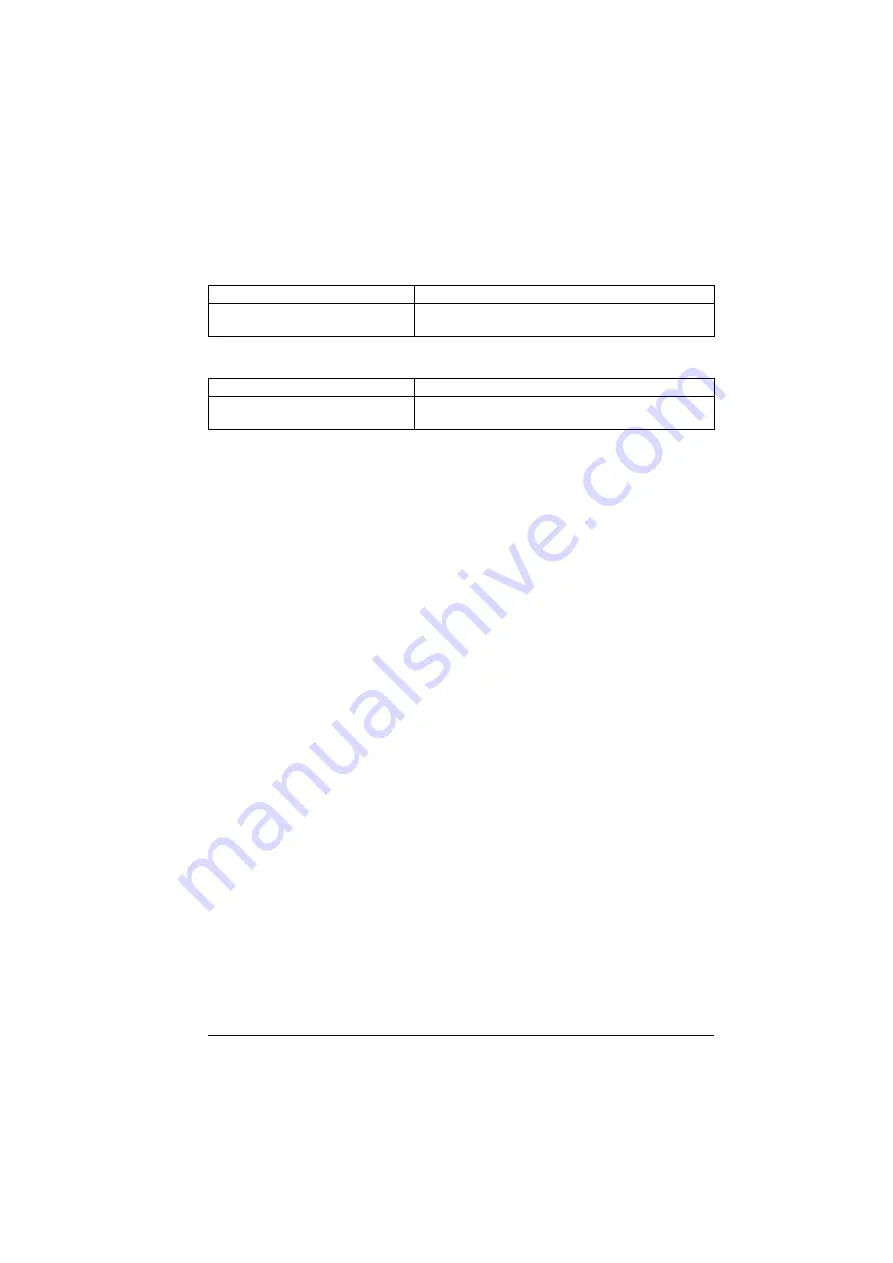
Program features 137
Settings
Diagnostics
PFA control
(Requires use of MREL-01 option purchased separately)
PFA control
The pump and fan alternation (PFA) control switches auxiliary pumps on and off as
required by capacity changes. The Autochange function alternates between pumps to
keep the duty times of the pumps equal. Interlocks function enables the drive to
detect if any of the pumps are unavailable (for example, switched off for
maintenance), in which case the next available pump is started instead.
The drive controls the motor of pump 1, varying the motor speed to control the pump
capacity. This motor is the speed regulated motor.
Direct line connections power the motor of pump 2 and pump 3, etc. The drive
switches pump 2 (and then pump 3, etc.) on and off as needed. These motors are
auxiliary motors.
The drive PID control uses two signals: a process reference and an actual value
feedback. The PID controller adjusts the speed (frequency) of the first pump such that
the actual value follows the process reference.
When demand (defined by the process reference) exceeds the first motor’s capacity
(user defined as a frequency limit), the PFA control automatically starts an auxiliary
pump. The PFA control also reduces the speed of the first pump to account for the
auxiliary pump’s addition to total output. Then, as before, the PID controller adjusts
the speed (frequency) of the first pump such that the actual value follows the process
reference. If demand continues to increase, the PFA control adds additional auxiliary
pumps, using the same process.
When demand drops, such that the first pump speed falls below a minimum limit
(user defined by a frequency limit), the PFA control automatically stops an auxiliary
pump. The PFA control also increases the speed of the first pump to account for the
auxiliary pump’s missing output.
An Interlock function (when enabled) identifies off-line (out of service) motors, and the
PFA control skips to the next available motor in the sequence.
Parameter
Additional information
,
Load analyzer settings
Actual signal
Additional information
,
Load analyzer results
Summary of Contents for ACS320 series
Page 1: ...ABB drives User s manual ACS320 drives 0 5 to 30 hp ...
Page 4: ......
Page 18: ...18 Safety ...
Page 28: ...28 Operation principle and hardware description ...
Page 56: ...56 Electrical installation ...
Page 142: ...142 Program features Connection diagram example ACS320 xx xxxx x ...
Page 282: ...282 Actual signals and parameters ...
Page 358: ...358 Fieldbus control ...
Page 376: ...376 Fault tracing ...
Page 382: ...382 Maintenance and hardware diagnostics ...
Page 407: ...Dimension drawings 407 Frame size R2 NEMA 1 Frame size R2 IP20 NEMA 1 3AUA0000051097 A ...
Page 409: ...Dimension drawings 409 Frame size R3 NEMA 1 Frame size R3 IP20 NEMA 1 3AUA0000051118 A ...
Page 411: ...Dimension drawings 411 Frame size R4 NEMA 1 Frame size R4 IP20 NEMA 1 3AUA0000051133 A ...
Page 412: ...412 Dimension drawings ...
Page 413: ...Index Numerics A B C D E F G H I K L M N O P R S T ...