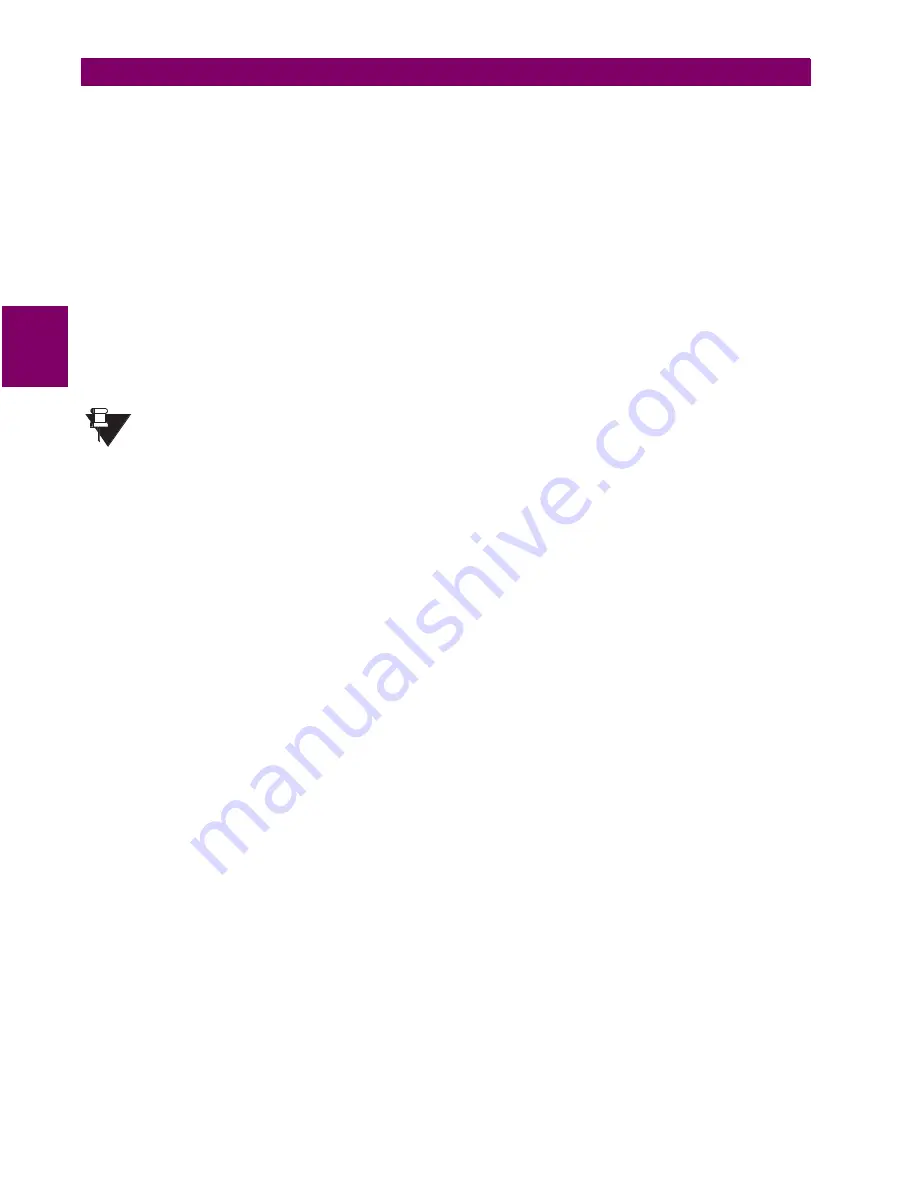
C-2
MM2 Motor Manager 2
GE Power Management
C.1 DO’S AND DONT’S
APPENDIX C
C
•
The shields of the cable should be daisy chained to all of the MM2 serial commons (Terminal 38)
and grounded at the MASTER only. This provides a common reference for all of the devices on
the data link, as well as, grounding the data link without creating the potential for ground loops.
The potential difference between the MM2 safety ground (terminal 14) and the MM2 serial com-
mon (Terminal 38) should not exceed 36 V.
•
A terminating network consisting of a 120
Ω
/ 0.25 W resistor in series with a 1 nF / 50 V general
purpose mono ceramic or equivalent capacitor MUST be placed across the positive and negative
terminals at both ends of the data link (terminals 39 and 40 on the MM2). This is to provide the
200 mV separation between the +ve and –ve terminals of the device, as well as to eliminate any
reflected signals and ringing.
d) SWITCH INPUTS
The MM2 has 16 switch inputs that operate on 120 V AC when the control voltage switch is set to
120 V AC and 240 V AC when the control voltage switch is set 240 V AC.
It is recommended that the switch terminals are activated from the same source as is
connected to Terminals 23 and 24. The common of the switch inputs is though Termi-
nal 23.
An external source can be used to supply the circuitry into the MM2 switch inputs providing that the
external source is
in phase with the control voltage of the MM2. The MM2 switches the inputs on and
off internally, to minimize power consumption, at a frequency determined by the control voltage. If the
external source is not in phase with the control voltage to the MM2, the timing will be off which could
cause errors when reading the switch inputs. If an external source is used to supply the control sig-
nals to the MM2 switch inputs, the source should be fused to protect against fault conditions in the
circuitry.
e) THERMISTOR AND ANALOG INPUTS
Due to the small voltage levels coming into the MM2 from the thermistor and external analog device,
shielded cable is recommended to minimize any noise that may be picked up. These wires should be
routed away from any power carrying cables.
f) STOP SWITCH INPUT
The STOP switch input on the MM2 MUST be energized before the MM2 is available to perform a
start. If the contactor is being energized and de-energized externally to the MM2, this terminal will
need a jumper from terminal 24 before the MM2 will seal in Contactor A.
g) CONTACTOR STATUS FEEDBACK
The MM2 MUST see feedback from Contactor A and Contactor B auxiliary contacts into the applica-
ble status switch inputs (Terminals 15 and 16) within 1 second of closing the contactor. If this feed-
back is not received, the MM2 will open the contactor instead of sealing it in, and will alarm with an
OPEN CONTROL CIRCUIT.
NOTE
Содержание MOTOR MANAGER 2
Страница 2: ......
Страница 4: ......
Страница 21: ...GE Power Management MM2 Motor Manager 2 2 3 2 INSTALLATION 2 1 MOUNTING 2 Figure 2 4 TYPICAL WIRING DIAGRAM ...
Страница 33: ...GE Power Management MM2 Motor Manager 2 3 7 3 HARDWARE 3 3 THEORY OF OPERATION 3 Figure 3 2 BLOCK DIAGRAM ...
Страница 34: ...3 8 MM2 Motor Manager 2 GE Power Management 3 3 THEORY OF OPERATION 3 HARDWARE 3 ...
Страница 80: ...5 12 MM2 Motor Manager 2 GE Power Management 5 5 A4 STATISTICS 5 ACTUAL VALUES 5 ...
Страница 130: ...7 2 MM2 Motor Manager 2 GE Power Management 7 1 INJECTION TESTING 7 TESTING 7 Figure 7 1 SECONDARY INJECTION TEST SETUP ...
Страница 153: ...GE Power Management MM2 Motor Manager 2 9 5 9 STARTER TYPES 9 2 FV REVERSING STARTER 9 Figure 9 4 FV REVERSING STARTER ...
Страница 161: ...GE Power Management MM2 Motor Manager 2 9 13 9 STARTER TYPES 9 4 SLIP RING STARTER 9 Figure 9 10 SLIP RING STARTER ...
Страница 187: ...GE Power Management MM2 Motor Manager 2 9 39 9 STARTER TYPES 9 13 SOFT STARTER 9 Figure 9 25 SOFT STARTER ...
Страница 188: ...9 40 MM2 Motor Manager 2 GE Power Management 9 13 SOFT STARTER 9 STARTER TYPES 9 ...
Страница 212: ...E 4 MM2 Motor Manager 2 GE Power Management E 1 CT ISOLATION APPENDIXE E ...
Страница 220: ...iv MM2 Motor Manager 2 GE Power Management INDEX ...