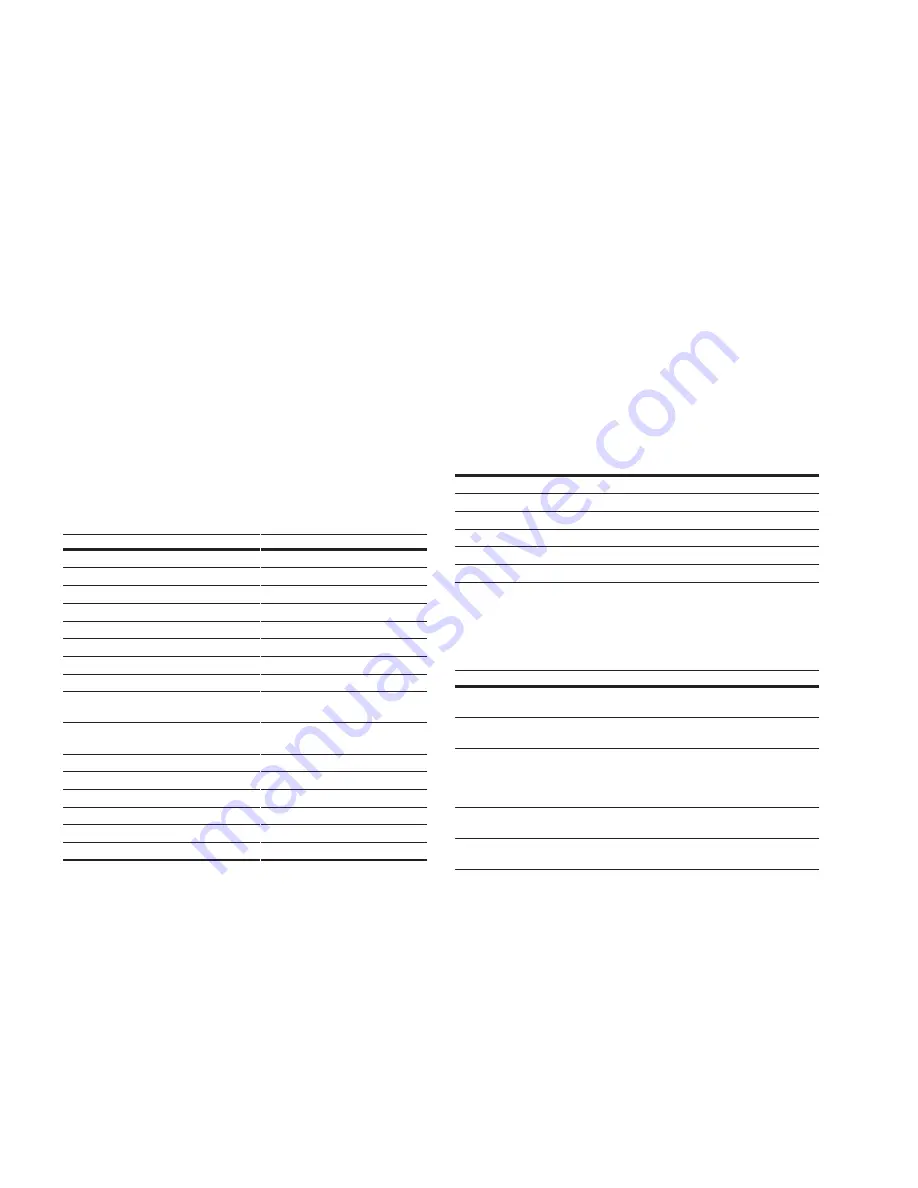
9
SPX Advanced application – monitoring values
SPX ADVANCED APPLICATION MANUAL
SVCH0203—October 2017 www.eaton.com
3.2.1 Monitoring values 2
V7.24.1
Current A
ID 1113
Unfiltered motor current, recommended signal
for NCDrive monitoring.
Drive Synch Operation Master drive:
This value is the total current of the system
divided by number of drives in the system
(SbLastID). SbLastId cannot be changed; it
needs to be set according to how many drives
are linked with system bus.
Drive Synch Operation Follower drive:
This value is current of drive own power unit.
V7.24.2
Torque
%
ID 1125
Unfiltered motor torque.
V7.24.3
DC Voltage V
ID 44
Unfiltered DC link voltage.
V7.24.4
Application status word
ID 43
“status word 1”
Application status word combines different
drive statuses to one data word.
Recommended signal for NCDrive monitoring.
Application status word 1 ID43
False
True
b0
Flux not ready
Flux ready (>90 %)
b1
Not in ready state
Ready
b2
Not running
Running
b3
No fault
Fault
b4
Direction forward
Direction reverse
b5
Emergency stop active
Emergency stop NOT active
b6
Run disabled
Run enable
b7
No warning
Warning
b8
Power positive
Power negative or Gen torque or
current limit active
b9
Parameter set 1 active
(or no set used)
Parameter set 2 active
b10
Brake chopper operating
b11
No DC brake
DC brake is active
b12
No run request
Run request
b13
No limit controls active
Limit control active
b14
External brake control off
External brake control ON
b15
Not used
Not used
V7.24.5
Shaft frequency Hz
ID1124
Shaft Frequency used by motor control.
V7.24.6
Output power kw
ID 1508
Unfiltered electrical drive output power.
V7.24.7
Measured temperature 1 Cº
ID 50
V7.24.8
Measured temperature 2 Cº
ID 51
V7.24.9
Measured temperature 3 Cº
ID 52
V7.24.10
Measured temperature 4 Cº
ID 69
V7.24.11
Measured temperature 5 Cº
ID 70
V7.24.12
Measured temperature 6 Cº
ID 71
Separate measurement from two PT100 board.
The signal has 4 s filtering time.
V7.24.13
ABS encoder revolutions
ID55
Absolute encoder revolution information.
V7.24.14
ABS encoder position
ID54
Absolute encoder position within one rotation.
See encoder manual for scaling.
V7.24.15
Step response Hz
ID 1132
Frequency error. Compares ramp output
to actual encoder frequency with 0,001 Hz
accuracy. Can be used for speed control tuning
in closed loop control.
V7.24.16
Actual power factor
ID 68
Estimated power factor value.
V7.24.17
Flux current
ID 72
Flux producing current component 100,0 %
equals nominal flux current.
V7.24.18
Regulator status ID 77
Regulator status ID77
b0
Motoring current regulator status
b1
Generator current regulator status
b2
Motoring torque regulator status
For CL monitor B0
b3
Generator torque regulator status
For CL monitor B1
b4
Over voltage regulator status
DC Voltage
b5
Under voltage regulator status
DC Voltage
V7.24.19
Frequency delta
ID 1847
Change of final frequency reference in Hz/s.
V7.24.20
Data logger trigger word
ID 97
Data logger trig word ID97
Function
Comment
b0
Fault status
Logger is triggered when there is
a fault
b1
Warning status
Logger is triggered when there is a
warning
b2
Auto reset warning
Logger is triggered when there is
a fault that has been defined to be
automatically reset. This bit can be
used to get the first fault situation.
b3
Fault status OR warning status
B0 OR B1 triggering situation has
happened
b4
Fault status OR auto reset warning
B0 OR B2 triggering situation has
happened
V7.24.21
Encoder 2 frequency
OPT-D7 board second input encoder frequency.
V7.24.22
Operation hours
Running state hours.
V7.24.23
Application status word 2 ID 89 “status word 2”
Different statuses from the drive, useful for ID
Control DO functions.