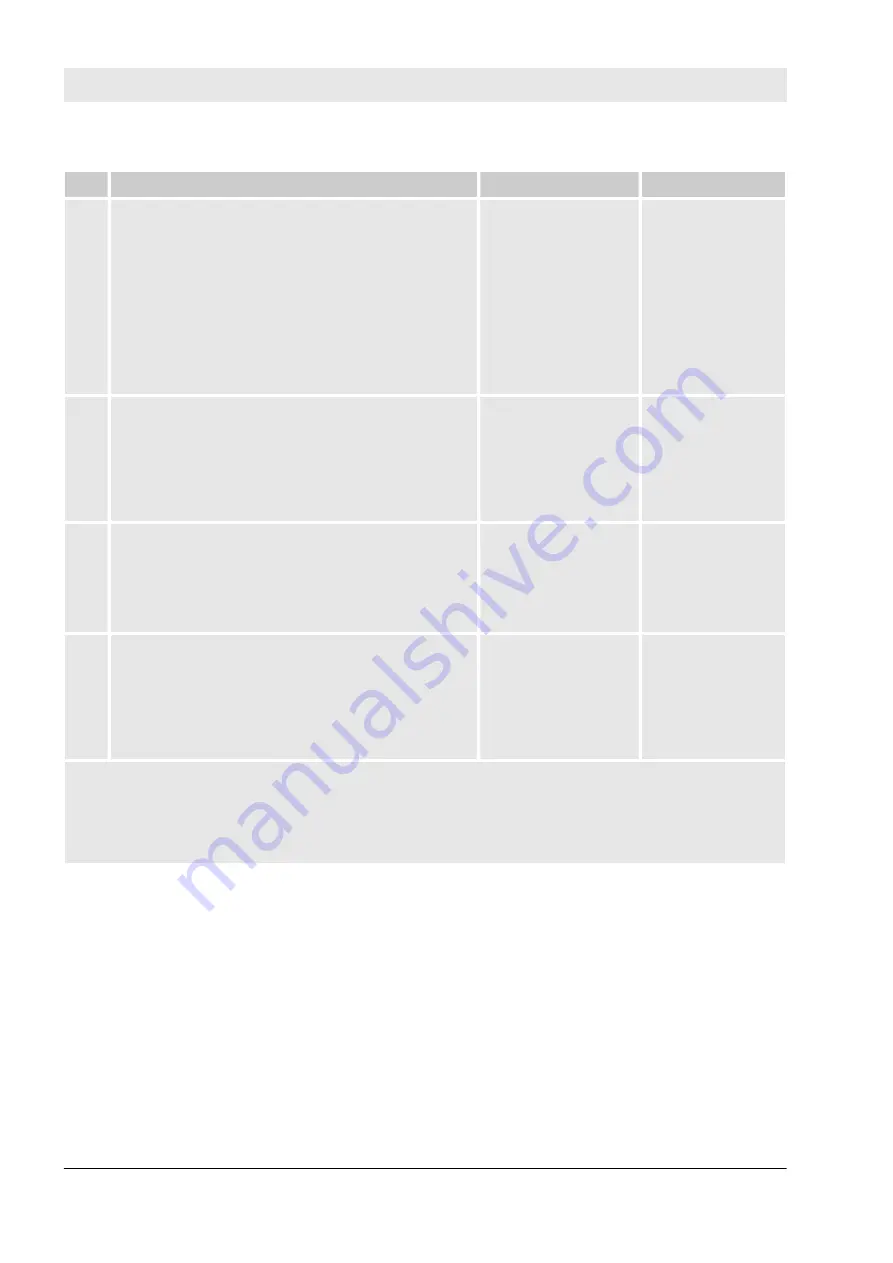
Nr.
Item to check
Fulfilled (Yes / No)?
Comment
7.
Verify that clear operation, maintenance and repair
procedures (organisation, responsibility, spare parts,
project data backup, etc.) for safety application are
defined.
Note:
n
Restart of the corresponding safety control loop is
only permitted, if there is no hazardous process
state, and after an operator acknowledgement
(OA_C).
8.
Verify that proper electrical contact is available
between Safety I/O modules (AI581-S, DI581-S and
DX581-S) and TU582-S terminal units. To do this,
after properly attaching Safety I/O modules to TU582-
S terminal units, press each Safety I/O module into
the TU582-S terminal unit with a force of at least 100
Newton.
9.
Ensure that average operating temperature for used
Safety modules (AC500-S and AC500-S-XC) does
not exceed 40 °C (e.g., temperature sensors could be
placed in the control cabinet and connected to AI581-
S safety analog input channels for temperature moni-
toring).
10.
Verify that no automatic reboot of PM5xx Non-safety
CPU is programmed in CoDeSys Non-safety pro-
gram. The automatic reboot of PM5xx would lead to
automatic restart of SM560-S Safety CPU, which is
directly attached to PM5xx. Such automatic restart of
SM560-S Safety CPU may not be accepted in some
safety applications.
Reviewer(s):
Machine/Application <ID>:
Signature:
Date:
6.5 Verification procedure for safe iParameter setting in AC500-S Safety I/Os
This verification procedure has to be performed before commissioning of the final safety application and rele-
vant validation tests to confirm that F_iPar_CRC was calculated for a correct set of iParameters.
Checklists for AC500-S Commissioning
Verification procedure for safe iParameter setting in AC500-S Safety I/Os
30.03.2017
AC500-S
412