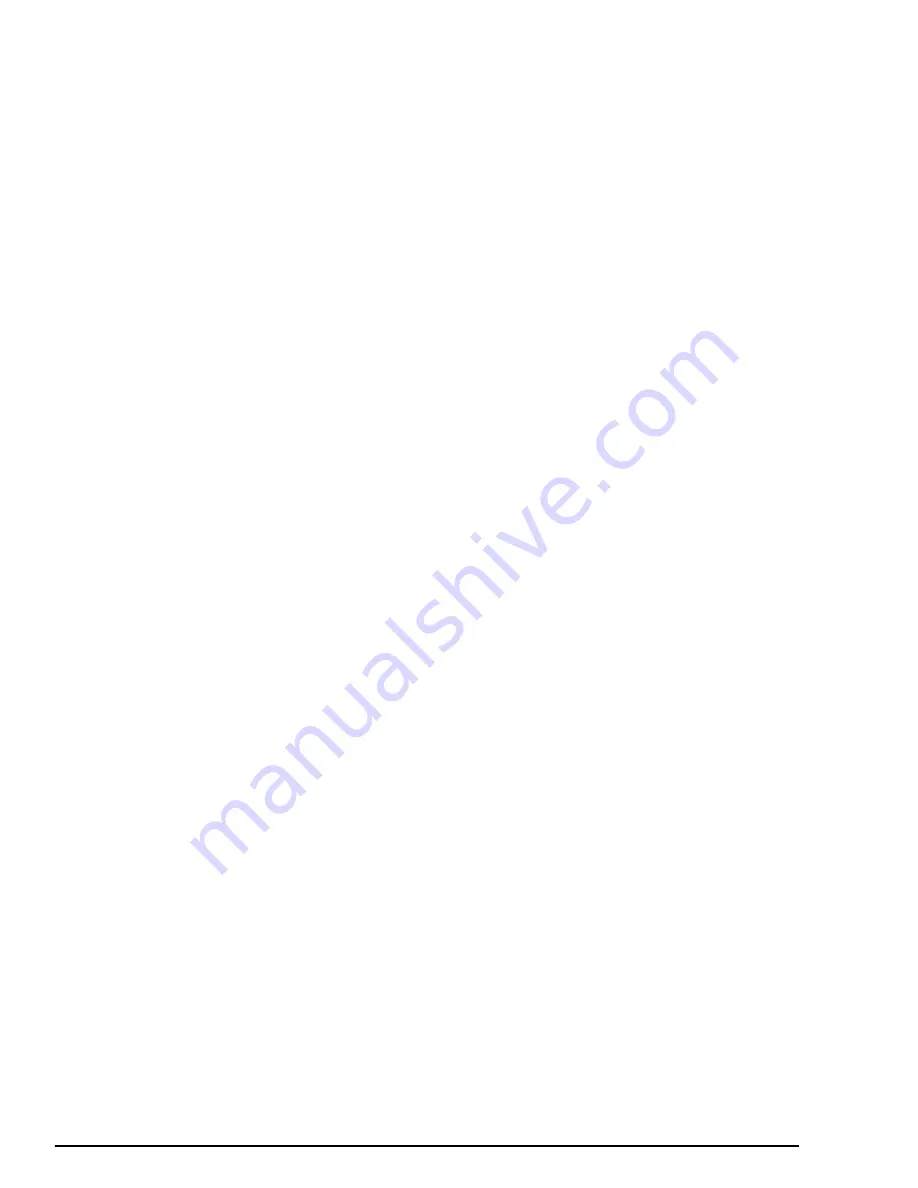
174
Commander SE Advanced User Guide
Issue Number: 4
12.14 Torque limiting
Example 1
When the Commander SE is in torque control and is told to stop by opening the run forward or run reverse terminals,
sometimes the motor will carry on turning at low frequency. This is due to inaccuracies in the current measurement circuitry
on the drive. This may be seen on unloaded or very lightly loaded motors, but can be overcome by using the following set-up.
Parameter set-up
1.22
= 30
Preset speed 2 to the maximum speed the drive will run at (will be
1.22
+20%)
1.23
= -750
Preset speed 3 to -750 to give an error between PID main reference and PID reference
4.11
= 1
Torque control selected
7.10
=
4.08
Analog input 1 destination to torque reference
9.04
=
8.03
Logic source 1 to terminal 10 monitor
9.05
= 1
Logic source 1invert
9.06
=
8.04
Logic source 2 to terminal 11 monitor
9.07
= 1
Logic source 2 invert
9.10
=
14.08
Logic source output to PID enable
14.02
=
1.22
Preset speed 2 to PID main reference source
14.03
=
1.23
Preset speed 3 to PID reference source
14.10
= 0
PID proportional gain to zero
14.11
= 0.1
PID integral gain to 0.1
14.13
= 30
PID high limit to 30
14.14
= -30
PID low limit to -30
14.15
= 0.1
PID scaling to 0.1
14.16
=
1.06
PID output to maximum speed
Perform a Save routine:
xx.00
= 1000 and press red Stop / Reset button on the drive.
Operation
When the Drive is enabled and told to run via either the run forward or run reverse terminals, the PID loop will be disabled so
that the Drive will run in torque control as normal. The maximum output frequency of the Drive is set by the value of preset
speed 1 +20%. When either the run forward or run reverse terminals are opened, the PID loop will be enabled, this will create
an error between the main PID reference source and the PID reference source. This error will cause the PID output and thus
the maximum speed clamp to ramp to zero frequency. This will then clamp the output frequency at zero Hz.
Example 2
The following set-up monitors the drive's output current and when this current goes above a set level for a set period of time,
stops the drive.
Parameter set-up
Set
6.04
= 3
Changes terminal 9, 10 & 11 set-up
Perform a Save routine:
xx.00
= 1000 and press red Stop / Reset button on the drive
Set
8.11
= 1
Terminal 8, digital output invert
Set
8.21
=
9.01
Digital output from programmable logic output indicator
Set
8.39
= 1
Terminal 12 & 13 automatic set-up disable
Set
8.25
=
6.15
Terminal 12 as Enable/Disable terminal
Set
9.04
=
12.01
Programmable logic source 1 from programmable threshold output indicator
Set
9.09
= ??
Programmable logic timer - set to required time
Set
12.03
=
4.01
Programmable
threshold
source from motor current magnitude
Set
12.04
= ??
Programmable threshold level - set to required level
Set
12.05
= 5
Programmable threshold hysteresis set to 5%
Perform a Save routine:
xx.00
= 1000 and press red Stop / Reset button on the drive.
Terminal Set-up
Terminal 9 = Not Stop (latching)
Terminal 10 = Run (latching)
Terminal 11 = Forward / Reverse
Terminal 12 = Enable
Connect terminal 8, digital output to terminal 9, Not Stop input. A normally closed push button switch could be put in series
with this connection to allow the drive to be stopped rather than disabled.
Содержание COMMANDER SE
Страница 76: ...76 Commander SE Advanced User Guide Issue Number 4...
Страница 93: ...Commander SE Advanced User Guide 93 Issue Number 4...
Страница 98: ...98 Commander SE Advanced User Guide Issue Number 4...
Страница 142: ...142 Commander SE Advanced User Guide Issue Number 4 Figure 6 9 Input line reactor 4400 0241 All dimensions in mm...
Страница 144: ...144 Commander SE Advanced User Guide Issue Number 4 Figure 7 3 Commander SE Size 4 All dimensions in mm...