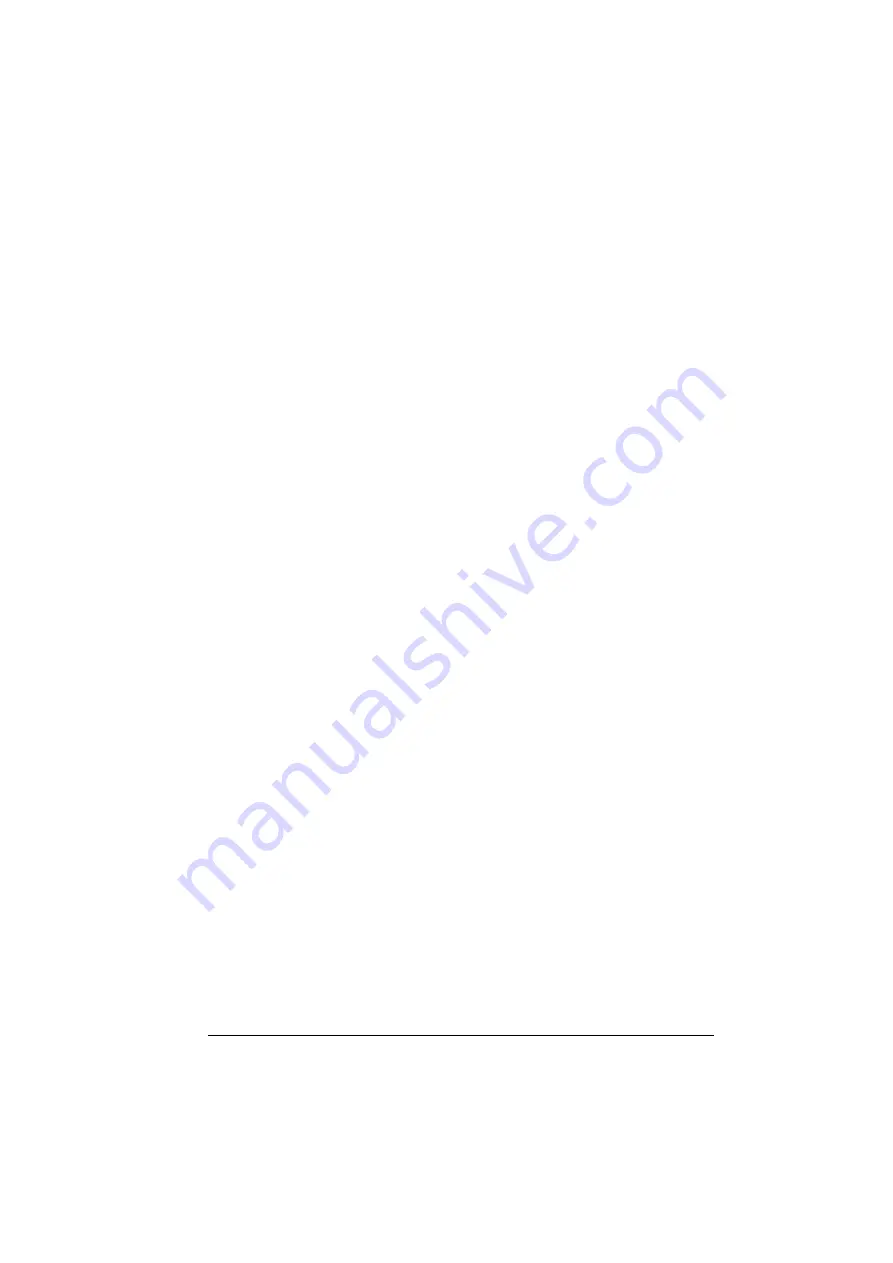
Program features 121
Parameter lock
The user can prevent parameter adjustment by activating the parameter lock.
Settings
Parameters
PID control
There are two built-in PID controllers in the drive:
• Process PID (PID1) and
• External/Trim PID (PID2).
The PID controller can be used when the motor speed needs to be controlled based
on process variables such as pressure, flow or temperature.
When the PID control is activated, a process reference (setpoint) is connected to the
drive instead of a speed reference. An actual value (process feedback) is also
brought back to the drive. The drive compares the reference and the actual values,
and automatically adjusts the drive speed in order to keep the measured process
quantity (actual value) at the desired level (reference).
The control operates on a 2 ms time level.
Process controller PID1
PID1 has two separate sets of parameters (
,
). Selection between parameter sets 1 and 2 is defined by a
parameter.
In most cases when there is only one transducer signal wired to the drive, only
parameter set 1 is needed. Two different parameter sets (1 and 2) are used, eg, when
the load of the motor changes considerably in time.
External/Trim controller PID2
PID2 (
) can be used in two different ways:
• External controller: Instead of using additional PID controller hardware, the user
can connect PID2 output via drive analog output or fieldbus controller to control
a field instrument like a damper or a valve.
• Trim controller: PID2 can be used to trim or fine tune the reference of the drive.
See section
.
Summary of Contents for ACS320 series
Page 1: ...ABB drives User s manual ACS320 drives 0 5 to 30 hp ...
Page 4: ......
Page 18: ...18 Safety ...
Page 28: ...28 Operation principle and hardware description ...
Page 56: ...56 Electrical installation ...
Page 142: ...142 Program features Connection diagram example ACS320 xx xxxx x ...
Page 282: ...282 Actual signals and parameters ...
Page 358: ...358 Fieldbus control ...
Page 376: ...376 Fault tracing ...
Page 382: ...382 Maintenance and hardware diagnostics ...
Page 407: ...Dimension drawings 407 Frame size R2 NEMA 1 Frame size R2 IP20 NEMA 1 3AUA0000051097 A ...
Page 409: ...Dimension drawings 409 Frame size R3 NEMA 1 Frame size R3 IP20 NEMA 1 3AUA0000051118 A ...
Page 411: ...Dimension drawings 411 Frame size R4 NEMA 1 Frame size R4 IP20 NEMA 1 3AUA0000051133 A ...
Page 412: ...412 Dimension drawings ...
Page 413: ...Index Numerics A B C D E F G H I K L M N O P R S T ...