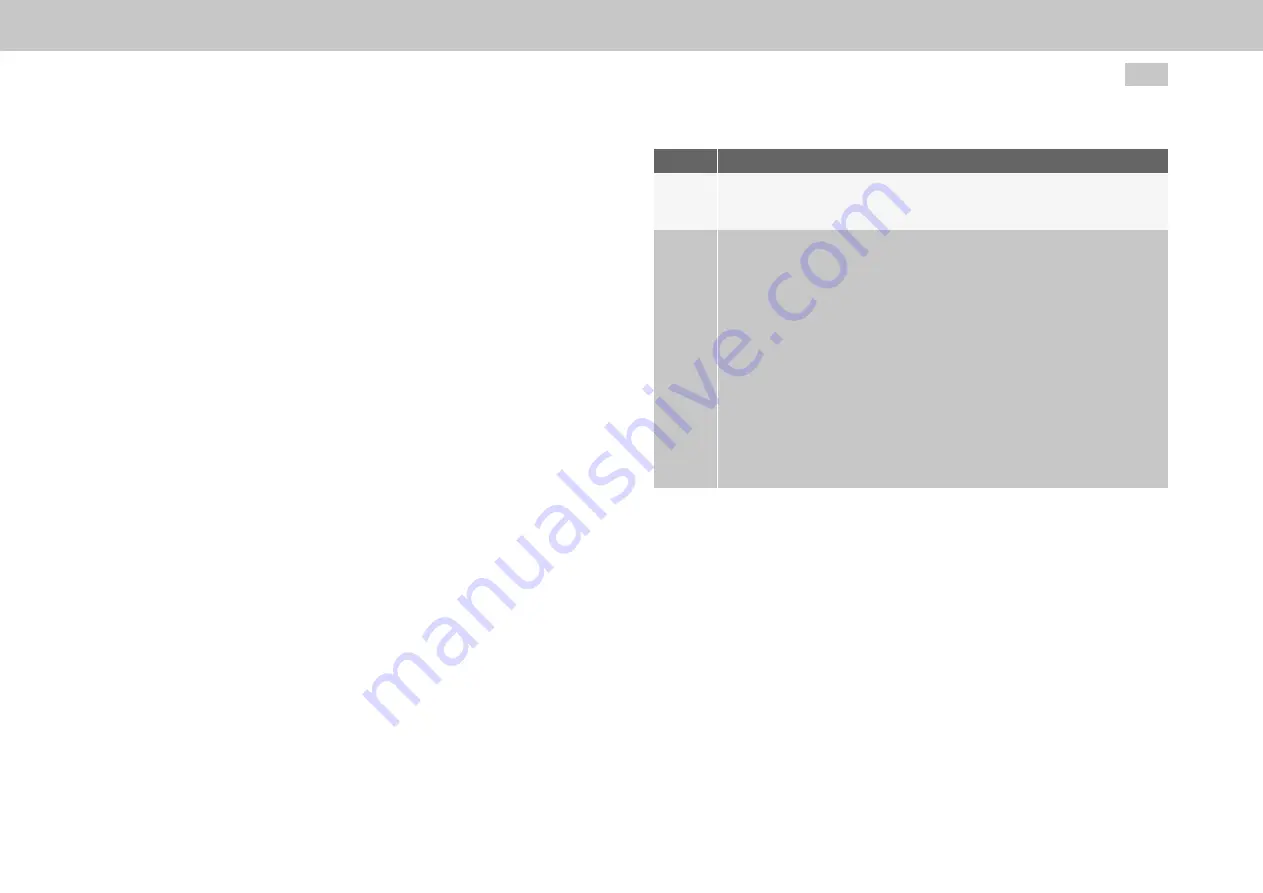
combination with a test signal when the motor is stopped. In addition, the total
moment of inertia resulting from the motor and the connected load must be set as
accurately as possible.
The encoder communications will be used to calculate and pass the actual speed
and actual position. Accordingly, in order to select the sensorless method, a value of
2 must be set for encoder channel 4 in the selector (P 508[0] - ENC_CH4_Sel = 2),
and a value of 4 must be set for P 520[0] - ENC_MCon, P 521[0] - ENC_SCon and
P 522[0] - ENC_PCon.
The Kalman filter needs to be configured further by following the steps below:
MOOG
ID No.: CB40859-001 Date: 11/2020
MSD Servo Drive - Device Help
96
6 Encoder
Step
Action
1
Configure noise covariance matrices Q and R. This should be done
automatically by setting the control parameter for encoder channel 4
(
P 783[0] - ENC-CH4-Ctrl
) to a value of 6.
2
Manually configure the test signal generator:
Recommendation:
Sinusoidal test signal in d axis
P 792[09] = 1
P 792[19] = 500 Hz
P 792[2] = P 792[9] = 10% of rated motor current
P 792[79] = 15% of rated motor speed
P 792[89] = 5% of rated motor speed
P 792[9] = 30% of rated motor current
Set the other values to 0
Or set the control parameter for encoder channel 4 (
P 783[0] - ENC-CH4-
Ctrl
) to a value of 3, which will trigger a general initialization routine in
which steps 1 and 2, as well as encoder initialization, will be
automatically carried out based on the motor parameters.
Table 6.30: Configuring the Kalman filter for sensorless control