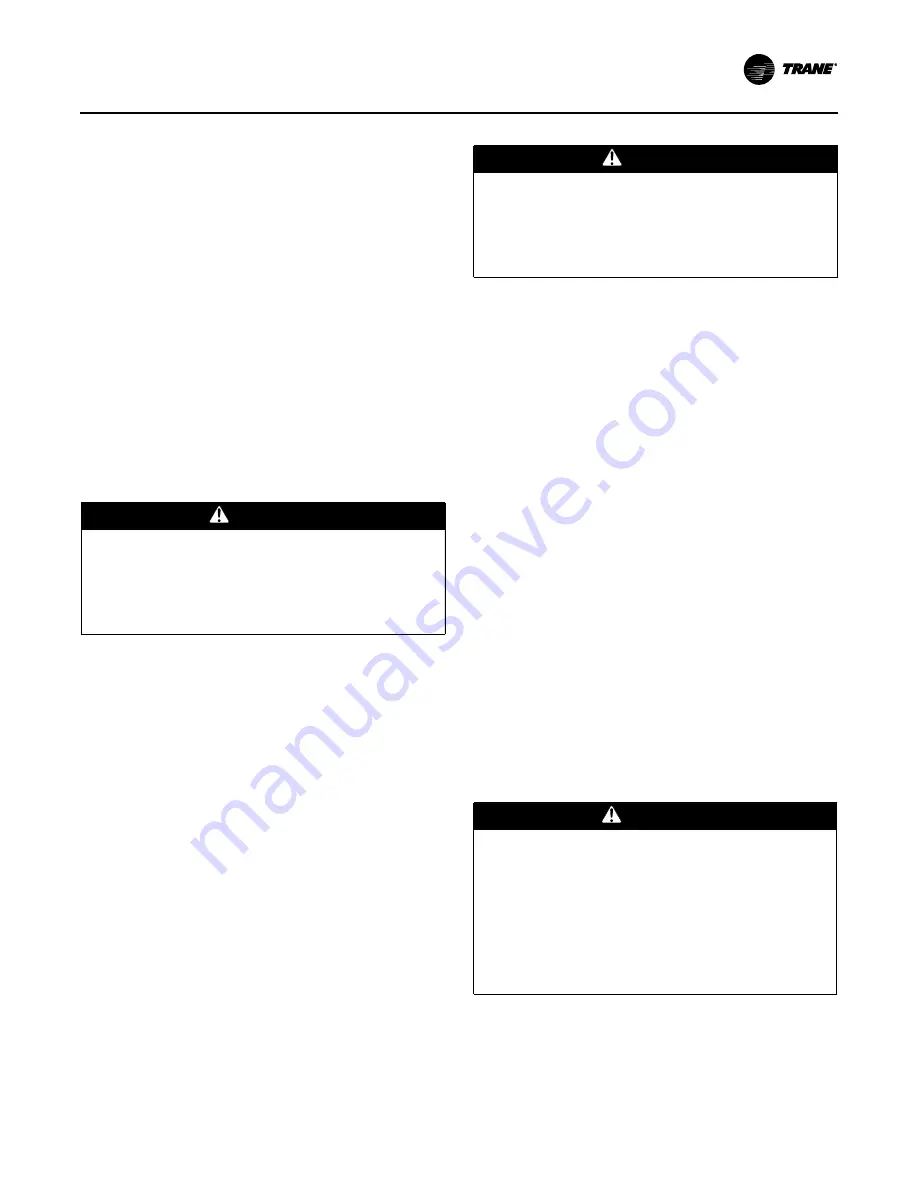
Unit Startup
RT-SVX24J-EN
143
Components
Standard Unit without Energy Recovery
Wheel
Economizer Damper Adjustment
Exhaust Air Dampers
Verify that the exhaust dampers (if equipped) close tightly
when the unit is off. Adjust the damper linkage as
necessary to ensure proper closure. An access panel is
provided under each damper assembly.
Outside Air & Return Air Damper Operation
The outside air and return air damper linkage is accessible
from the filter section of the unit. The damper linkage
connecting the outside air dampers to the return air
dampers is preset from the factory in the number 1
position. Refer to
Figure 102, p. 144
for the appropriate
linkage position for the unit and operating airflow (CFM).
Note:
Bridging between the unit main supports may
consist of multiple 2 by 12 boards or sheet metal
grating.
Arbitrarily adjusting the outside air dampers to open fully
when the return air dampers are closed or; failing to
maintain the return air pressure drop with the outside air
dampers when the return air dampers are closed, can
overload the supply fan motor and cause building
pressurization control problems due to improper CFM
being delivered to the space.
The outside air/return air damper linkage is connected to
a crank arm with a series of holes that allows the installer
or operator to modify the amount of outside air damper
travel in order to match the return static pressure. Refer to
Table 43, p. 146
for the equivalent return air duct losses
that correspond to each of the holes illustrated in
Figure 102, p. 144
.
To Adjust the Outside Air Damper Travel:
1.
Drill a 1/4" hole through the unit casing up stream of
the return air dampers. Use a location that will produce
an accurate reading with the least amount of
turbulence. Several locations may be necessary, and
average the reading.
HIGH VOLTAGE IS PRESENT AT TERMINAL BLOCK OR
UNIT DISCONNECT SWITCH.
2. Close the disconnect switch or circuit protector switch
that provides the supply power to the unit terminal
block or the unit mounted disconnect switch.
3. Turn the 115 volt control circuit switch and the 24 volt
control circuit switch to the “On” position.
4. Open the Human Interface access door, located in the
unit control panel, and press the SERVICE MODE key to
display the first service screen. Refer to the latest
edition of the applicable programming manual for
applications for the SERVICE TEST screens and
programming instructions.
5. Use
Table 37, p. 110
to program the following system
components for operation by scrolling through the
displays;
Supply Fan (On)
Variable Frequency Drive (100% Output, if applicable)
RTM Occ/Unocc Output (Unoccupied)
Outside Air Dampers (Closed)
6. Once the configuration for the components is
complete, press the NEXT key until the LCD displays
the “Start test in __Sec.” screen. Press the + key to
designate the delay before the test is to start. This
service test will begin after the TEST START key is
pressed and the delay designated in this step has
elapsed. Press the ENTER key to confirm this choice.
7.
Press theTEST START key to start the test. Remember
that the delay designated in step 6 must elapse before
the fan will begin to operate.
8. With the outside air dampers fully closed and the
supply fan operating at 100% airflow requirements,
WARNING
No Step Surface!
Do not walk on the sheet metal drain pan. Walking on
the drain pan could cause the supporting metal to
collapse, resulting in the operator/technician to fall.
Failure to follow this recommendation could result in
death or serious injury.
WARNING
Hazardous Voltage!
Disconnect all electric power, including remote
disconnects before servicing. Follow proper lockout/
tagout procedures to ensure the power can not be
inadvertently energized. Failure to disconnect power
before servicing could result in death or serious injury.
WARNING
Rotating Components!
During installation, testing, servicing and
troubleshooting of this product it may be necessary to
work with live and exposed rotating components. Have
a qualified or licensed service individual who has been
properly trained in handling exposed rotating
components, perform these tasks. Failure to follow all
safety precautions could result in rotating components
cutting and slashing technician which could result in
death or serious injury.
Содержание SEHJ090-162
Страница 40: ...Dimensional Data 40 RT SVX24J EN Figure 13 Evaporative condenser water connection locations RIGHT SIDE VIEW ...
Страница 48: ...Installation 48 RT SVX24J EN Figure 18 Ductwork conversion ...
Страница 58: ...Installation 58 RT SVX24J EN Figure 36 5 Connected tubes 6 install panels Connected tubes 5 6 ...
Страница 75: ...Installation RT SVX24J EN 75 Figure 51 Hot water coil piping Figure 52 Steam coil piping ...
Страница 87: ...Installation RT SVX24J EN 87 Figure 57 Typical field wiring diagram for 90 to 162 ton CV control options ...
Страница 89: ...Installation RT SVX24J EN 89 Figure 59 Typical field wiring diagram for 90 to 162 ton VAV control options ...