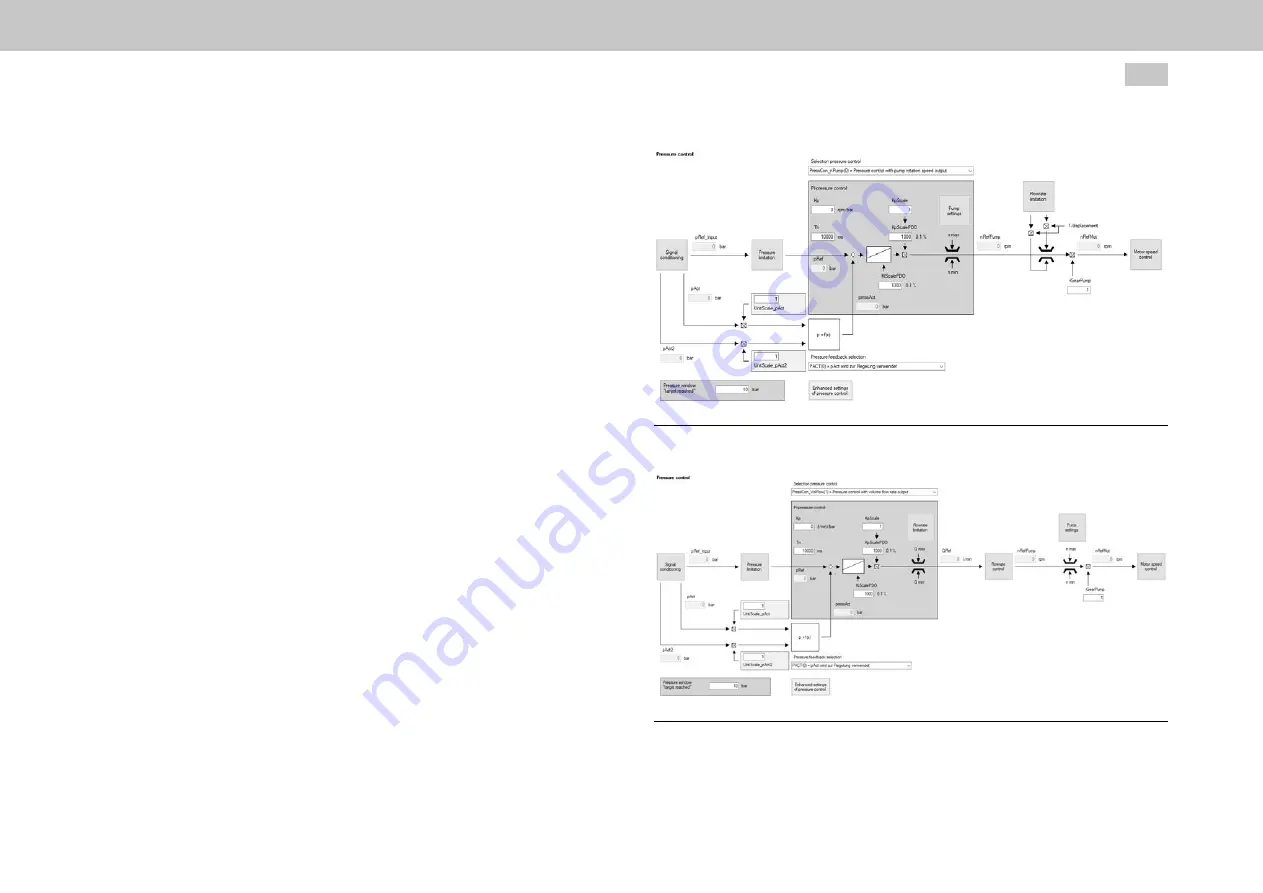
pumped for the same pressure change. Accordingly, the pressure controller’s gain
needs to be reduced at higher pressures in order to maintain a constant pressure
control circuit dynamic performance. Because of this, pressure-dependent controller
gain scaling has also been incorporated. This scaling can be configured with a
characteristic curve (P 2853 - HYD_PressConScale).
The pressure controller settings were duplicated in P 2874 HYD_PressCon2. With
this it is possible to select a different controller setting for a selected table motion
block. The second controller data set can be selected in the table motion block using
P 2863 HYD_TabCtr bit 12.
In order to provide feedback to a higher-order control system, a setpoint window for
“Pressure reached” (Para 2850.9 - PressWindow) can be specified. If the actual
value is within this window, the bit “InWindow” (bit 13) is set in the status word (
also section "Hydraulic Motion profile" on page 190). Furthermore, a second
KpScale P 2879[0] PressCon1_KpScalePDO, P 2879[1] PressCon2_KpScalePDO
has been introduced for operation via one controller and it can be written cyclically
via the PDO channel. It should be noted here that both factors act one after the other
and influence each other.
MOOG
ID No.: CB40859-001 Date: 11/2020
MSD Servo Drive - Device Help
197
7 Control
Image 7.67: Mask of pressure control with pump speed output
Image 7.68: Mask of pressure control with volumetric flow rate output.