
that provides the supply power to the unit terminal
block or the unit mounted disconnect switch to allow
the crankcase heater to operate a minimum of 8 hours
before continuing.
4. Turn the 115 volt control circuit switch and the 24 volt
control circuit switch to the “On” position.
5. Open the Human Interface access door, located in the
unit control panel, and press the SERVICE MODE key to
display the first service screen. Refer to the latest
edition of the applications programming guide for
applications for the SERVICE TEST screens and
programming instructions.
6. Use
Table 37, p. 110
to program the following system
components for operation by scrolling through the
displays;
Compressors
Compressor 1A (On)
Compressor 1B (Off)
Compressor 2A(Off)
Compressor 2B (Off)
Condenser Fans
1. Attach a set of service gauges onto the suction and
discharge gauge ports for each circuit.
See
Figure 115, p. 163
for the various compressor
locations.
2. Once the configuration for the components is
complete, press the NEXT key until the LCD displays
the “Start test in __Sec.” screen. Press the + key to
designate the delay before the test is to start. This
service test will begin after the TEST START key is
pressed and the delay designated in this step has
elapsed. Press the ENTER key to confirm this choice.
3. Press theTEST START key to start the test. Remember
that the delay designated in step 8 must elapse before
the system will begin to operate.
4. Once each compressor or compressor pair has started,
verify that the rotation is correct. If a scroll compressor
is rotating backwards, it will not pump and a loud
rattling sound can be observed. Check the electrical
phasing at the load side of the compressor contactor.
If the phasing is correct, before condemning the
compressor, interchange any two leads to check the
internal motor phasing. If the compressor runs
backward for an extended period (15 to 30 minutes),
the motor winding can over heat and cause the motor
winding thermostats to open. This will cause a
“compressor trip” diagnostic and stop the
compressor.
5. Press the STOP key at the Human Interface Module in
the unit control panel to stop the compressor
operation.
6. Repeat steps 5 through 11 for each compressor stage
and the appropriate condenser fans.
Refrigerant Charging
1. Attach a set of service gauges onto the suction and
discharge gauge ports for each circuit.
See
Figure 115, p. 163
for the various compressor
locations.
2. Open the Human Interface access door, located in the
unit control panel, and press the SERVICE MODE key to
display the first service screen. Refer to the latest
edition of the applications programming guide for CV
or VAV applications for the SERVICETEST screens and
programming instructions.
NOTICE:
Compressors Failure!
Unit must be powered and crankcase heaters energized
at least 8 hours BEFORE compressors are started. This
will protect the compressors from premature failure.
CAUTION
Compressor Damage!
Do not allow liquid refrigerant to enter the suction line.
Excessive liquid accumulation in the liquid lines could
result in compressor damage.
COMPRESSOR SERVICE VALVES MUST BE FULLY
OPENED BEFORE STARTUP (SUCTION, DISCHARGE,
LIQUID LINE, AND OIL LINE).
WARNING
Rotating Components!
The following procedure involves working with
rotating components. Disconnect all electric power,
including remote disconnects before servicing. Follow
proper lockout/tagout procedures to ensure the power
can not be inadvertently energized. Failure to
disconnect power before servicing could result in
rotating components cutting and slashing technician
which could result in death or serious injury.
Содержание SEHJ090-162
Страница 40: ...Dimensional Data 40 RT SVX24J EN Figure 13 Evaporative condenser water connection locations RIGHT SIDE VIEW ...
Страница 48: ...Installation 48 RT SVX24J EN Figure 18 Ductwork conversion ...
Страница 58: ...Installation 58 RT SVX24J EN Figure 36 5 Connected tubes 6 install panels Connected tubes 5 6 ...
Страница 75: ...Installation RT SVX24J EN 75 Figure 51 Hot water coil piping Figure 52 Steam coil piping ...
Страница 87: ...Installation RT SVX24J EN 87 Figure 57 Typical field wiring diagram for 90 to 162 ton CV control options ...
Страница 89: ...Installation RT SVX24J EN 89 Figure 59 Typical field wiring diagram for 90 to 162 ton VAV control options ...