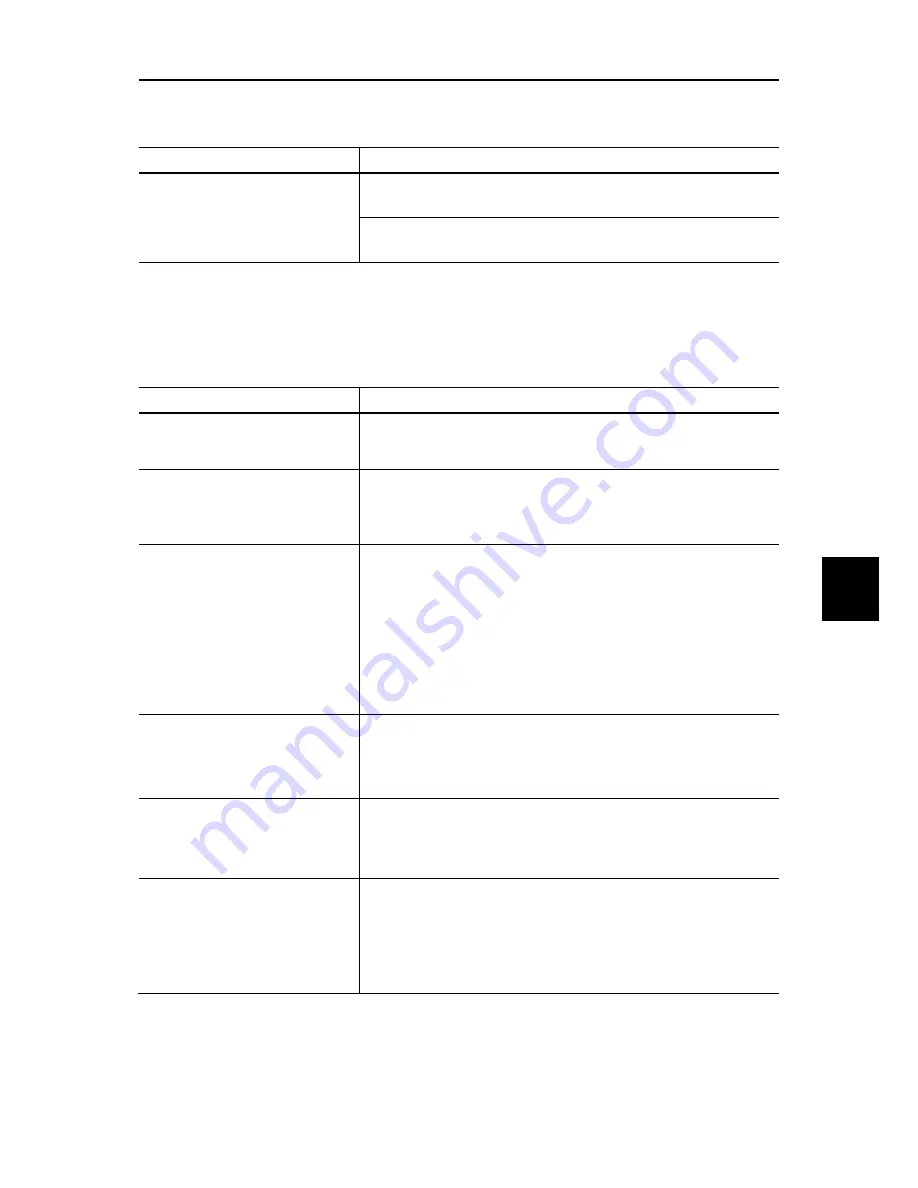
6.3 If an Alarm Code Appears on the LED Monitor
6-21
TR
O
U
BL
ES
H
O
O
TI
N
G
Chap 6
[ 34 ]
0s
Overspeed protection
Phenomena Motor rotated at excessive speed (When motor speed
≥
(F03×1.2)).
Possible Causes
Check and Measures
(1) Incorrect setting of function
code data.
Check the motor parameter “Number of poles” setting (P01*).
Specify the P01* data in accordance with the motor to be used.
Check the maximum frequency setting (F03*).
Specify the F03* data in accordance with the output frequency.
[ 35 ]
0un
Overvoltage
Phenomena The DC intermediate circuit voltage was over the detection level of overvoltage.
0u1
Overvoltage occurred during acceleration.
0u2
Overvoltage occurred during deceleration.
0u3
Overvoltage occurred during running at constant speed.
Possible Causes
Check and Measures
(1) The power supply voltage
exceeded the inverter's mode
range.
Measure the input voltage.
Decrease the voltage to within the specified range.
(2) A surge current entered the
input power supply.
In the same power line, if a phase-advancing capacitor is turned
ON/OFF or a thyristor converter is activated, a surge (momentary large
increase in the voltage or current) may be caused in the input power.
Install a DC reactor.
(3) The deceleration time was too
short for the moment of inertia
of the load.
Recalculate the deceleration torque based on the moment of inertia of
the load and the deceleration time.
Increase the deceleration time (F08, E11, E13, E15, and H56).
Enable the anti-regenerative control (H69), or deceleration
characteristics (H71).
Set torque limit (F40, F41, E16, E17) to become effective.
Set the rated voltage at base frequency (F05*) to “0” to improve the
braking capability.
Consider the use of a braking resistor.
(4) The acceleration time was too
short.
Check if the overvoltage alarm occurs after rapid acceleration.
Increase the acceleration time (F07, E10, E12, and E14).
Select the Curve acceleration/ deceleration (H07).
Consider the use of a braking resistor.
(5) Braking load is too heavy.
Compare the braking torque of the load with that of the inverter.
Set the rated voltage at base frequency (F05*) to “0” to improve the
braking capability.
Consider the use of a braking resistor.
(6) Malfunction caused by noise.
Check if the DC intermediate circuit voltage was below the protective
level when the overvoltage alarm occurred.
Implement noise control measures. For details, refer to Appendix A.
Enable the retry function (H04).
Connect a surge absorber to magnetic contactor's coils or other
solenoids (if any) causing noise.
Содержание FRENIC-Ace series
Страница 20: ......
Страница 32: ......
Страница 92: ......
Страница 94: ......
Страница 452: ......
Страница 490: ......
Страница 504: ......
Страница 506: ...8 2 Frequency Setting Section 8 2 8 2 Frequency Setting Section Figure 8 2 1 Frequency Setting Section Block Diagram...
Страница 508: ...8 2 Frequency Setting Section 8 4 Figure 8 2 3 Frequency Setting Section Block Diagram...
Страница 514: ...8 6 Control Section 8 10 3 With speed sensor Figure 8 6 3 V f Control with speed sensor Section Block Diagram...
Страница 520: ...8 6 Control Section 8 16 6 For PMSM Figure 8 6 9 Vector Control For PMSM Section Block Diagram...
Страница 522: ...8 7 FM Output Section 8 18 8 7 FM Output Section Figure 8 7 1 FM Output Section Block Diagram...
Страница 582: ......
Страница 646: ...11 9 Power Regenerative PWM Converters RHC Series 11 42 11 9 5 External dimensions PWM converter Boosting reactor...
Страница 649: ...11 9 Power Regenerative PWM Converters RHC Series 11 45 SELECTING PERIPHERAL EQUIPMENT Chap 11 Charging resistor Fuse...
Страница 664: ...11 15 External Cooling Fan Attachments 11 60...
Страница 690: ......
Страница 692: ......
Страница 720: ......
Страница 738: ......
Страница 787: ......