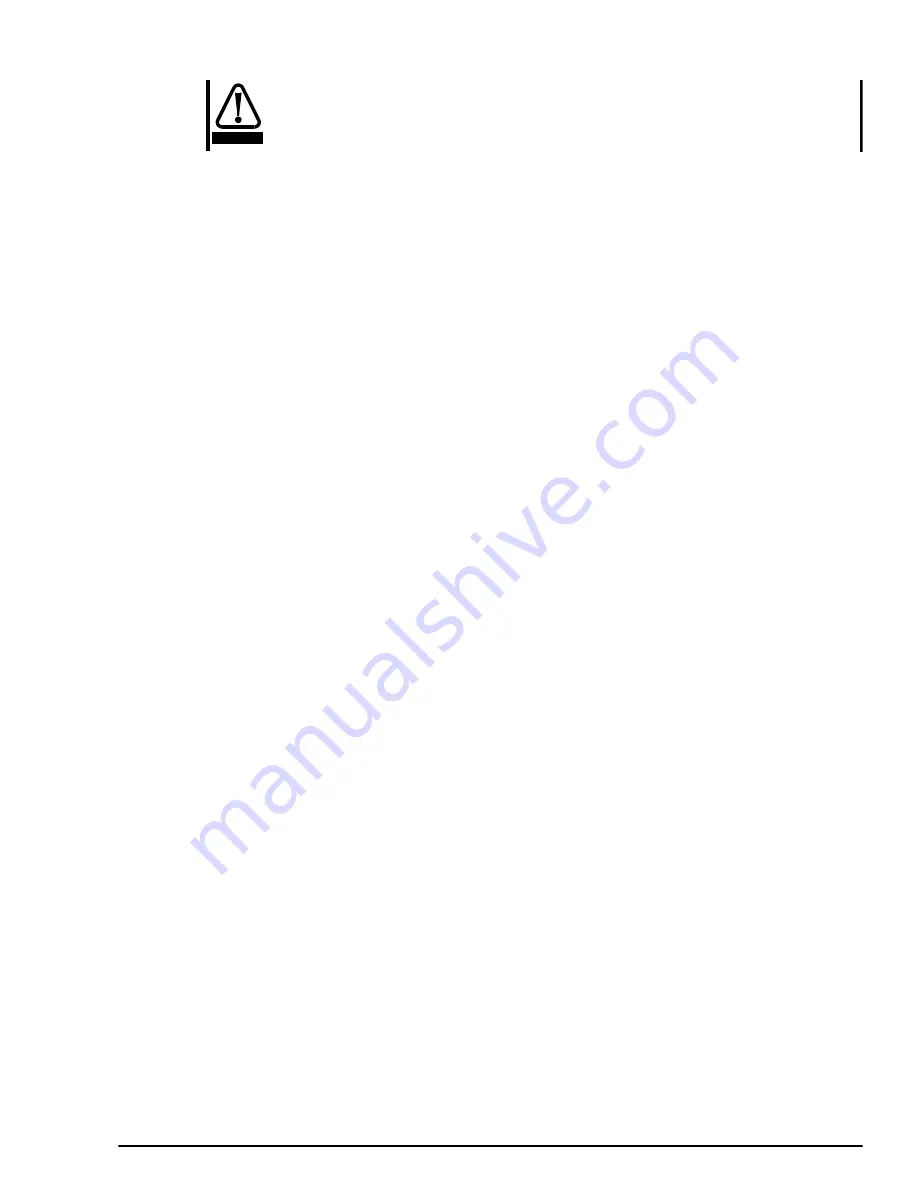
Commander SE Advanced User Guide
169
Issue Number: 4
12.10.2 Brake set-up 2
The following set-up is an alternative to the set-up on the previous page.
Great care should be taken when implementing a brake control set-up as this may cause a safety issue
depending on the application, e.g. crane. If in any doubt, please contact the supplier of the drive for
advice and information.
Frequency Reference
Usually by analog reference of preset speeds. The run forward and/or run reverse inputs must be used to change the
direction of motor rotation. Changing the direction of rotation by the sign of the analog input is not advisable for safety
reasons.
Brake Control
IMPORTANT INFORMATION!
•
Connect a +24V interface relay to the Commander SE according to the connection diagram on the following page.
•
Control the brake contactor according to the diagram on the following page.
•
The programming of the Drive Healthy relay should not be changed, it should remain as a Drive Healthy relay.
•
Make sure that the Drive Healthy relay of the Commander SE inhibits the brake contactor.
•
Use a separate overspeed detection which is integrated into the emergency stop circuit.
•
Use DC control of the brake coil to improve brake response.
•
Fast ramps must be selected to stop extended travel due to the drives internal DC bus controller becoming active and
increasing the ramp times automatically.
Commissioning and drive set-up
•
Connect the Commander SE according to the connection diagram on the following page.
•
Disconnect the coil connecting the brake contactor.
•
Program the following parameters:
02
= set the appropriate motor rated frequency
06
= set the appropriate motor rated current
07
= 0 disable slip compensation
08
= set the appropriate motor rated voltage
09
= set the appropriate motor rated power factor
30
= 0 (FASt) Set fast ramps
8.21
=
9.01
Digital output source
from
programmable logic output indicator
9.04
=
12.01
Programmable logic source 1
from
programmable threshold indicator
9.06
=
10.03
Programmable logic source 2
from
zero speed indicator
9.07
= 1
Programmable logic source 2 invert
12.03
=
4.01
Threshold detector source
from
motor current magnitude
•
Calculate and program parameter
3.05
-
Zero speed threshold
3.05
= ((
N
sync
-
N
rated
) /
N
sync
) x 50
Example
Motor rated speed of 1440 rpm
3.05
=((1500-1440) / 1500) x 50 = 2Hz
•
Calculate and program parameter 15 -
Jog reference
15 =
3.05
+ 0.5
Example
15 = 2 + 0.5 = 2.5Hz
•
Calculate and program parameter
12.04
-
Threshold detector level
12.04
= (I rated motor / I rated Commander SE) x 25
•
Program parameter
12.05
, T
hreshold detector hysteresis
, with the value of parameter
12.04
•
Program parameter
01
, minimum speed, with the value of parameter
15
•
If 2 preset speeds are used, the high speed will be selected by terminal 12 and the following parameters will need to be
programmed:
8.39
=1
Disable digital inputs 5 and 6 auto select
1.14
= 3
Reference selector
to select preset speeds
8.25
=
1.45
Terminal 12 destination to select preset select bit 0
11
Required low speed into preset speed 1
12
Required high speed into preset speed 2
•
Press the red stop/reset button on the drives keypad and reconnect the coil of the brake contactor
•
Perform an autotune by setting parameter
38
= 1.
•
Run the drive and tune/adjust the acceleration ramps in parameters
03
and
04
.
•
Perform a Save routine:
xx.00
= 1000 and press red Stop / Reset button on the drive
WARNING
Содержание COMMANDER SE
Страница 76: ...76 Commander SE Advanced User Guide Issue Number 4...
Страница 93: ...Commander SE Advanced User Guide 93 Issue Number 4...
Страница 98: ...98 Commander SE Advanced User Guide Issue Number 4...
Страница 142: ...142 Commander SE Advanced User Guide Issue Number 4 Figure 6 9 Input line reactor 4400 0241 All dimensions in mm...
Страница 144: ...144 Commander SE Advanced User Guide Issue Number 4 Figure 7 3 Commander SE Size 4 All dimensions in mm...