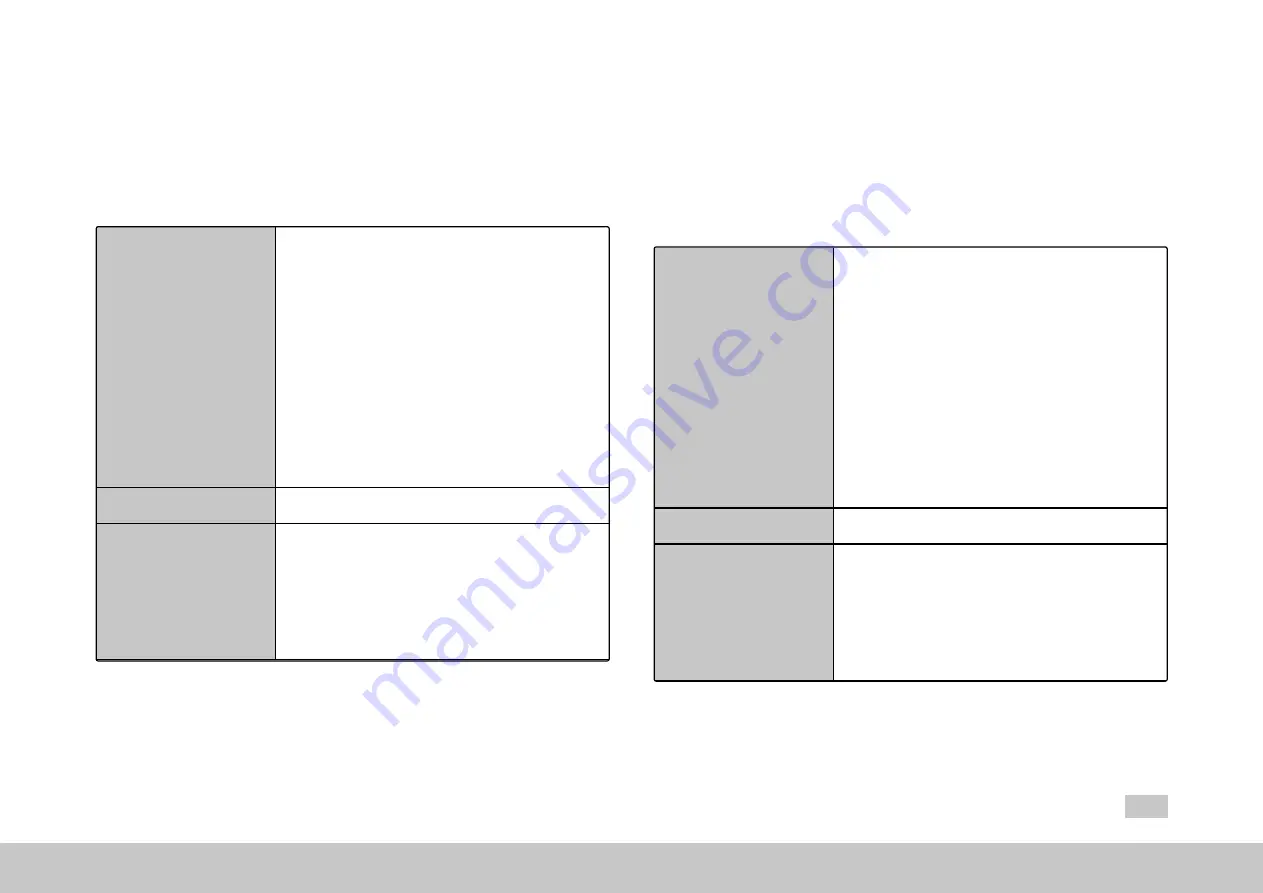
11.6.6.7 Error 5-7 (emergency code 2350h)
Cause: Fast I²t at high overload
Suggested steps:
Please check control and motion profile settings or reduce load
An overcurrent was
detected.
l
Please check current control settings and step
response.
l
Check the motor's saturation settings
(parameter MOT_LSigDiff). If the error
occurred in high-current range, lower
saturation values manually.
l
If possible, reduce the needed current,
especially in low-frequency range.
l
If possible, lower the switching frequency or
enable automatic frequency selection.
l
Check if the encoder offset is set properly.
l
Consider using an axis module with higher
current rating.
This is possibly a hardware
issue
If other measures fail to solve the problem, please
replace the servo drive.
This is possibly an EMC
issue. This is very likely if the
problem occurs when
switching on motor control
and/ or when connecting DC
link power supply.
l
Please check the device cabling for proper
connection.
l
Please check device grounding, i. e. the
connection to a metal backplane and cabinet
connection to earth.
l
Check motor grounding and motor cable
length.
MOOG
ID No.: CB40859-001 Date: 11/2020
MSD Servo Drive - Device Help
338
11 Alarms & warnings
11.6.6.8 Error 5-8 (emergency code 2350h)
Cause: Maximum fault current (= absolut sum current) in power-off detected
Suggested steps:
Please check ground connection or power wiring of motor and device, check current
values
An overcurrent was
detected.
l
Please check current control settings and step
response.
l
Check the motor's saturation settings
(parameter MOT_LSigDiff). If the error
occurred in high-current range, lower
saturation values manually.
l
If possible, reduce the needed current,
especially in low-frequency range.
l
If possible, lower the switching frequency or
enable automatic frequency selection.
l
Check if the encoder offset is set properly.
l
Consider using an axis module with higher
current rating.
This is possibly a hardware
issue
If other measures fail to solve the problem, please
replace the servo drive.
This is possibly an EMC
issue. This is very likely if the
problem occurs when
switching on motor control
and/ or when connecting DC
link power supply.
l
Please check the device cabling for proper
connection.
l
Please check device grounding, i. e. the
connection to a metal backplane and cabinet
connection to earth.
l
Check motor grounding and motor cable
length.