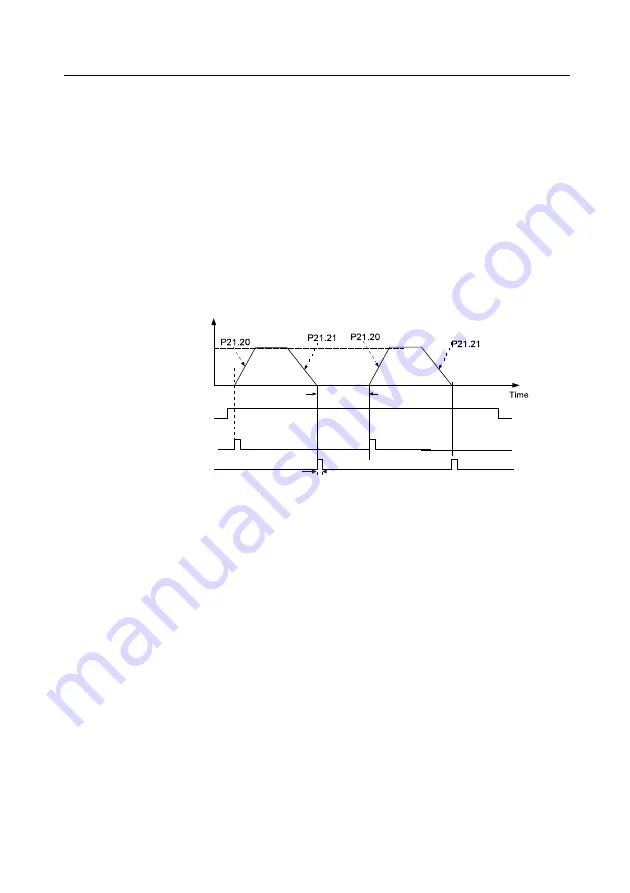
HD2 IP55 High-ingress Protection Series Inverter
-108
At this point, the belt may slip during high-speed running and cause inaccurate positioning, it is
recommended to install proximity switch on the spindle.
c) The encoder is installed on the spindle, and the motor shaft is connected to the spindle with
belt, the drive ratio is not necessarily 1:1;
At this point, set P20.06 (speed ratio of the mounting shaft between motor and encoder), and
set P22.14 (spindle drive ratio) to 1. As the encoder is not installed on the motor, the control
performance of closed-loop vector will be affected.
Proximity switch positioning supports the following spindle positioning modes:
a) The encoder is installed on the motor shaft, the drive ratio between motor shaft and spindle
is not necessarily 1:1;
At this point, it is required to set P22.14 (spindle drive ratio).
5. Commissioning procedures for digital positioning
The diagram for digital positioning is shown below.
Frequency
Positioning
speed
Running command
Cyclic positioning
enable signal terminal
Positioning completion signal
P21.25 Hold time of positioning completion signal
Step 1–4: These four steps are the same with the first four steps of the commissioning
procedures for closed-loop vector control, which aim to fulfill the control requirements of closed-
loop vector control.
Step 5: Set P21.00=0011 to enable digital positioning. Set P21.17, P21.11 and P21.12 (set
positioning displacement) according to actual needs ; set P21.18 and P21.19 (set positioning
speed); set P21.20 and P21.21 (set acceleration/deceleration time of positioning).
Step 6: Single positioning operation
Set P21.16.bit1=0, and the motor will carry out single positioning action and stay in the
positioning position according to the setup in step 5.
Step 7: Cyclic positioning operation
Set P21.16.bit1=1 to enable cyclic positioning. The cyclic positioning is divided into continuous
mode and repetitive mode; users can also carry out cyclic positioning through terminal function
(no. 55, enable digital positioning cycle)
6. Commissioning procedures for positioning of photoelectric switch
Photoelectric switch positioning is to realize positioning function based on closed-loop vector
control.
P21.22 Hold time
of positioning arrival
Basic Operation Instructions
Содержание HD2 IP Series
Страница 1: ......
Страница 16: ......
Страница 40: ......
Страница 107: ......
Страница 176: ...HD2 IP55 High ingress Protection Series Inverter 162 Function parameter list...
Страница 213: ......
Страница 271: ...HD2 IP55 High ingress Protection Series Troubleshooting 251 7 6 8 Overcurrent...
Страница 294: ...HD2 IP55 High ingress Protection Series Inverter 274...
Страница 360: ...HD2 IP55 High ingress Protection Series Inverter 340...
Страница 361: ......