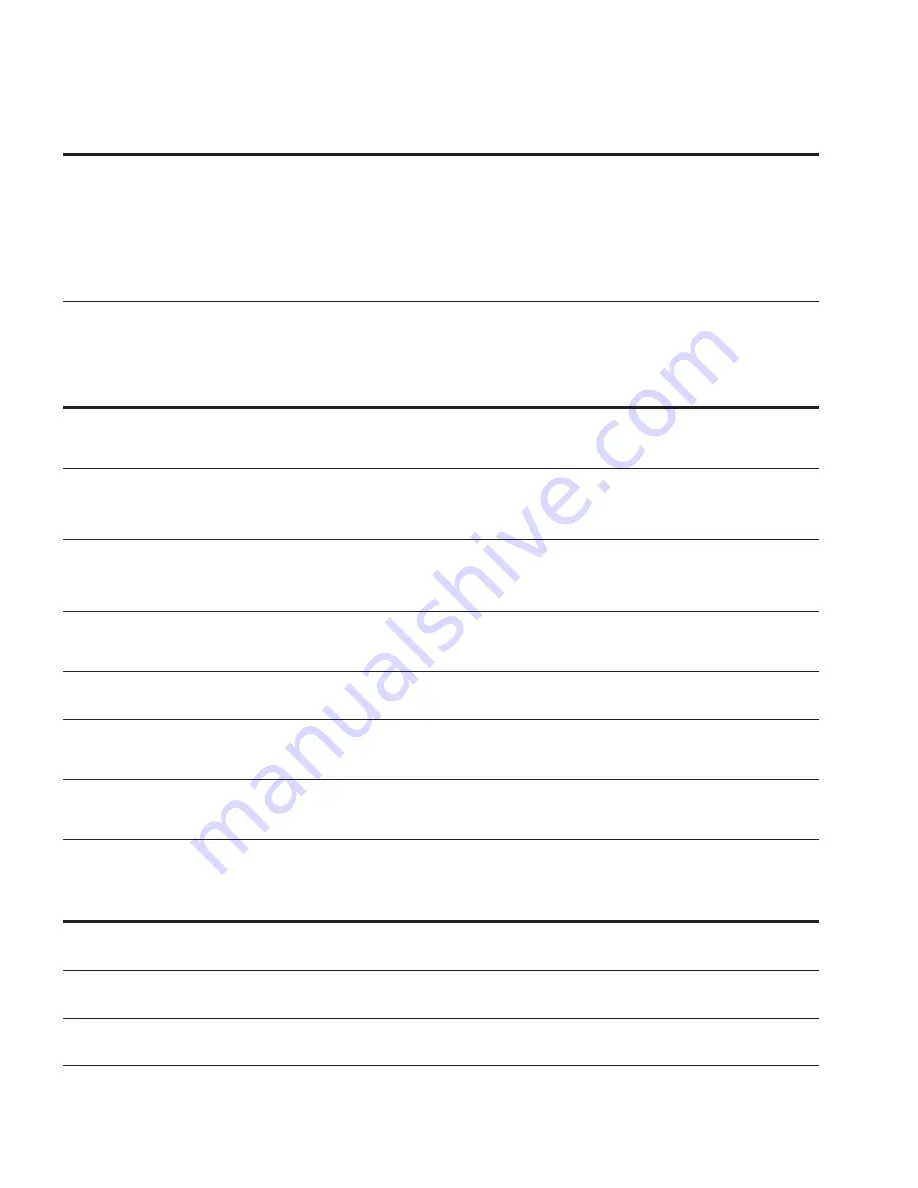
155
SPX advanced – description of parameters
SPX ADVANCED APPLICATION MANUAL
SVCH0203—October 2017 www.eaton.com
Code
ID
Description
Notes
P1.16.13
1569
This fault simulation cover wide range of different faults in drive, see fault description
for details.
B06 = +64 = Simulates encoder fault (F43)
B07 = +128 = Simulates over temperature warning (W14)
B08 = +256 = Simulates over temperature fault (F14)
Warning bit needs to be active that fault will come in simulation. If fault bit is left
active drive will go fault state at warning limit when drive temperature will rice to
warning level.
B09 = +512 = Reserved
Code
ID
Description
Notes
P1.17.1.1
118
PID controller gain ID118 “PID-contr gain”
This parameter defines the gain of the PID controller. If thevalue of the parameter is
set to 100% a change of 10% inthe error value causes the controller output to change
by10%. If the parameter value is set to 0 the PID controlleroperates as I-controller.
P1.17.1.2
119
PID controller I time “PID-contr I time”
The parameter ID119 defines the integration time of the PIDcontroller. If this parameter
is set to 1,00 second a changeof 10% in the error value causes the controller output
tochange by 10.00%/s. If the parameter value is set to 0.00 sthe PID controller will
operate as P controller.
P1.17.1.3
132
PID controller D time“PID-contr D time”
ID 132 defines the derivative time of the PD controller. Ifthis parameter is set
to 1.00 seconds a change of 10% inPID error value during 1.0 seconds cause the
controlleroutput to change 10%. If the parameter is set to 0 the PIDcontroller operates
as a PI controller.
P1.17.1.4
1795
Engineering unit “engineering unit”
This defines the unit used in the process setting the valueallow for easy set up and
control of the PID controller byallowing the controller to display and control values
thatmatch the process.
P1.17.1.5
359
PID minimum limit “PID min limit”
This parameter sets the low limit in engineering units of the process this will typically
match the low limit of the measurement device measuring the feedback value.
P1.17.1.6
360
PID maximum limit “PID max limit”
This parameter sets the maximum limit in engineering unitsof the process this will
typically match the maximum limit ofthe measurement device measuring the feedback
value.
P1.17.1.7
342
Error inversion “error inversion”
This inverts the error in the PID allowing the output to be inverted.
Not inverted = The drive will increase speed to increase the feedback value
Inverted = The drive will increase speed to decrease the feedback value
Code
ID
Description
Notes
P1.17.2.1
332
PID set point source “setpoint source”
This parameter allows the selection of two independent setpoint sources source 1 or
source 2 the section can also bemade with a digital input.
P1.17.2.2
334
PID source 1 select“source 1 sel”
This sets the source of the source 1 set point value this can come from an analog input,
keypad, or fieldbus.
P1.17.2.3
335
PID source 2 select “source 2 sel”
This sets the source of the source 2 set point value this can come from an analog input,
keypad, or fieldbus.
5.18 PI control
5.18.1 Basic settings
5.18.2 Set points