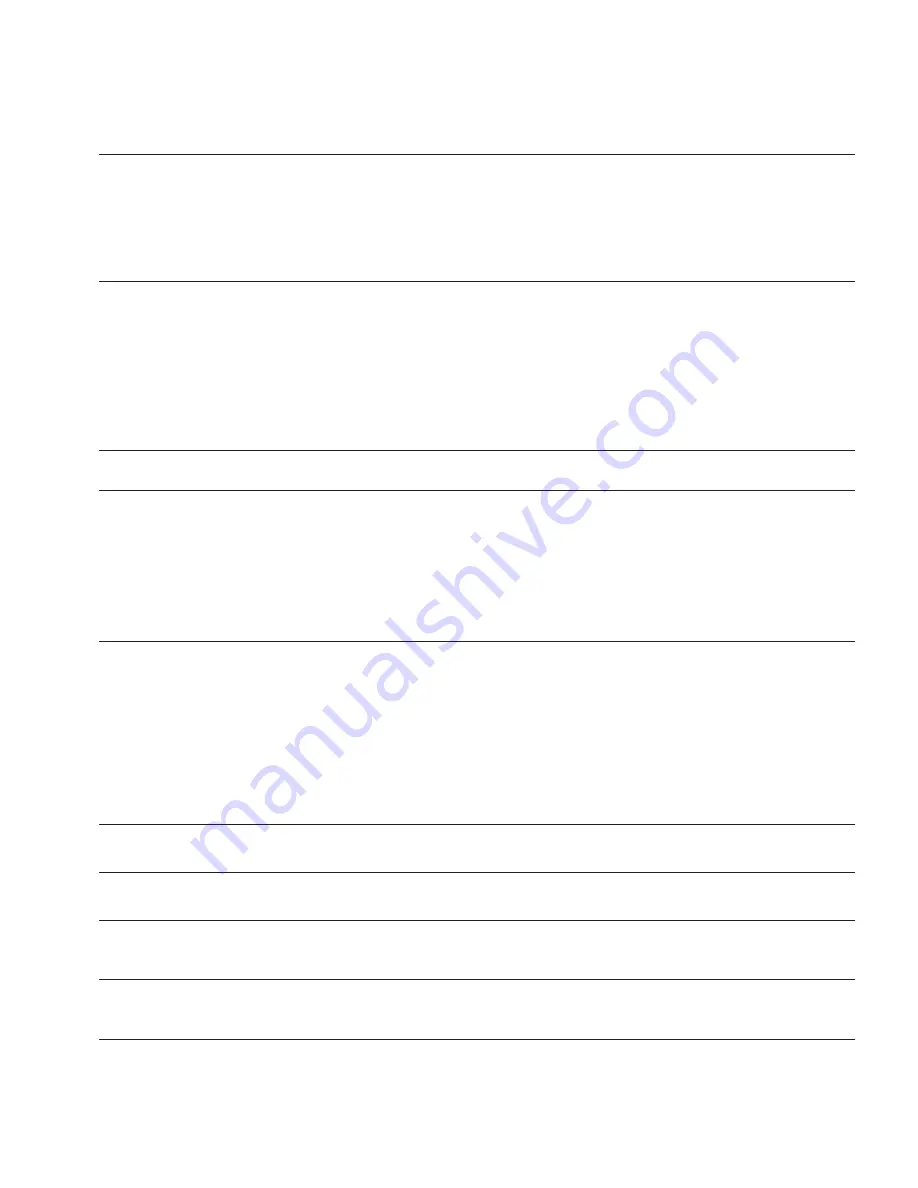
124
SPX advanced – description of parameters
SPX ADVANCED APPLICATION MANUAL
SVCH0203—October 2017 www.eaton.com
Code
ID
Description
Notes
P1 .10 .2
1516
Modulator type modulator type”
3 = Software modulator 3
Unsymmetrical BusClamb in which one switch always conducts 120 degrees to
negative DC-rail to reduce switching losses. However, upper and lower switches are
unevenly loaded and the spectrum is wide.
4 = Software modulator 4:
Pure sinewave, sinusoidal modulator without harmonic injection. Dedicated to be used
in back to back test benches etc. to avoid circulating third harmonic current. Drawback
is that required DC voltage is 15% higher compared to other modulator types.
P1 .10 .3
1084
Control options “Control options”
B01 = Disable open loop power limit function
B06 = Activate Closed Loop type speed limit function in Open Loop
B07 = Disables switching frequency decrease due to drive temperature rise
B08 = Disable Encoder fault when brake is closed
B12 = Disable Process Data locking function when Profibus communication fails. When
using Profibus, an occurring communication fault will lock the process data to
previous values. This bit will disable the locking of process data forcing the
values to zero.
B13 = Disable only acceleration when using DI Acc/Dec prohibit function
This bit can only be used with
Profibus.
P1 .10 .4
1798
Control options 2 “ControlOptions2”
B10 = Possibility to revert back to “old” operation. See details from Release Note.
P1 .10 .5
1560
Advanced Options 1 “AdvancedOptions1”
B00 = Disable Synchronous modulation
B01 = Use encoder information to slip compensation in Open Loop Speed control
B02 = Disable encoder fault
B03 = Disable slip compensation for reverse direction
B06 = Enable synchronous symmetrical modulation
B07 = Automatically handled by application logic.
B15 = Cosphii = 1 control. This controls the motor reactive power to zero. Possible to
use only with PMS motors in closed loop control.
P1 .10 .6
1561
Advanced options 2 “AdvancedOptions1”
B00 = Sensorless control for PMS motors. This is an open loop control but uses the
same control system than the normal closed loop control. Calculations try to
estimate the encoder speed instead of using the encoder signal. This mode has
speed and torque range limitations and therefore application limitations. A lower
speed controller gain may be required to gain stability. Useful for generator
applications.
B04 = Enable Start Positioning damping active if PMSM
B09 = I/f control for PMS motors. PMS motor can be started with I/f control. Used
with high power motor when there is low resistance in motor and U/f is difficult
to tune to be stable.
B13 = Changes automatically depending on Drive Synch operation
P1 .10 .7
1563
Advanced options 4 “AdvancedOptions4”
Reserved for future use. Some bits are controlled by application software so value may
not be always zero.
P1 .10 .8
1564
Advanced options 5 “AdvancedOptions5”
B11 = Current measurement anti-aliasing for low switching frequencies, prevents
torque calculation distortions. Requires Software Modulator 1.
P1 .10 .9
1565
Advanced options 6 “AdvancedOptions6”
B05 = To reduce aliasing effects in current measurement, it is possible to take an
average from all internal samples taken at fast time level. It must be noted, that
this mode does not affect the motor control, only monitoring.
P1 .10 .10
1424
Restart Delay “Restart Delay OL”
The time delay within which the drive cannot be restarted after a coast stop and flying
start is not in use. Closed Loop control mode and the flying start use a different delay
see P1.9.11.