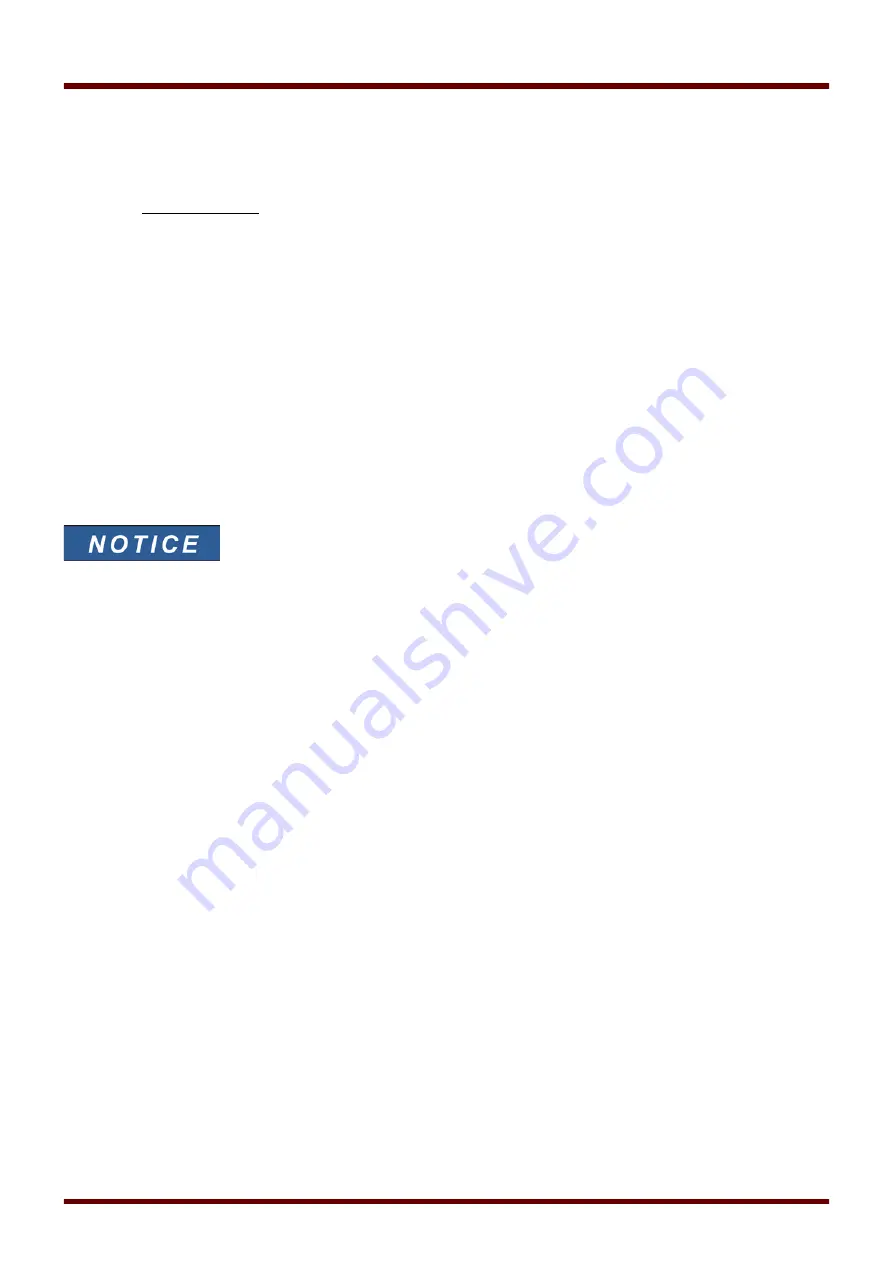
Protective Elements
Commissioning of the Cold Load Pickup Module
Object to be tested:
Testing the
Cold Load Pickup module
according to the configured operating mode:
•
I< (No current);
•
Bkr state (Breaker position);
•
I< (No Current) and Bkr state (Breaker position); and
•
I< (No Current) or Bkr state (Breaker position).
Necessary means:
•
Three-phase current source (if the Enable Mode depends on current);
•
Ampere meters (may be needed if the Enable Mode depends on current); and
•
Timer.
Test Example for Mode Bkr State (Breaker Position)
Mode I<: In order to test the tripping delay, start the timer and feed with an
abrupt change current that is distinctly less than the I<-threshold. Measure
the tripping delay. In order to measure the drop-out ratio, feed a current
with an abrupt change that is distinctly above the I<-threshold.
Mode I< and Bkr state: Combine the abrupt change (switching the current
ON and OFF) with the manual switching ON and OFF of the breaker.
Mode I< or Bkr state: Initially carry out the test with an abrupt changing
current that is switched ON and OFF (above and below the I<-threshold).
Measure the tripping times. Finally, carry out the test by manually
switching the breaker ON and OFF.
•
The breaker has to be in the OFF position. There must not be any load current.
•
The Status Display of the device shows the signal "CLPU.E
NABLED
“=1.
•
The Status Display of the device shows the signal ”CLPU.I<“=1.
•
Testing the tripping delay and the resetting ratio:
•
Switch the breaker manually ON and simultaneously start the timer.
•
After the the »
t Max Block (Release Delay)« timer has expired, the signal "CPLU.Enabled “=0 has to become
untrue.
•
Write down the measured time.
•
Manually switch the breaker OFF and simultaneously start the timer.
•
After the
»t load Off« timer has expired, the signal ”CPLU.E
NABLED
“=1 has to become true.
•
Write down the measured time.
Successful test result:
The measured total tripping delays or individual tripping delays, threshold values, and drop-out ratios correspond
with those values specified in the adjustment list. Permissible deviations/tolerances can be found in the Technical
Data section.
781
MCDLV4
DOK-HB-MCDLV4-2E
Содержание HighPROtec MCDLV4
Страница 1: ...Manual Line Differential Protection MCDLV4 Software Version 3 4 a DOK HB MCDLV4 2E Revision A English...
Страница 3: ...Order Code Order Code 3 MCDLV4 DOK HB MCDLV4 2E...
Страница 47: ...Installation and Connection 47 MCDLV4 DOK HB MCDLV4 2E...
Страница 164: ...Input Output and LED Settings 164 MCDLV4 DOK HB MCDLV4 2E...
Страница 433: ...Parameters 433 MCDLV4 DOK HB MCDLV4 2E...
Страница 457: ...Device Parameters 457 MCDLV4 DOK HB MCDLV4 2E...
Страница 473: ...Blockings 473 MCDLV4 DOK HB MCDLV4 2E...
Страница 822: ...Protective Elements Name Description Profibus Scada Cmd 16 Scada Command 822 MCDLV4 DOK HB MCDLV4 2E...
Страница 988: ...Protective Elements 988 MCDLV4 DOK HB MCDLV4 2E P P Q P Q P Q Q Q P S S...
Страница 989: ...Protective Elements 989 MCDLV4 DOK HB MCDLV4 2E Pr Q P Q P Qr...
Страница 1023: ...Protective Elements 1023 MCDLV4 DOK HB MCDLV4 2E...
Страница 1070: ...Supervision 1070 MCDLV4 DOK HB MCDLV4 2E...