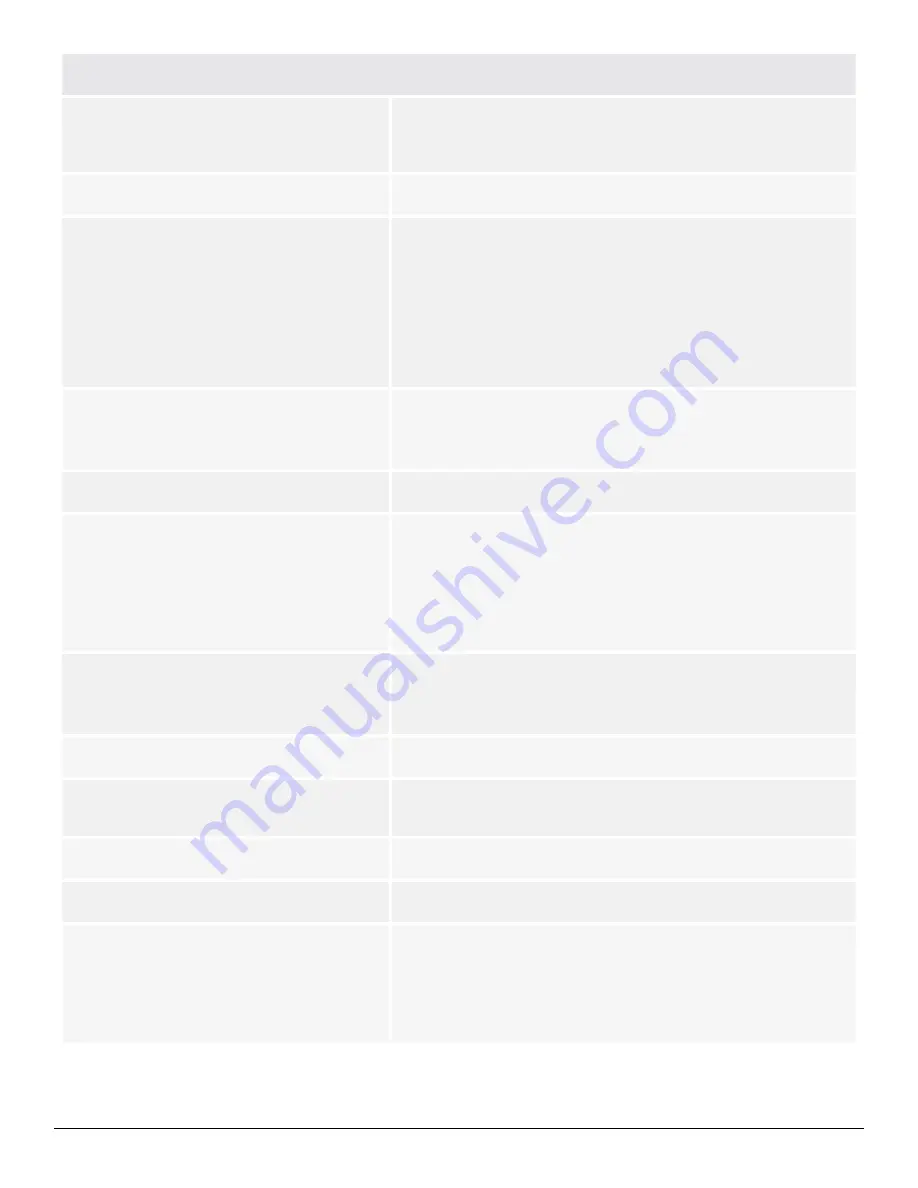
3D Systems, Inc.
106
p/n: 15-D100, rev. D
QUESTION
ANSWER
The clamp came off during transport and we
lost the cap, is there anything to worry about?
Not likely, there are spring loaded check valves that automatically seal
the tank when caps are removed. If any air got in, in the fraction of a
second for the valve to seal, it would be too low of a concentration to
initiate combustion.
Do we have to be ESD safe when handling the
cartridge?
No, once it is capped and clamps on, the cartridge is safe to transport
and no concern with static charge is necessary.
What happens if air gets inside a used tank? Is
just a little air dangerous or only if it’s a lot of
air?
In case of titanium, aluminum and iron fumes, air ingress in the
filter might cause ignition due to the pyrophoric nature of the waste.
However, the filter is equipped with self-sealing valves, which should
cause the fire, if any, to extinguish itself when it is starved of oxygen.
Because of the self-sealing valves, air ingress in the filter is limited.
Nonetheless upright storage with the proper blind flanges installed
is necessary to avoid incidents in case a filter falls or is otherwise
disturbed.
Always try to close the filter with the blind flanges as soon as you can.
I know titanium fumes ignited very fast in air,
what if I accidentally get some air inside and
close it quickly; did I just make a bomb?
Any ignition in the filter should be self-extinguishing as the air is
consumed and the self-sealing valves prevent ingress of further air.
In the case air get inside, still make sure to close the valves as soon as
possible to prevent further risks.
Do different materials produce more fume
particles than others?
Yes. In addition, the amount of generated fumes is also dependent on
the printer type, parameters used and the type of geometries printed.
How many hours can I expect to get out of a
canister before needing to change
Follow the guidance of the maintenance management tools. The
number of operation hours (job hours) of a filter is a stable measure to
assess how full the filter is on your system.
DMP Factory 350: 1800 job hours.
Upcoming software will also consider a measurement of the drop in
filter pressure as an additional measure of the filter lifetime. This will
be additionally available in the maintenance management tools.
What is a good indication that my filter needs
to be changed?
See 6.
If the maintenance manager guidelines are followed, no alleged effects
such as soot pulled out of the filter, slower airflow or increased dirt
depositions on the lens do not occur.
Do I have to change the suction hose to the
filter when I change materials?
No, the amount of condensate is minimal and negligible reaction if it
mixes with other material condensate.
Will the condensate particles in the suction
hose ignite if I have to change the suction
hose?
The quantity of fumes present in the vacuum hose does not pose
immediate danger.
I see a lot of raw powder along with
condensate in the suction hose.
Have the air knife adjusted as de-powdering is taking place. All
airborne material is sucked into the filter.
What if the humidity in my shop is really high,
will this moisture start a fire in the canister?
There is no concern as the filter valves will not open until the chamber
is inert and all atmospheric air has been evacuated.
What tests were performed during the UN
certification?
Tests for steel drums (1A1W) prescribed by:
UN- regulations – part 6
IMDG – part 6
ICAO – part 6
ADR – RID – part 6
Содержание DMP Flex 350
Страница 1: ...DMP Flex 350 Production printer User guide Original instructions ...
Страница 11: ...3D Systems Inc 6 p n 15 D100 rev D 1 x on the printer door 1 x on the scanner 2 1 4 Laser Safety Label ...
Страница 119: ...3D Systems Inc 114 p n 15 D100 rev D 8 BASIC REGULATIONS 8 1 EC Declaration of Conformity DoC ...