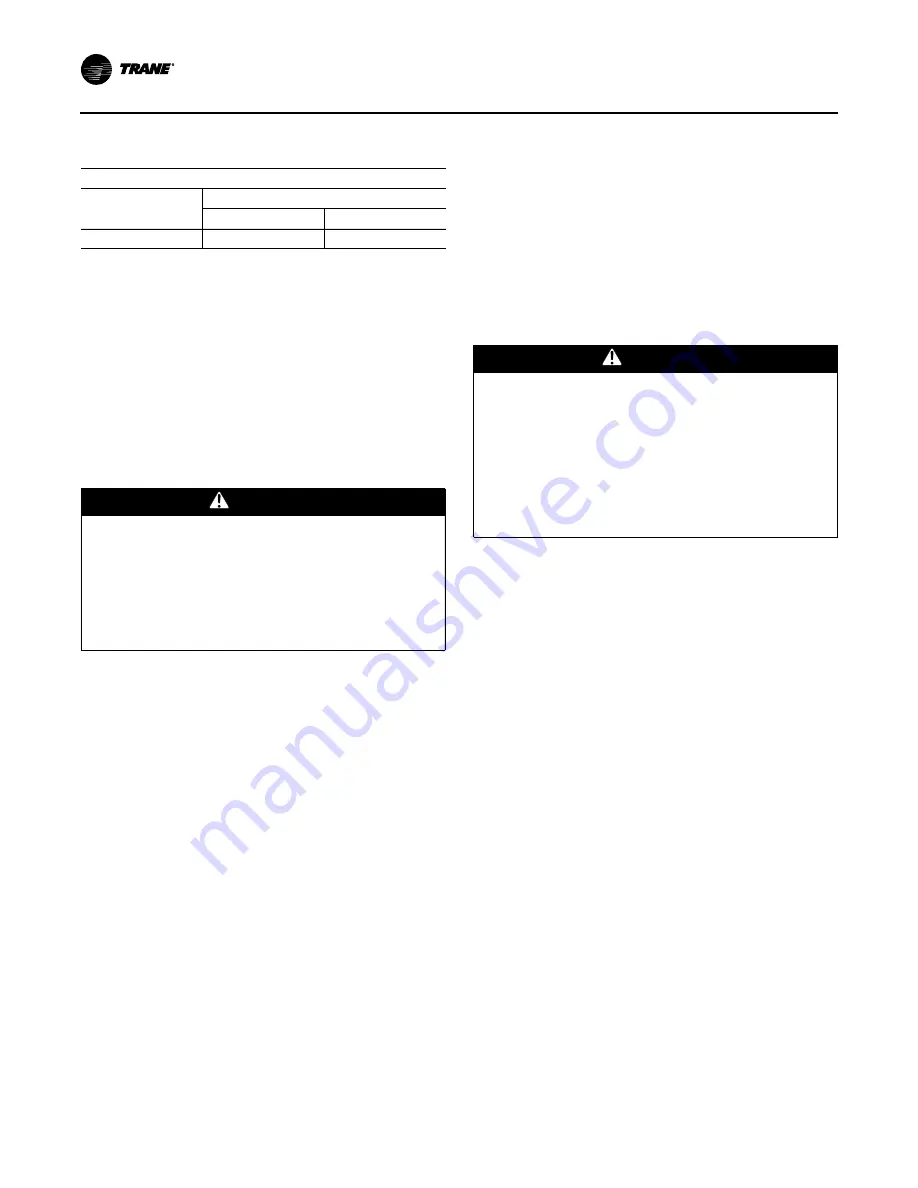
Unit Startup
164
RT-SVX24J-EN
Electric, Steam and Hot Water Startup
(Constant Volume & Variable Air Volume
Systems)
1.
Ensure that the “System” selection switch at the
remote panel is in the “Off” position.
2. Close the disconnect switch or circuit protector switch
that provides the supply power to the unit terminal
block or the unit mounted disconnect switch.
HIGH VOLTAGE IS PRESENT AT TERMINAL BLOCK OR
UNIT DISCONNECT SWITCH.
3. Turn the 115 volt control circuit switch and the 24 volt
control circuit switch to the “On” position.
4. Open the Human Interface access door, located in the
unit control panel, and press the SERVICE MODE key to
display the first service screen. Refer to the latest
edition of the appropriate programming manual for CV
or VAV applications for the SERVICETEST screens and
programming instructions.
5. Use
Table 37, p. 110
to program the following system
components for operation by scrolling through the
Human Interface displays;
Electric Heat
Supply Fan (On)
Variable Frequency Drive (100% Output, if applicable)
RTM Occ/Unocc Output (Unoccupied)
Heat Stages 1 & 2 (On)
Steam or Hot Water Heat
Supply Fan (On)
Variable Frequency Drive (100% Output, if applicable)
RTM Occ/Unocc Output (Unoccupied)
Hydronic Heat Actuator (100% Open)
Open the main steam or hot water valve supplying the
rooftop heater coils.
6. Once the configuration for the appropriate heating
system is complete, press the NEXT key until the LCD
displays the “Start test in __Sec.” screen. Press the +
key to designate the delay before the test is to start.
This service test will begin after theTEST START key is
pressed and the delay designated in this step has
elapsed. Press the ENTER key to confirm this choice.
7.
Press theTEST START key to start the test. Remember
that the delay designated in step 6 must elapse before
the fan will begin to operate.
8. Once the system has started, verify that the electric
heat or the hydronic heat system is operating properly
by using appropriate service technics; i.e. amperage
readings, delta tees, etc.
9. Press the STOP key at the Human Interface Module in
the unit control panel to stop the system operation.
Gas Furnace Startup
(Constant Volume and Variable Air Volume
Systems)
It is important to establish and maintain the appropriate
air/fuel mixture to assure that the gas furnace operates
safely and efficiently.
Since the proper manifold gas pressure for a particular
installation will vary due to the specific BTU content of the
local gas supply, adjust the burner based on carbon
dioxide and oxygen levels.
The volume of air supplied by the combustion blower
determines the amount of oxygen available for
combustion, while the manifold gas pressure establishes
fuel input. By measuring the percentage of carbon dioxide
produced as a by-product of combustion, the operator can
estimate the amount of oxygen used and modify the air
volume or the gas pressure to obtain the proper air/fuel
ratio.
Arriving at the correct air/fuel mixture for a furnace results
in rated burner output, limited production of carbon
Table 47. Minimum ambient
Minimum Starting Ambient
Unit Size
Standard Ambient
with HGBP
without HGBP
90-162
40
55
Notes:
1. Minimum starting ambients in degrees F and is based on unit
operating at min. step of unloading, and unloading and 5 mph wind
across condenser
WARNING
Hazardous Voltage!
Disconnect all electric power, including remote
disconnects before servicing. Follow proper lockout/
tagout procedures to ensure the power can not be
inadvertently energized. Do not open the service access
doors while the unit is operating. Failure to disconnect
power before servicing could result in death or serious
injury.
WARNING
Rotating Components!
During installation, testing, servicing and
troubleshooting of this product it may be necessary to
work with live and exposed rotating components. Have
a qualified or licensed service individual who has been
properly trained in handling exposed rotating
components, perform these tasks. Failure to follow all
safety precautions could result in rotating components
cutting and slashing technician which could result in
death or serious injury.
Содержание SEHJ090-162
Страница 40: ...Dimensional Data 40 RT SVX24J EN Figure 13 Evaporative condenser water connection locations RIGHT SIDE VIEW ...
Страница 48: ...Installation 48 RT SVX24J EN Figure 18 Ductwork conversion ...
Страница 58: ...Installation 58 RT SVX24J EN Figure 36 5 Connected tubes 6 install panels Connected tubes 5 6 ...
Страница 75: ...Installation RT SVX24J EN 75 Figure 51 Hot water coil piping Figure 52 Steam coil piping ...
Страница 87: ...Installation RT SVX24J EN 87 Figure 57 Typical field wiring diagram for 90 to 162 ton CV control options ...
Страница 89: ...Installation RT SVX24J EN 89 Figure 59 Typical field wiring diagram for 90 to 162 ton VAV control options ...