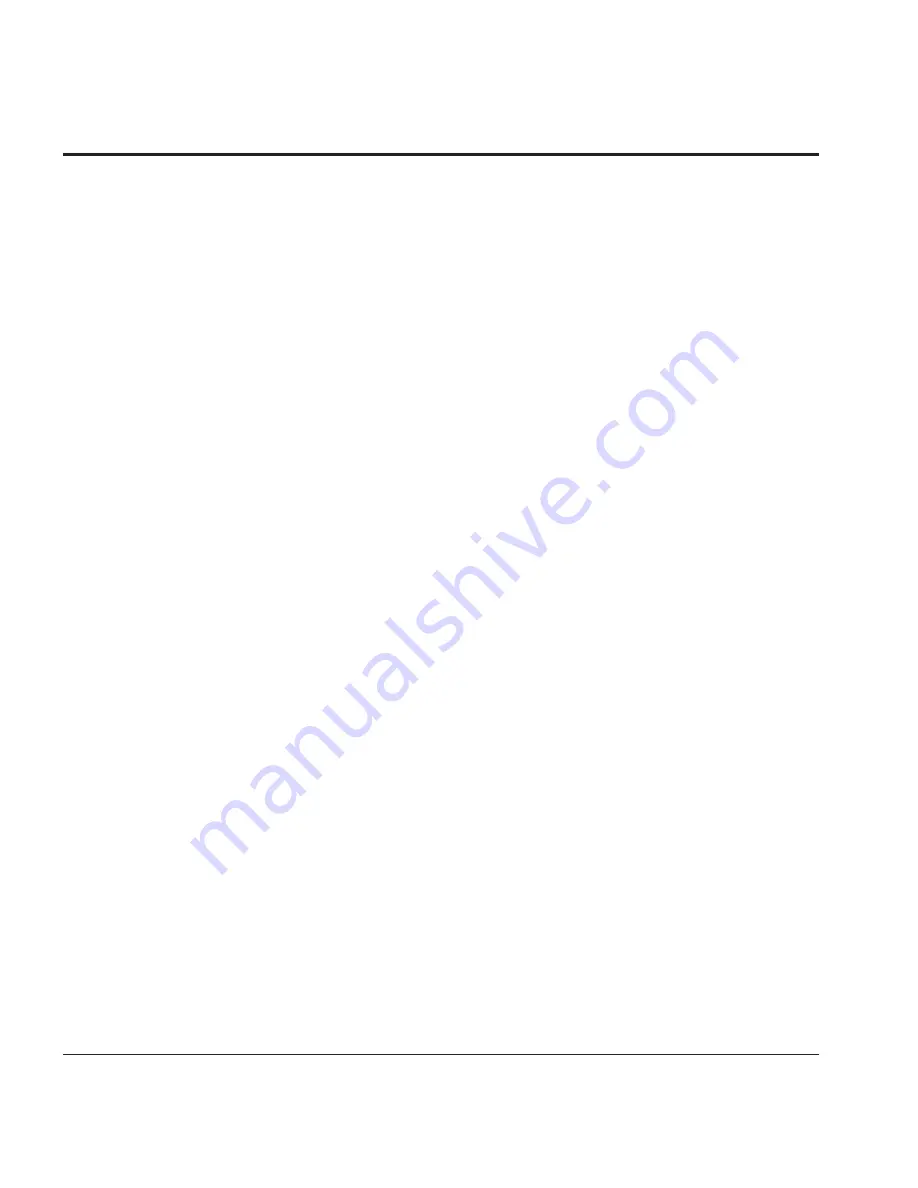
87
SPX advanced – description of parameters
SPX ADVANCED APPLICATION MANUAL
SVCH0203—October 2017 www.eaton.com
Code
ID
Parameter
Notes
P1.5.7.2
490
Digital output 2 function “DO2 content”
9 = “Reversed”
Drive output frequency is negative
10 = “JogSpeedSel”
The jogging, preset or inching speed has been activated with digital input.
11 = “At speed”
Induction motor: speed is within nominal slip of the reference.
PMS motor: output frequency is within 1 Hz of the reference.
12 = “MotorRegAct”
One of the limit regulators is active.
13 = “FreqLim1Sup”
Output frequency limit 1 supervision
The output frequency goes outside the set supervision low limit/high limit.
14 = “FreqLim2up”
Output frequency limit 2 supervision
The output frequency goes outside the set supervision low limit/high limit.
15 = “TorqLimSprv”
Torque limit supervision
The motor torque goes beyond the set supervision low limit/high.
16 = “RefLimSprv”
Reference limit supervision
Active reference goes beyond the set supervision low limit/high limit.
17 = “ExtBrakeCont”
External brake control
External brake ON/OFF control with programmable delay
18 = “I/O ContAct”
Control from I/O terminals
IO control place is active.
19 = “TempLimSprv”
Drive temperature limit supervision.
Drive temperature goes beyond the set supervision limits (par. ID354)
20 = “WrongDirecti”
Motor rotation direction is different from the requested one. This happens
in situation when an external force makes the motor to rotate into different
direction or when a command for direction change has been given and the drive
is still ramping down to change direction.
21 = “ExtBrakeInv”
External brake control inverted
External brake ON/OFF control; Output active when brake control is OFF.
22 = “ThermFlt/Wrn”
Thermistor fault or warning
The thermistor input of option board indicates overtemperature. Fault or warning
depending on the response parameter.
23 = “AI Supervis”
Analog input supervision
Analog input supervision function, Set Reset type output function.
24 = “FB DigInput1”
Fieldbus digital input data 1
25 = “FB DigInput2”
Fieldbus digital input data 2
26 = “FB DigInput3”
Fieldbus digital input data 3
27 = “Warning SR”
Warning indication that requires pressing of Reset button. Normally the drive
will remove warning indication when the fault situation has passed. This output
requires that reset button is pressed before signal goes low after there has been
a warning trigger. If a new warning comes while previous is active this output
goes low for 1 second.
28 = “ID.Bit”
Select the signal for controlling the DO. The parameter has to be set in format
xxxx.yy where xxxx is the ID number of a signal and yy is the bit number. For
example, the value for DO control is 1174.02. 1174 is the ID number of Warning
Word 1. So the digital output is ON when bit number 02 of the warning word (ID
no. 1174) i.e. Motor underload is high.