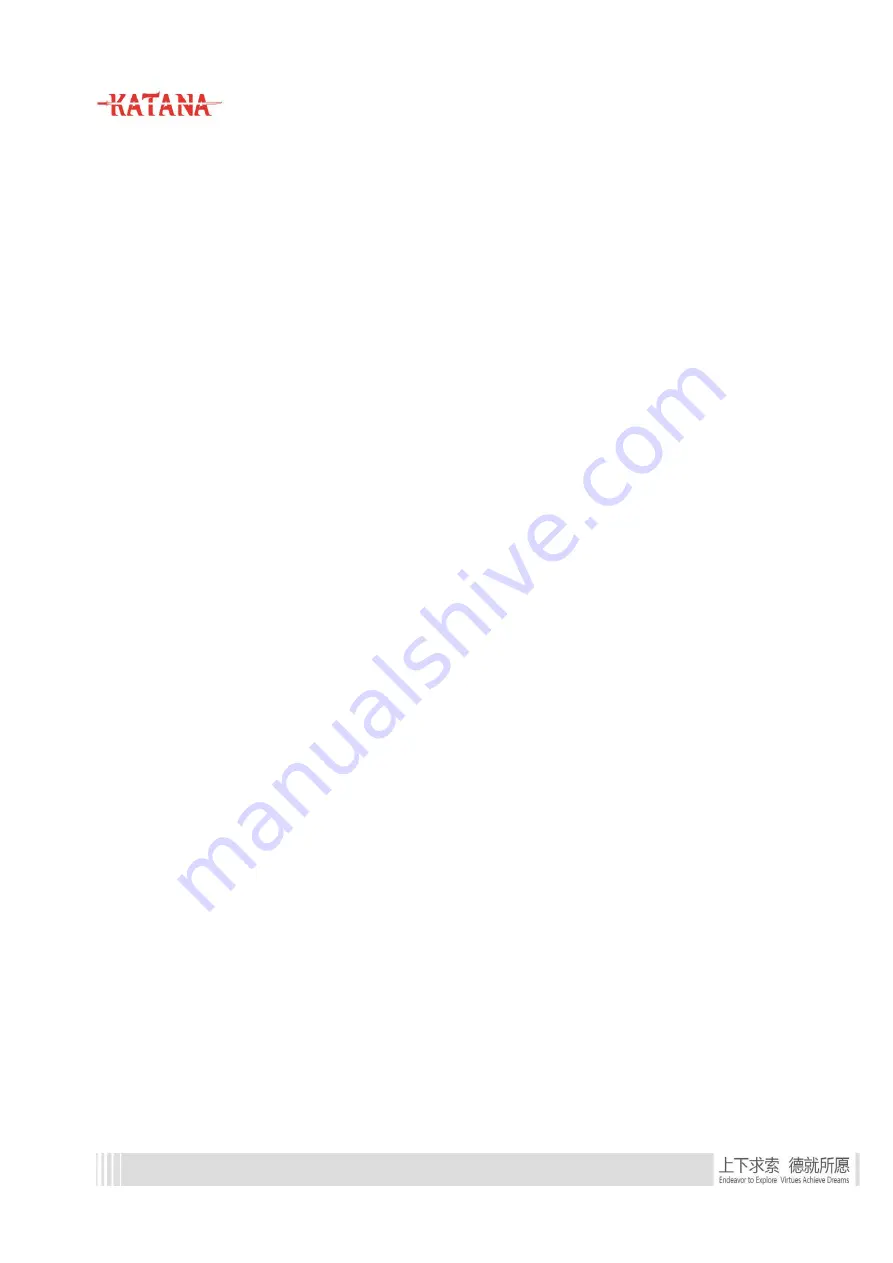
90
KATANA S610M Inverter Specialized for Elevator Manual
After auto tuning is completed, F01.16 will be set to 0 automatically.
Synchronous motor parameters auto tuning is identified by position, operation are shown below:
F01.16 = 0
:
No action
F01.16 = 1: action (synchronous motor in rotary state)
The synchronous motor is in static state before being in rotary state.
Alter the value of F01.16 to non-zero and give run command, the synchronous motor will start parameters
self-tuning. After that, the value of F01.16 will be automatically restored to 0, and motor parameters will be
automatically writen in F01.10~F01.13, the location angle of encoder will be automatically written in F01.14,
with the location angle of Z pulse be written in F01.15 (valid for rotation identification of synchronous motor),
encoder direction is entered F08.02 automatically. If bit9 of F11.01 (bit 1 of LED hundreds digit: current loop PI
parameter tuning calculation enable) enable, parameter of current loop will automatically write into
F06.11~F06.14.
F01.16 = 2: action (synchronous motor in static state 1)
Choose static identification if the motor cannot be unloaded. When the synchronous motor is in static state,
the sound of electricity current can be heard, after that motor parameters will be automatically written in
F01.10~F01.13, the location angle of encoder will be automatically written in F01.14, check the value of F01.14
(the initial pole angle of synchronous motor); If bit9 of F11.01 (bit 1 of LED hundreds digit: current loop PI
parameter tuning calculation enable) enable, parameter of current loop will automatically write into
F06.11~F06.14.
Put the inverter in inspection state and start running upward/downward after learning initial angle. If error is
reported immediately, or the elevator is running abnormally, the probable cause is that the encoder is in reverse
direction, then the function code F08.02 should be modified. After that, restart static identification. If the control
direction is in reverse with the actual running direction, then modify F00.05 (running direction setting). When
done, put the inverter in inspection state again to observe whether the current is normal, the motor running is
stable, and the running direction complies with given direction. Record the angle displayed by F01.14 and the
running current if all these are correct and normal. Repeat the procedure for three times and record the angle
identified each time. If the deviation is within ±30 degree every time, it’s defined normal. The deviation is
supposed to be better at its smallest value. Take the initial pole angle when the running current of the motor is the
lowest.
F01.16 = 3: action (synchronous motor in static state 2)
Difference of asynchronous motor tuning between static state 2 and 1: add encoder direction identification on
2, after completing synchronous motor identification, encoder direction automatically write in F08.02. At later
stage of tuning, this mode will open the brake to learn encoder direction (learning with load is available).
F01.16 = 4: action (synchronous motor in static state 3)
Difference of asynchronous motor tuning between static state 3 and 1: 3 could automatically calculate current
loop parameters and write them in F06.11~F06.14.