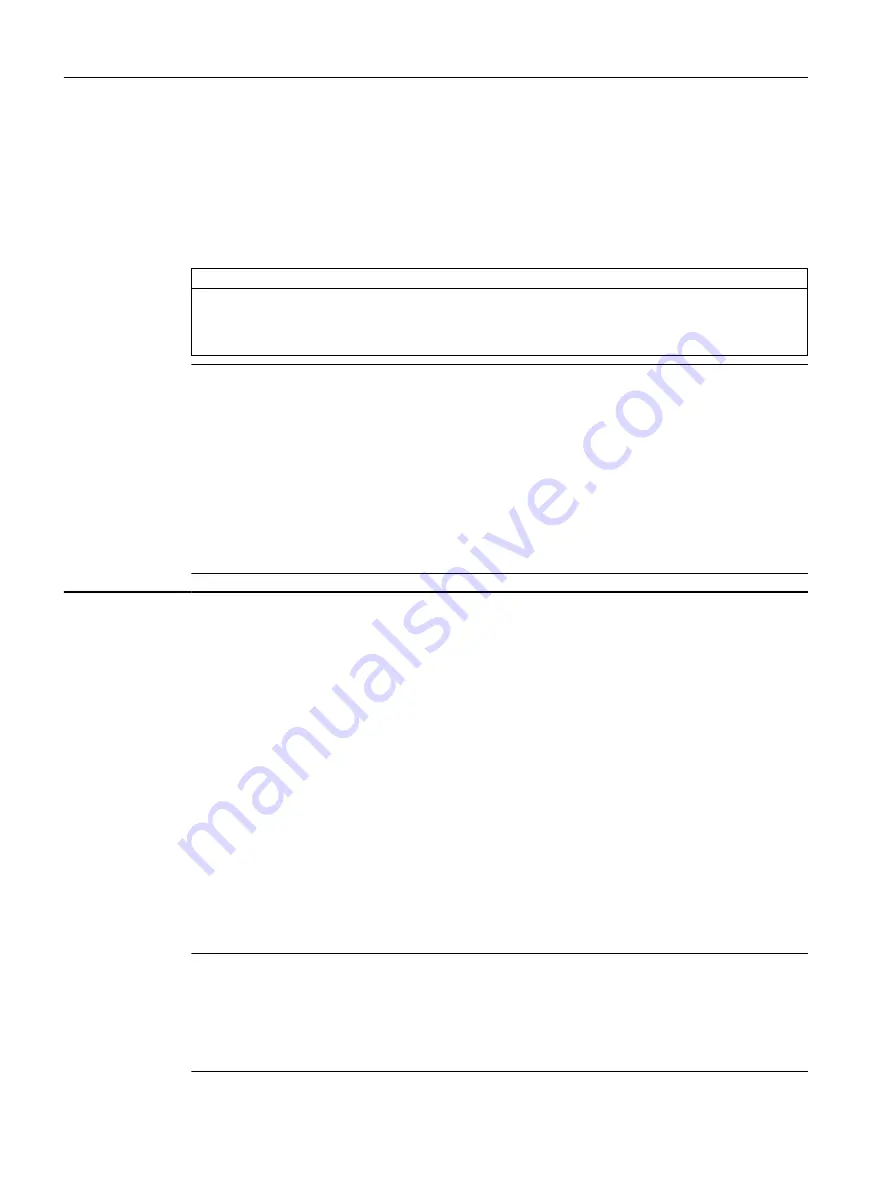
1:
Identifying motor data and optimizing the speed controller
2:
Identifying motor data (at standstill)
3:
Optimizing the speed controller (in rotating operation)
11:
Motor data ident. and speed controller opt., switch to operation
12:
Motor data identification (at standstill), switch to operation
Dependency:
See also: p1300, p1910, p1960
See also: A07980, A07981, F07983, F07984, F07985, F07986, F07988, F07990, A07991
NOTICE
p1900 = 3:
This setting should only be selected if the motor data identification was already carried out at standstill.
To permanently accept the determined settings they must be saved in a non-volatile fashion (p0971).
During the rotating measurement it is not possible to save the parameter (p0971).
Note
The motor and control parameters of the vector control are only optimally set when both measurements are carried out
(initially at standstill, and then with the motor rotating). The measurement with rotating motor is not performed for p1300
< 20 (U/f controls).
An appropriate alarm is output when the parameter is set.
The switch-on command must remain set during a measurement and after the measurement has been completed, the
drive automatically resets it.
The duration of the measurements can lie between 0.3 s and several minutes. This time is, for example, influenced by
the motor size and the mechanical conditions.
p1900 is automatically set to 0 after the motor data identification routine has been completed.
If a reluctance motor has been parameterized, a pole position identification is carried out during the stationary
measurement. As a consequence, faults that occur can also be assigned to the pole position identification.
For U/f control (p1300), identification with speed controller optimization does not make sense (e.g. P1900 = 1).
p1901
Test pulse evaluation configuration / Test puls config
Access level: 3
Calculated: CALC_MOD_ALL Data type: Unsigned32
Can be changed: T
Scaling: -
Dynamic index: -
Unit group: -
Unit selection: -
Function diagram: -
Min:
-
Max:
-
Factory setting:
0000 bin
Description:
Sets the configuration for the test pulse evaluation.
Bit 00: Check for conductor-to-conductor short circuit once/always when the pulses are enabled.
Bit 01: Check for ground fault once/always when the pulses are enabled.
Bit 02: Activation of the tests selected using bit 00 and/or bit 01 each time the pulses are enabled
Recommendation:
If the ground fault test is incorrectly initiated because the motor is not at a complete standstill, then the pulse
cancellation delay time (p1228) should be increased.
Bit field:
Bit
Signal name
1 signal
0 signal
FP
00
Phase short-circuit test pulse active
Yes
No
-
01
Ground fault detection test pulse active
Yes
No
-
02
Test pulse at each pulse enable
Yes
No
-
Dependency:
The ground fault test is only possible when the motor is stationary, and is therefore only realized when flying restart
is deactivated (p1200 = 0).
See also: p0287
Note
If a conductor-to-conductor short-circuit is detected during the test, this is displayed in r1902.1.
If a ground fault is detected during the test, this is displayed in r1902.2.
For bit 02 = 0:
If the test was successful once after POWER ON (see r1902.0), then it is not repeated.
For bit 02 = 1:
The test is not only performed after POWER ON, but also each time the pulses are enabled.
Parameters
7.3 Parameters
SINAMICS G120XA converter
542
Operating Instructions, 03/2019, FW V1.0, A5E44751205B AB
Содержание SINAMICS G120XA
Страница 2: ......
Страница 12: ...Table of contents SINAMICS G120XA converter 10 Operating Instructions 03 2019 FW V1 0 A5E44751205B AB ...
Страница 104: ...Wiring 4 2 Control interfaces SINAMICS G120XA converter 102 Operating Instructions 03 2019 FW V1 0 A5E44751205B AB ...
Страница 916: ...Index SINAMICS G120XA converter 914 Operating Instructions 03 2019 FW V1 0 A5E44751205B AB ...
Страница 917: ......