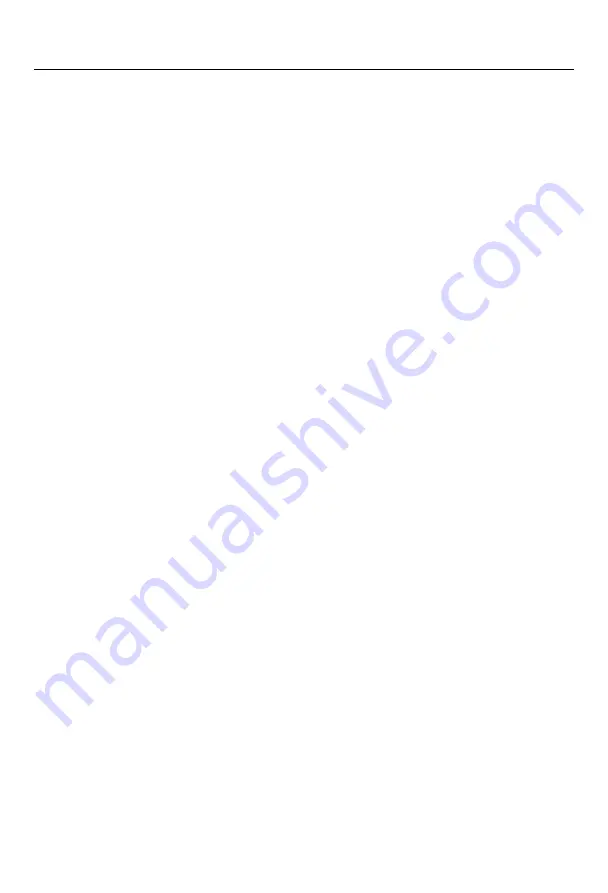
User Manual of EM730/EM730E Series Inverter
308
interference and RF interference will be generate to the control device. The following measures
can be taken.
Reduce the carrier frequency (F00.23) of the inverter.
Install a noise filter on the input side of the inverter.
Install a noise filter on the output side of the inverter.
Install a metal tube outside the cables. Install the inverter in a metal casing.
Make the inverter and motor grounded reliably.
Connect the main circuit and control circuit separately. Use the shielded cables in
the control circuit, and connect them according to the wiring method in Chapter 3.
9.2.6
Action of leakage circuit breaker
When the inverter is running, the leakage circuit breaker works.
Since the inverter outputs high-frequency PWM signals, a high-frequency leakage current
will be generated. Please use the dedicated leakage circuit breaker with the current sensitivity
above 30 mA. If an ordinary leakage circuit breaker is used, use a leakage circuit breaker with
the current sensitivity above 200 mA and action time of more than 0.1 s.
9.2.7
mechanical vibration
The inherent frequency of the mechanical system resonates with the carrier frequency of
the inverter.
The motor is not faulty, but the mechanical system produces sharp resonant sounds. This is
caused by the resonation between the inherent frequency of the mechanical system and carrier
frequency of the inverter. Please adjust the carrier frequency (F00.23) to avoid resonation.
The inherent frequency of the mechanical system resonates with the output frequency of
the inverter.
Resonation between the inherent frequency of the mechanical system and output frequency
of the inverter will lead to mechanical noise. Please use the vibration suppression function
(F05.13), or install the anti-vibration rubber or take other anti-vibration measures on the motor
base.
PID control oscillation
The adjustment parameters P, Ti and Td of the PID controller are not set correctly. Please
set the PID parameters again.