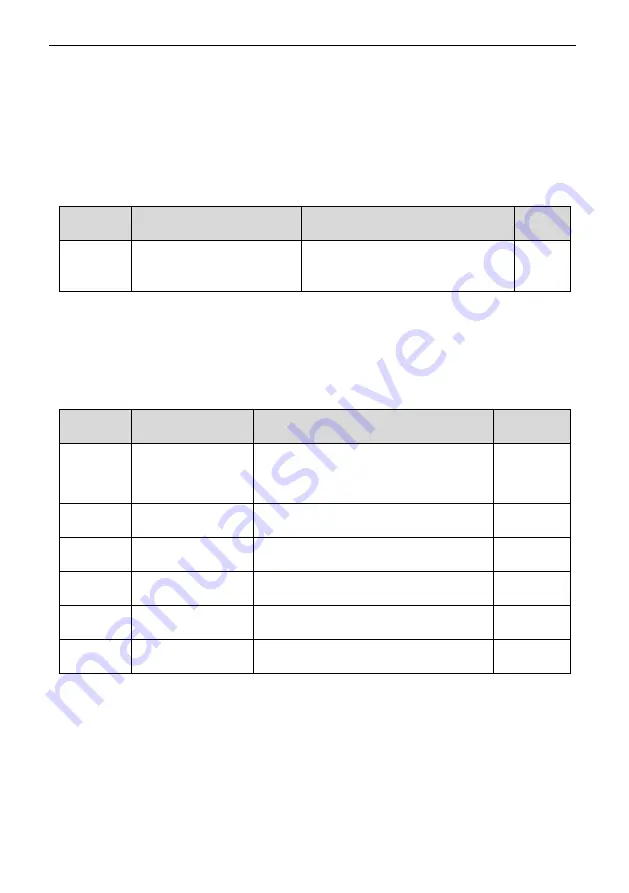
PE6000 User Manual Description of Function Codes
89
It is used to bind the three running command sources with the nine frequency sources,
facilitating to implement synchronous switchover.
For details on the frequency sources, see the description of P0-03 (Main frequency source X
selection). Different running command sources can be bound to the same frequency source
If a command source has a bound frequency source, the frequency source set in P0-03 to
P0-07 no longer takes effect when the command source is effective.
Function
Code
Parameter Name
Setting Range
Default
P0-28
Serial communication
protocol
0: Modbus protocol
1: PROFIBUS-DP bridge
2: CANopen bridge
0
The PE6000 supports Modbus, PROFIBUS-DP bridge and CANopen bridge. Select a proper
protocol based on the actual requirements.
Group P1: Motor Parameters
Function
Code
Parameter Name
Setting Range
Default
P1-00
Motor type
selection
0: Common asynchronous motor
1: Variable frequency asynchronous
motor 2: Permanent magnetic
synchronous motor
0
P1-01
Rated motor power
0.1–1000.0 kW
Model
dependent
P1-02
Rated motor
voltage
1–2000 V
Model
dependent
P1-03
Rated motor
current
0.01–
655.35 A (AC drive power ≤ 55 kW)
0.1–6553.5 A (AC drive power > 55 kW)
Model
dependent
P1-04
Rated motor
frequency
0.01 Hz to maximum frequency
Model
dependent
P1-05
Rated motor
rotational speed
1–65535
RPM
Model
dependent
Set the parameters according to the motor nameplate no matter whether V/F control or vector
control is adopted.
To achieve better V/F or vector control performance, motor auto-tuning is required. The motor
auto-tuning accuracy depends on the correct setting of motor nameplate parameters.