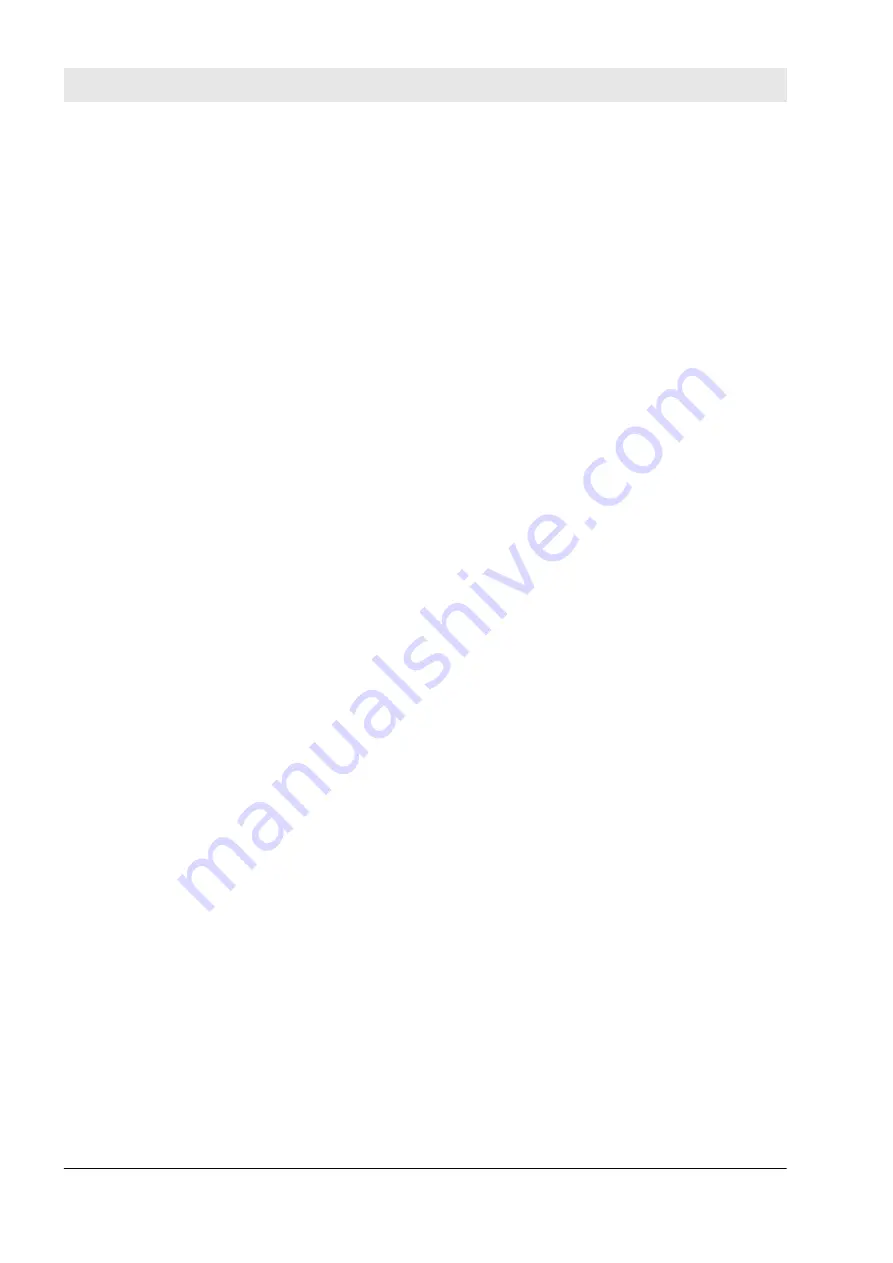
6
Second cartonning machine, guarded by an
electro-sensitive protective equipment, ESPE. In
this case, it is a light curtain.
7
Palletizing function, guarded by safety mats. This
functionality could be coupled to the ESPE safety
function.
8
Foil wrapping station of the palletized products,
as well as exit of the production line. This area is
safeguarded by several combined light beams,
coupled to the ESPE safety function.
In addition, every station is equipped with an emergency stop.
7.2 Example 1: Diagnostics concept
This example shows the usage of the diagnostic concept, with a daisy chain from the FB parameters Acti-
vate and Ready (with perhaps a pre-evaluation of hardware errors), and a coupling to an HMI screen with
error IDs and messages through the functional application. For clarity sake of the safety function, the other
Chapter 7.3 “Example 2: Muting” on page 430
and
Chapter 7.4 “Example 3: Two-hand con-
) will not show the diagnostic connections.
The safety functionality is to stop a drive in accordance with stop category 1 of IEC 60204-1 initiated by an
Emergency stop or by interrupting the light curtain. The equivalent monitoring of the 2 connectors of the
emergency switch is done in the safety application.
In this example, both options of input evaluation are shown:
n
via intelligent safety input
n
via the equivalent function block.
7.2.1 Functional description of safety functions
This example uses the following safety functions:
n
Issuing the emergency stop (via SF_EmergencyStop) or interrupting the light beam in the light curtain
(via SF_ESPE) stops the drive in accordance with stop category 1.
n
The stop of the electrical drive within a predefined time is monitored (via SF_SafeStop1).
n
The Safe Status of the drive is indicated by the S_Stopped variable, connected to the functional applica-
tion.
n
If the stop is performed by the Emergency Switch, a manual reset is required (via SF_EmergencyStop).
n
If a monitoring time violation is detected (via SF_SafeStop1), manual error acknowledge is required to
allow a reset.
n
The 2 channel connectors of the emergency stop are monitored. An error is detected when both inputs
do not have the same status once the discrepancy time has elapsed (via SF_EQUIVALENT).
n
The functional stop in this example is performed as a safe stop issued from the functional application. A
restart interlock for this stop is not necessary.
Safety application examples
Example 1: Diagnostics concept > Functional description of safety functions
30.03.2017
AC500-S
426