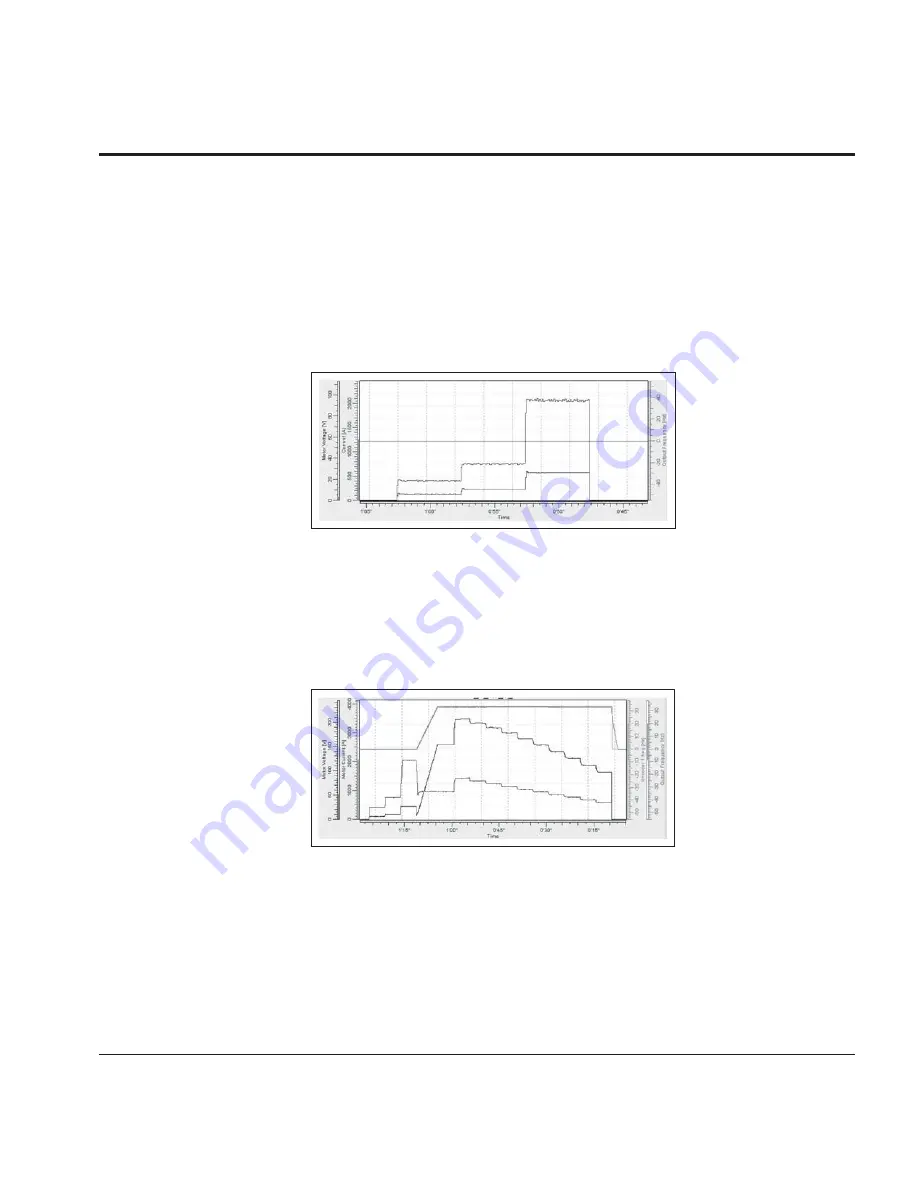
46
SPX advanced – description of parameters
SPX ADVANCED APPLICATION MANUAL
SVCH0203—October 2017 www.eaton.com
Code
Id
Descriptions
Notes
P1.1.10
631
Identification “Identification”
Identification Run is a part of tuning the motor and the drive specific parameters.
It is a tool for commissioning and service of the drive with the aim to find as good
parameter values as possible for most drives. The automatic motor identification
calculates or measures the motor parameters that are needed for optimum motor
and speed control.
0 = “No Action” No action
No identification requested.
1 = “ID No Run” - Identification without rotating the motor Current is applied to the
motor but shaft will not be rotated. U/f settings are identified. This identification is
minimum requirement if motor is only to be used in open loop control. It is however
recommended to make always identification with rotating motor if need for closed
loop control comes after mechanics are connected to shaft.
Example of behaviour
2 = “ID With Run” - Identification with motor rotating
Shaft is rotated during identification.
This identification must be run without load on motor shaft. U/f settings and
magnetization current are identified. This identification should be run regardless of
the final operation mode (closed loop or open loop) to get the best performance from
the motor. When identification with motor rotation is successfully finished the drive
starts to use internal slip estimator to compensate the motor temperature changed.
SCTorqueChainSelect B5 & B6.
Example of behaviour
3 = “Enc. ID Run” - Encoder identification run
The motor shaft is rotated during identification.
IM: If performed for induction motor encoder pulse number and direction are
identified. Can be used if the is no encoder information available, correct result can
be achieved only when motor in unloaded.
PMSM: This selection is used for PMS motor if automatic angle identification is not
suitable for used motor (angle is identified automatically in every start if PMSM
Shaft Position parameter is zero). This identification run will update PMSM Shaft
Position parameter based on absolute position of the encoder or Z pulse position of
incremental type encoder.
Set motor control mode to
Frequency Control before
identification!
During identification drive will
not open mechanical brake
for safety reasons. If motor
rotation requires that brake
is opened this needs to be
achieved externally.
During identification run torque
and power limits should be
above 100 %. Also current limit
should be above motor nominal
current.
During identification run
acceleration time should be
below 20 second.
If switching frequency is
changed after identification
it’s recommended to do
identification run again.
Small motor with long motor
cabled may require reduction
of switching frequency if
identification is not successful.
Identification needs to be
remade if encoder position
related to motor is changed e.g.
due maintenance.