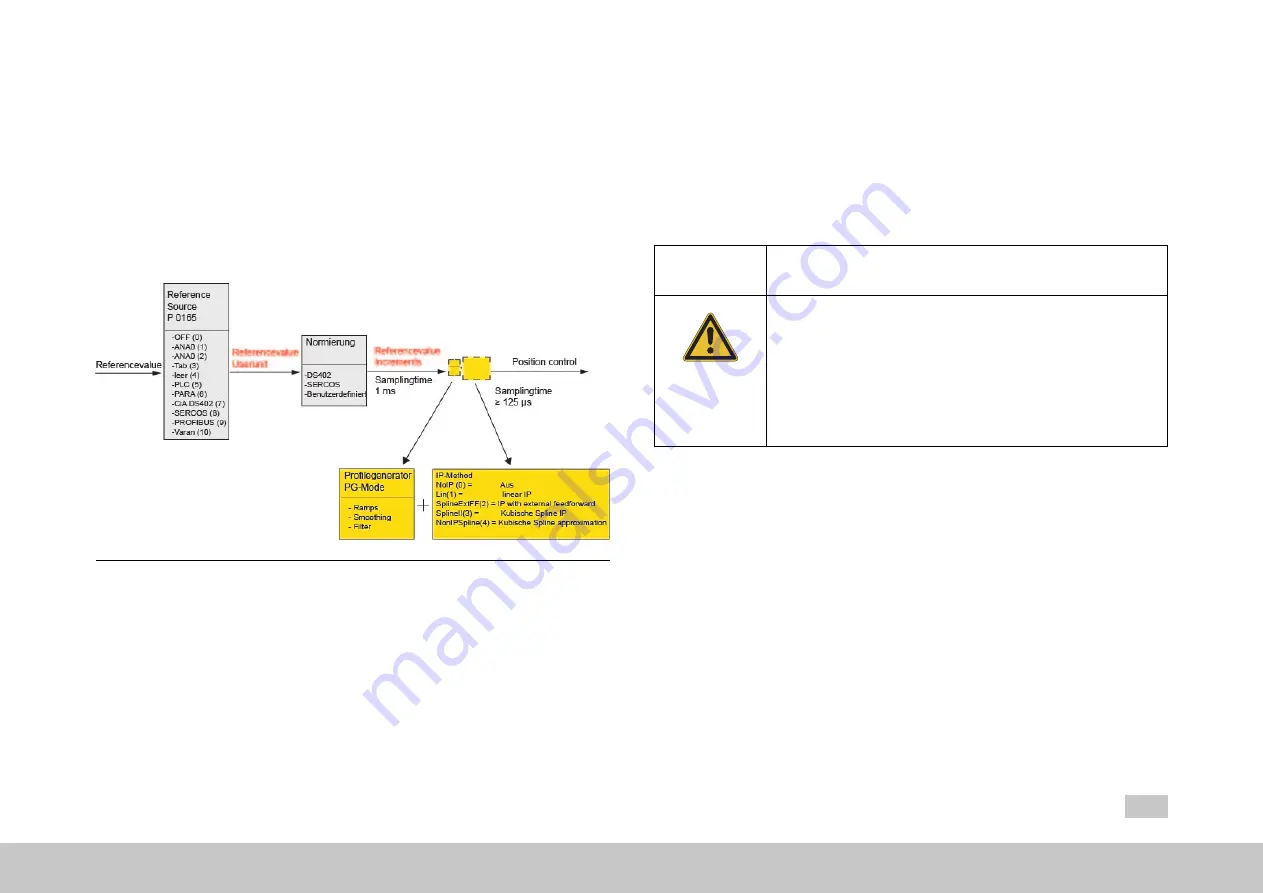
l
The position references are used to generate pre-control values for speed
and acceleration. These are scanned at the sampling time of the position
controller (normally 125 µs) and switched to the control loops.
8.3.2.1 Motion profile / Basic settings
In this screen the basic settings for the motion profile are made according to the list
boxes. If Profile Generator and IP mode are enabled, the reference value is
influenced by both functions.
Image 8.27: PG mode with position control
8.3.3 IP mode with speed control
In IP (Interpolation) mode the appropriate reference source and correct scaling of
units are selected for the speed reference before the reference is passed via the
interpolator to the control. Linear interpolation is always applied in this process.
MOOG
ID No.: CB40859-001 Date: 11/2020
MSD Servo Drive - Device Help
243
8 Motion profile
Interpolation (IP) mode
l
Reference values are interpolated in linear mode before being switched to
the control loops.
l
The profile generator is inactive.
l
Ramps and smoothing are inactive.
l
The reference values are switched directly to the closed-loop control.
CAUTION!
Your system/motor may be damaged if put into operation in
an uncontrolled or inappropriate manner.
Improper conduct can cause damage to your system /
machine.
l
Before the “Start” step, make absolutely sure that a valid
setpoint has been entered, as the configured setpoint
will be immediately transmitted to the motor after the
motor control function starts, which may result in the
motor accelerating unexpectedly.
Speed control in IP mode:
l
Control mode
P 300[0] - CON_CfgCon
= speed control or setting via Modes
of Operation (CAN, EtherCAT®)
l
Selection of reference source
P 165[0] - MPRO_REF_SEL
l
Scaling
l
Linear interpolation is always applied in speed control.
l
Bus sampling rate: the bus sampling time is custom-set according to the
application.