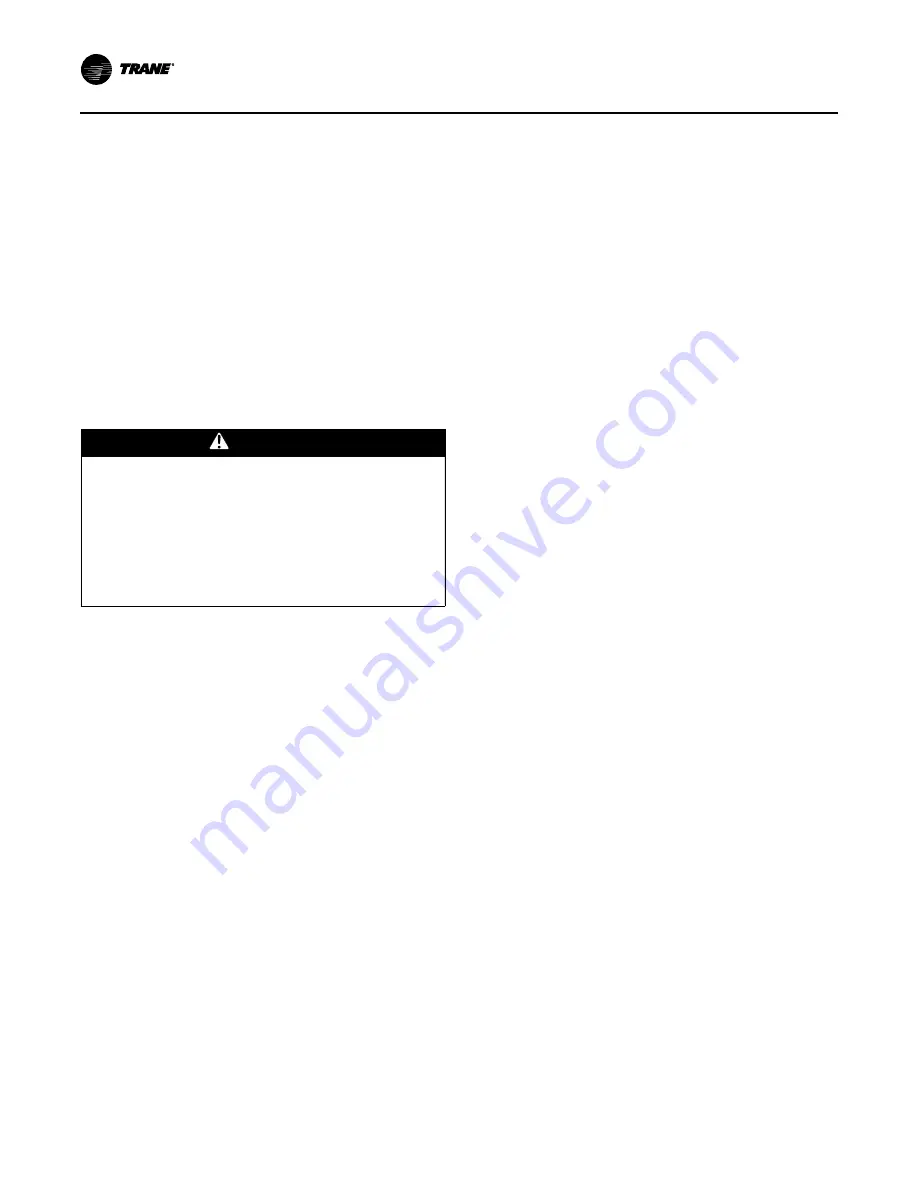
Unit Startup
160
RT-SVX24J-EN
3. Use
Table 37, p. 110
to program the following system
components for the number 1 refrigeration circuit by
scrolling through the displays;
Supply Fan (On)
VFD (100%, if applicable)
OCC/UNOCC Relay (Unoccupied for VAV units)
All Compressors for each circuit (On)
Condenser Fans for each circuit (On)
4. Once the configuration for the components is
complete, press the NEXT key until the LCD displays
the “Start test in __Sec.” screen. Press the + key to
designate the delay before the test is to start. This
service test will begin after the TEST START key is
pressed and the delay designated in this step has
elapsed. Press the ENTER key to confirm this choice.
5. Press theTEST START key to start the test. Remember
that the delay designated in step 4 must elapse before
the system will begin to operate.
6. After all of the compressors and condenser fans for the
number 1 circuit have been operating for
approximately 30 minutes, observe the operating
pressures. Use the appropriate pressure curve
beginning with
Figure 84, p. 134
to determine the
proper operating pressures. For superheat and
subcooling guidelines, refer to “Thermostatic
Expansion Valves and Charging by Subcooling” at the
end of this section.
Note:
Do Not release refrigerant to the atmosphere! If
adding or removing refrigerant is required, the
service technician must comply with all Federal,
State and local laws.
7.
Verify that the oil level in each compressor is correct.
The oil level may be down to the bottom of the
sightglass but should never be above the sightglass.
8. Press the STOP key at the Human Interface Module in
the unit control panel to stop the system operation.
9. Repeat steps 1 through 8 for the number 2 refrigeration
circuit.
10. After shutting the system off, check the compressor oil
appearance. Discoloration of the oil indicates that an
abnormal condition has occurred. If the oil is dark and
smells burnt, it has overheated because: the
compressor is operating at extremely high condensing
temperatures; high superheat; a compressor
mechanical failure; or, occurrence of a motor burnout.
If the oil is black and contains metal flakes, a
mechanical failure has occurred. This symptom is
often accompanied by a high compressor amperage
draw.
If a motor burnout is suspected, use an acid test kit to
check the condition of the oil.Test results will indicate
an acid level exceeding 0.05 mg KOH/g if a burnout
occurred.
The scroll compressor uses Trane OIL00079 (one quart
container) or OIL00080 (one gallon container) without
substitution. The appropriate oil charge for CSHN250
and CSHN315 scroll compressors is 14.2 pints. For
CSHN374 scroll compressor, use 15.2 pints.
Compressor Crankcase Heaters
Each scroll compressor is equipped with a 160-watt
crankcase heater.
Compressor Operational Sounds
Because of the scroll compressor design, it emits a higher
frequency tone (sound) than a reciprocating compressor.
It is designed to accommodate liquids, both oil and
refrigerant, without causing compressor damage. The
following discussion describes some of the operational
sounds that differentiate it from those typically associated
with a reciprocating compressor. These sounds do not
affect the operation or reliability of the compressor.
At Shutdown
When a Scroll compressor shuts down, the gas within the
scroll expands and causes momentary reverse rotation
until the discharge check valve closes. This results in a
“flutter” type sound.
At Low Ambient Startup
When the compressor starts up under low ambient
conditions, the initial flow rate of the compressor is low
due to the low condensing pressure. This causes a low
differential across the thermal expansion valve that limits
its capacity. Under these conditions, it is not unusual to
hear the compressor rattle until the suction pressure
climbs and the flow rate increases.
Note:
Evaporative Condensers ordered with sump
heaters will have low ambient down to 10 deg as
standard
WARNING
Rotating Components!
The following procedure involves working with rotating
components. Disconnect all electric power, including
remote disconnects before servicing. Follow proper
lockout/tagout procedures to ensure the power can not
be inadvertently energized. Failure to disconnect power
before servicing could result in rotating components
cutting and slashing technician which could result in
death or serious injury.
Содержание SEHJ090-162
Страница 40: ...Dimensional Data 40 RT SVX24J EN Figure 13 Evaporative condenser water connection locations RIGHT SIDE VIEW ...
Страница 48: ...Installation 48 RT SVX24J EN Figure 18 Ductwork conversion ...
Страница 58: ...Installation 58 RT SVX24J EN Figure 36 5 Connected tubes 6 install panels Connected tubes 5 6 ...
Страница 75: ...Installation RT SVX24J EN 75 Figure 51 Hot water coil piping Figure 52 Steam coil piping ...
Страница 87: ...Installation RT SVX24J EN 87 Figure 57 Typical field wiring diagram for 90 to 162 ton CV control options ...
Страница 89: ...Installation RT SVX24J EN 89 Figure 59 Typical field wiring diagram for 90 to 162 ton VAV control options ...