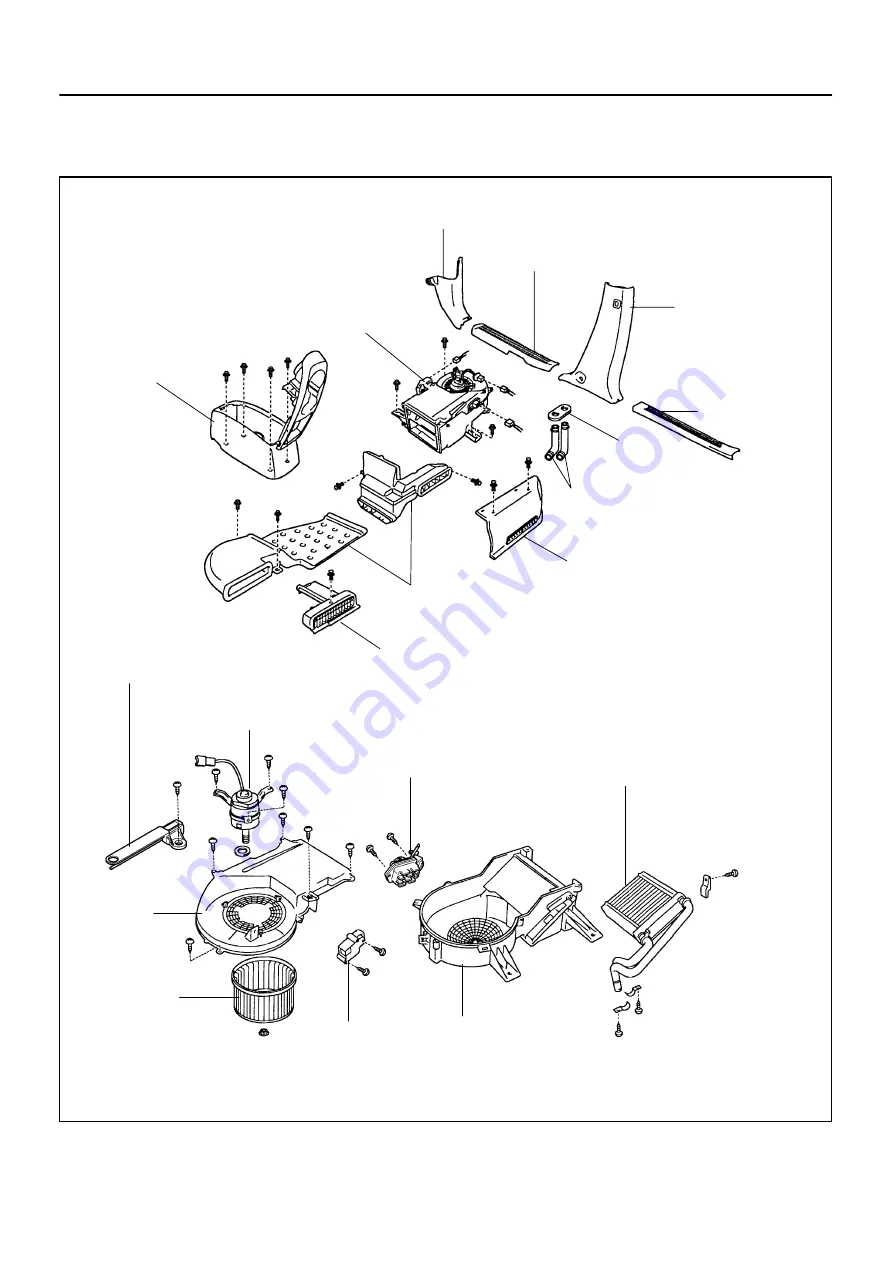
AC0SI-03
I20980
Air Outlet Grill
Rear Air Duct
Air Outlet Grill
Water Hose
Grommet
Rear Door
Lower Center Pillar
Front Door Scuff Plate
Cowl Side Trim
Rear Heater Unit
Rear Console Box
Garnish
Scuff Plate
Heater Case
Manual A/C:
Blower Resistor
Auto A/C:
Power Transistor
Heater Radiator
Blower Motor
Heater Case
Blower Fan
Air Mix Servomotor
Auto A/C:
Rear Heater Intake Air Temp. Sensor
-
AIR CONDITIONING
REAR HEATER UNIT
AC-47
1888
Author:
Date:
2001 SIENNA (RM787U)
REAR HEATER UNIT
COMPONENTS