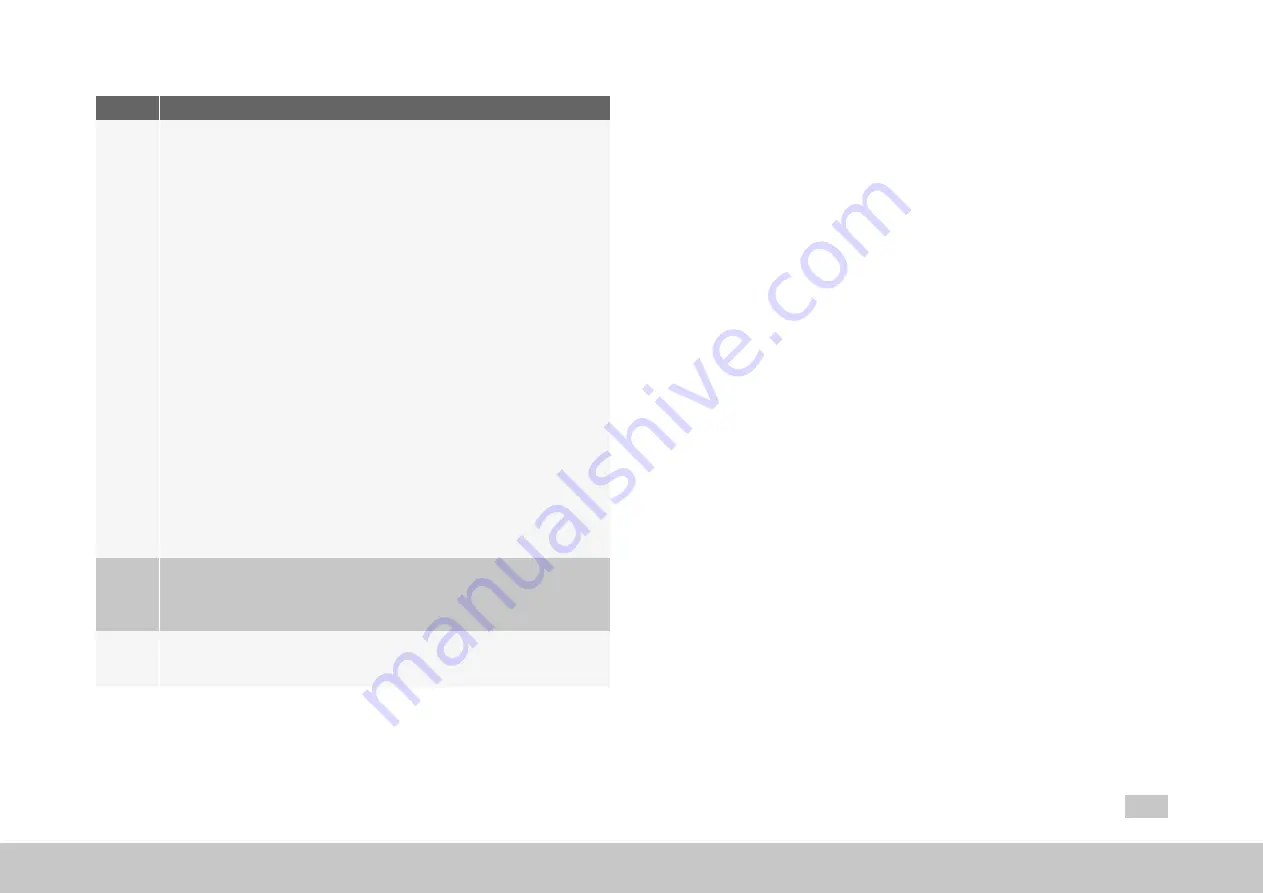
Step
Action
3
Configure the auto commutation function
Mode 1
As described in Section "Auto commutation" on page 92 or
Recommendation:
P 390[0] = 1
P 392[0] =500
P 392[1] =500
P 392[2] =500
P 392[3] =500
P 393[0] = Rated motor current
P 393[1] = Rated motor current
Mode 2
Parameters 792.1 and 792.2 are used as the measuring frequency and
measuring amplitude (see step 2)
Recommendation:
P 794[0] = 100 ms
P 794[1] = 50% of rated motor current
P 794[2] = 250 ms
4
Starting the expanded speed control circuit is not absolutely necessary,
but will result in control with better dynamic performance. The circuit can
be started by setting
P 350[0] - SEL_ObserverMethod
to a value of 4.
P 339 - CON_SCON_Kalman
can be used for tuning purposes.
5
If necessary, adjust the noise covariance matrices and the filter time
constants for the expanded speed control circuit (changes will take effect
in real-time).
Table 6.30: Configuring the Kalman filter for sensorless control (continue)
MOOG
ID No.: CB40859-001 Date: 11/2020
MSD Servo Drive - Device Help
97
6 Encoder
In order to make the encoderless control commissioning process easier, a function
used to calculate the position difference between encoderless control and a real
encoder can be activated. To use this function, the encoder channel that will be used
for the comparison must be selected in P 797[0] - ENC_CH4_Kalman_Compare.
Make sure that the encoder channel is configured correctly! This also includes the
encoder mounting angle P 349[0] - CON_FM_MConOffset. In addition to the
position difference, the encoder angle is also used to determine the d current and q
current as scope variables.
6.8.2 Sensorless asynchronous motor control
In sensorless mode, the other variables (position, speed, torque) are calculated
based on characteristic motor data and the measured currents and voltages on the
motor. A problem is determining position at standstill or at low speed.