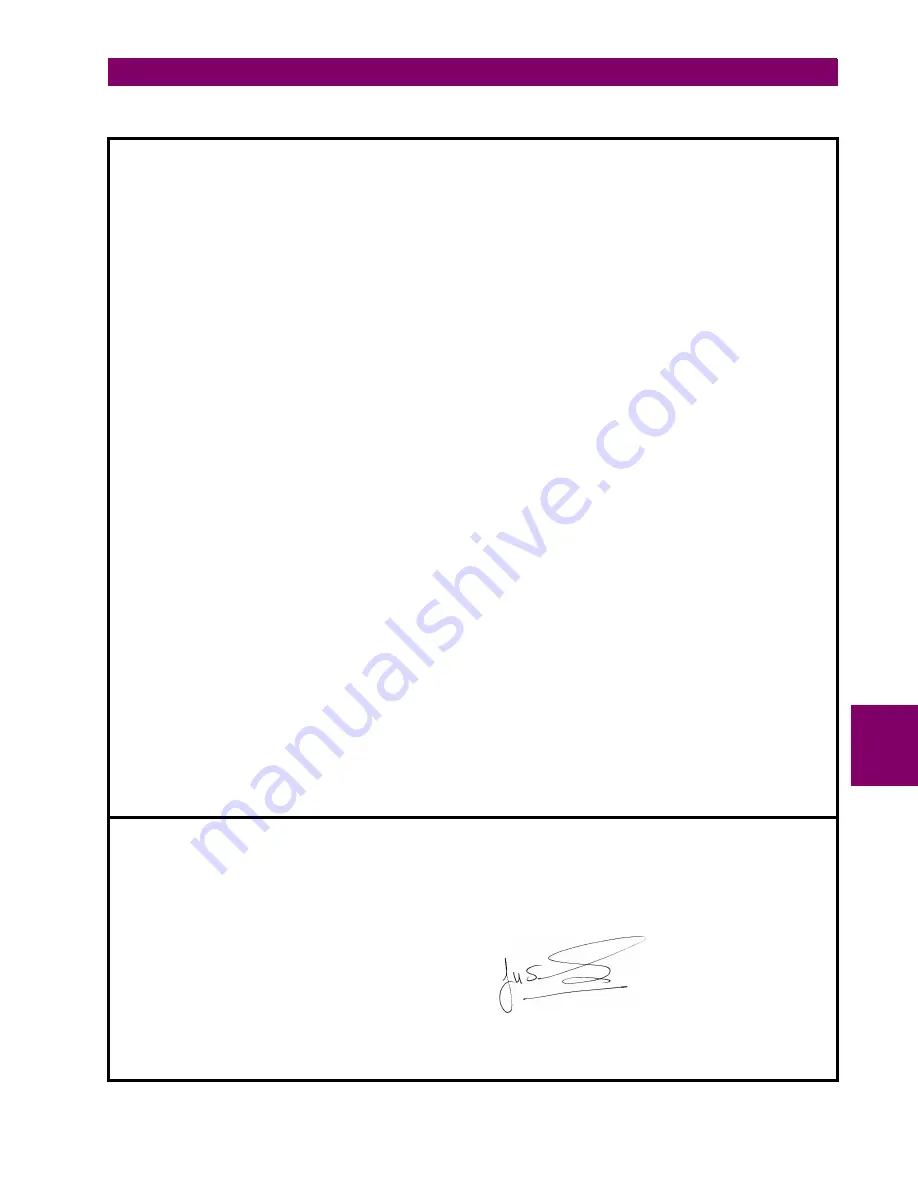
GE Power Management
MM2 Motor Manager 2
G-1
APPENDIX G
G.1 EU DECLARATION OF CONFORMITY
G
APPENDIX G MISCELLANEOUSG.1 EU DECLARATION OF CONFORMITY
EU DECLARATION OF CONFORMITY
Applicable Council Directives:
73/23/EEC
The Low Voltage Directive
89/336/EEC
The EMC Directive
Standard(s) to Which Conformity is Declared:
IEC 947-1
Low Voltage Switchgear and Controlgear
IEC1010-1:1990+ A 1:1992+ A 2:1995
Safety Requirements for Electrical Equipment for Measurement,
Control, and Laboratory Use
CISPR 11 / EN 55011:1997
Class A – Industrial, Scientific, and Medical Equipment
EN 50082-2:1997
Electromagnetic Compatibility Requirements, Part 2: Industrial
Environment
IEC100-4-3 / EN 61000-4-3
Immunity to Radiated RF
EN 61000-4-6
Immunity to Conducted RF
Manufacturer’s Name:
General Electric Power Management Inc.
Manufacturer’s Address:
215 Anderson Ave.
Markham, Ontario, Canada
L6E 1B3
Manufacturer’s Representative in the EU:
Christina Bataller Mauleon
GE Power Management
Avenida Pinoa 10
48710 Zamudio, Spain
Tel.: 34-94-4858835
Fax: 34-94-4858838
Type of Equipment:
Protection & Control Relay
Model Number:
MM2
First Year of Manufacture:
1999
I the undersigned, hereby declare that the equipment specified above conforms to the above
Directives and Standards
Full Name:
John Saunders
Position:
Manufacturing Manager
Signature:
Place:
GE Power Management Inc.
Date:
09/28/1999
Содержание MOTOR MANAGER 2
Страница 2: ......
Страница 4: ......
Страница 21: ...GE Power Management MM2 Motor Manager 2 2 3 2 INSTALLATION 2 1 MOUNTING 2 Figure 2 4 TYPICAL WIRING DIAGRAM ...
Страница 33: ...GE Power Management MM2 Motor Manager 2 3 7 3 HARDWARE 3 3 THEORY OF OPERATION 3 Figure 3 2 BLOCK DIAGRAM ...
Страница 34: ...3 8 MM2 Motor Manager 2 GE Power Management 3 3 THEORY OF OPERATION 3 HARDWARE 3 ...
Страница 80: ...5 12 MM2 Motor Manager 2 GE Power Management 5 5 A4 STATISTICS 5 ACTUAL VALUES 5 ...
Страница 130: ...7 2 MM2 Motor Manager 2 GE Power Management 7 1 INJECTION TESTING 7 TESTING 7 Figure 7 1 SECONDARY INJECTION TEST SETUP ...
Страница 153: ...GE Power Management MM2 Motor Manager 2 9 5 9 STARTER TYPES 9 2 FV REVERSING STARTER 9 Figure 9 4 FV REVERSING STARTER ...
Страница 161: ...GE Power Management MM2 Motor Manager 2 9 13 9 STARTER TYPES 9 4 SLIP RING STARTER 9 Figure 9 10 SLIP RING STARTER ...
Страница 187: ...GE Power Management MM2 Motor Manager 2 9 39 9 STARTER TYPES 9 13 SOFT STARTER 9 Figure 9 25 SOFT STARTER ...
Страница 188: ...9 40 MM2 Motor Manager 2 GE Power Management 9 13 SOFT STARTER 9 STARTER TYPES 9 ...
Страница 212: ...E 4 MM2 Motor Manager 2 GE Power Management E 1 CT ISOLATION APPENDIXE E ...
Страница 220: ...iv MM2 Motor Manager 2 GE Power Management INDEX ...