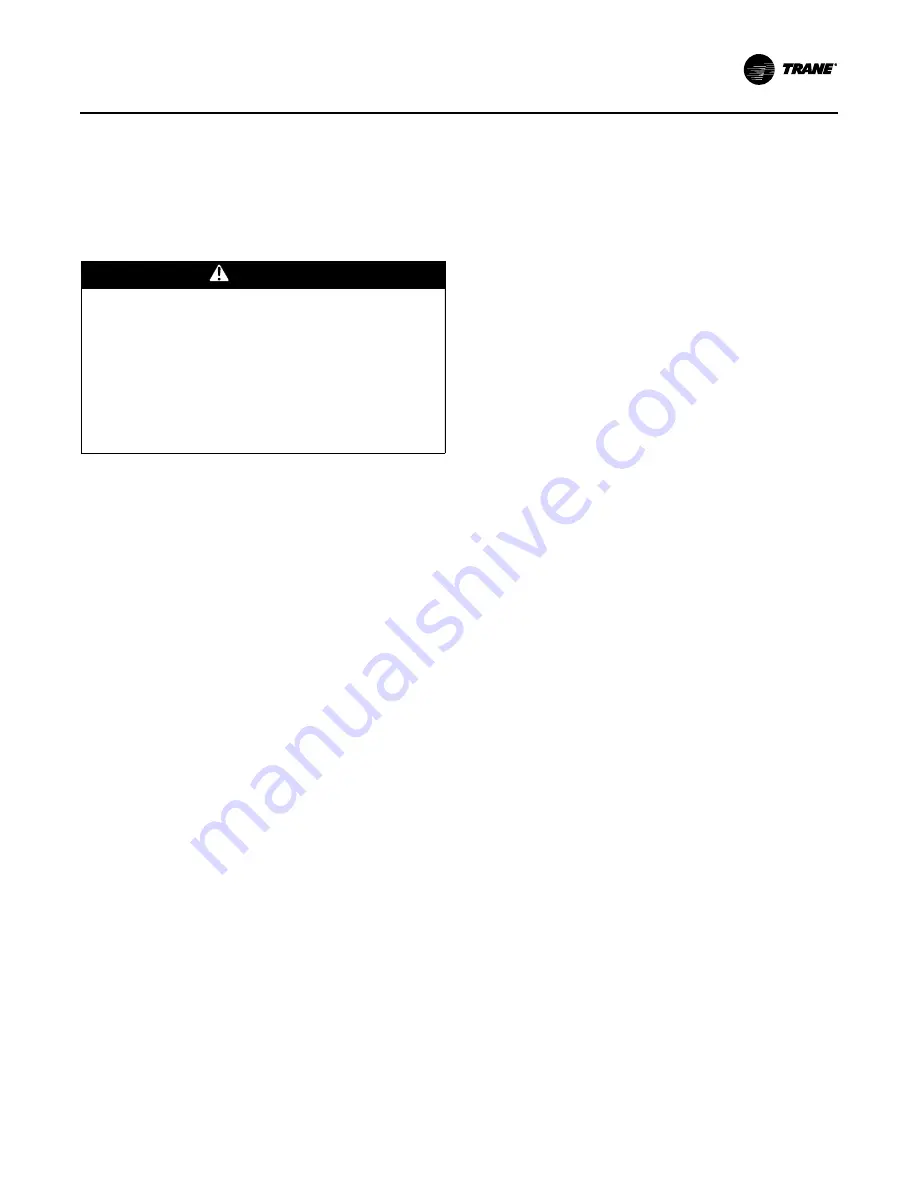
Unit Startup
RT-SVX24J-EN
147
6. Once the configuration for the components is
complete, press the NEXT key until the LCD displays
the “Start test in __Sec." screen. Press the + key to
designate the delay before the test is to start. This
service test will begin after the TEST START key is
pressed and the delay designated in this step has
elapsed. Press the ENTER key to confirm this choice.
7.
Press theTEST START key to start the test. Remember
that the delay designated in step 6 must elapse before
the fan will begin to operate.
8. With the outside air dampers fully closed and the
supply fan operating at 100% airflow requirements,
measure the return static pressure at the location
determined in step 1.
9. Press the STOP key at the Human Interface Module in
the unit control panel to stop the fan operation.
10. Open the field supplied main power disconnect switch
upstream of the rooftop unit. Lock the disconnect
switch in the “Open” position while working on the
dampers.
11. Locate the static pressure reading in
Table 44, p. 148
and determine which damper needs to be adjusted and
the degree reading. Proceed to the appropriate damper
actuator procedure.
To Adjust the Outside Air Damper Actuators:
12. Remove the shaft coupling from the damper shaft by
loosening the bolt and removing the retainer clip. Be
careful not to rotate the shaft.
13. Position the shaft coupling so that the indicator points
to the degree value obtained from step 11. The shaft
coupling is adjustable in 5 degree increments.
14. Replace the retainer clip and tighten the shaft coupling
on the shaft (120-180 in-lbs).
15. Close the disconnect switch or circuit protector switch
that provides the supply power to the unit terminal
block or the unit mounted disconnect switch.
16. Rotate the actuator control signal dial to Auto-Adapt.
The actuator will drive open and then closed to
determine the new open and closed positions.
17. Return the actuator control signal dial to 2-10 VDC
Modulating input signal position.
18. Plug the holes drilled in the cabinet after the proper
airfow has been established.
To Adjust the Return Damper Actuators:
19. Support or secure the damper blades in the wide open
position.
Note:
Gravity will cause the damper to close. Support or
secure the damper blades while removing the
actuator to prevent unexpected damper rotation.
20. Do not remove the shaft coupling from the shaft.
Remove the retainer clip from the shaft coupling.
21. Unscrew the actuator bracket from the damper wall.
22. Slide the actuator down the damper shaft off of the
shaft coupling.
23. Rotate the actuator and reinstall the shaft coupling in
the actuator so that the indicator points to the degree
value obtained in Step 11. The shaft coupling is
adjustable in 5 degree increments.
24. Replace the retainer clip and remove the blade stops to
allow the blades to rotate.
25. Rotate the actuator to the original position and reattach
the actuator bracket to the damper wall.
26. Close the disconnect switch or circuit protector switch
that provides the supply power to the unit terminal
block or the unit mounted disconnect switch.
27. Rotate the actuator control signal dial to Auto-Adapt.
The actuator will drive open and then closed to
determine the new open and closed positions.
28. Return the actuator control signal dial to the factory set
input signal position.
29. Plug the holes drilled in the cabinet after the proper
airfow has been established.
WARNING
Rotating Components!
During installation, testing, servicing and
troubleshooting of this product it may be necessary to
work with live and exposed rotating components. Have
a qualified or licensed service individual who has been
properly trained in handling exposed rotating
components, perform these tasks. Failure to follow all
safety precautions could result in rotating components
cutting and slashing technician which could result in
death or serious injury.
Содержание SEHJ090-162
Страница 40: ...Dimensional Data 40 RT SVX24J EN Figure 13 Evaporative condenser water connection locations RIGHT SIDE VIEW ...
Страница 48: ...Installation 48 RT SVX24J EN Figure 18 Ductwork conversion ...
Страница 58: ...Installation 58 RT SVX24J EN Figure 36 5 Connected tubes 6 install panels Connected tubes 5 6 ...
Страница 75: ...Installation RT SVX24J EN 75 Figure 51 Hot water coil piping Figure 52 Steam coil piping ...
Страница 87: ...Installation RT SVX24J EN 87 Figure 57 Typical field wiring diagram for 90 to 162 ton CV control options ...
Страница 89: ...Installation RT SVX24J EN 89 Figure 59 Typical field wiring diagram for 90 to 162 ton VAV control options ...