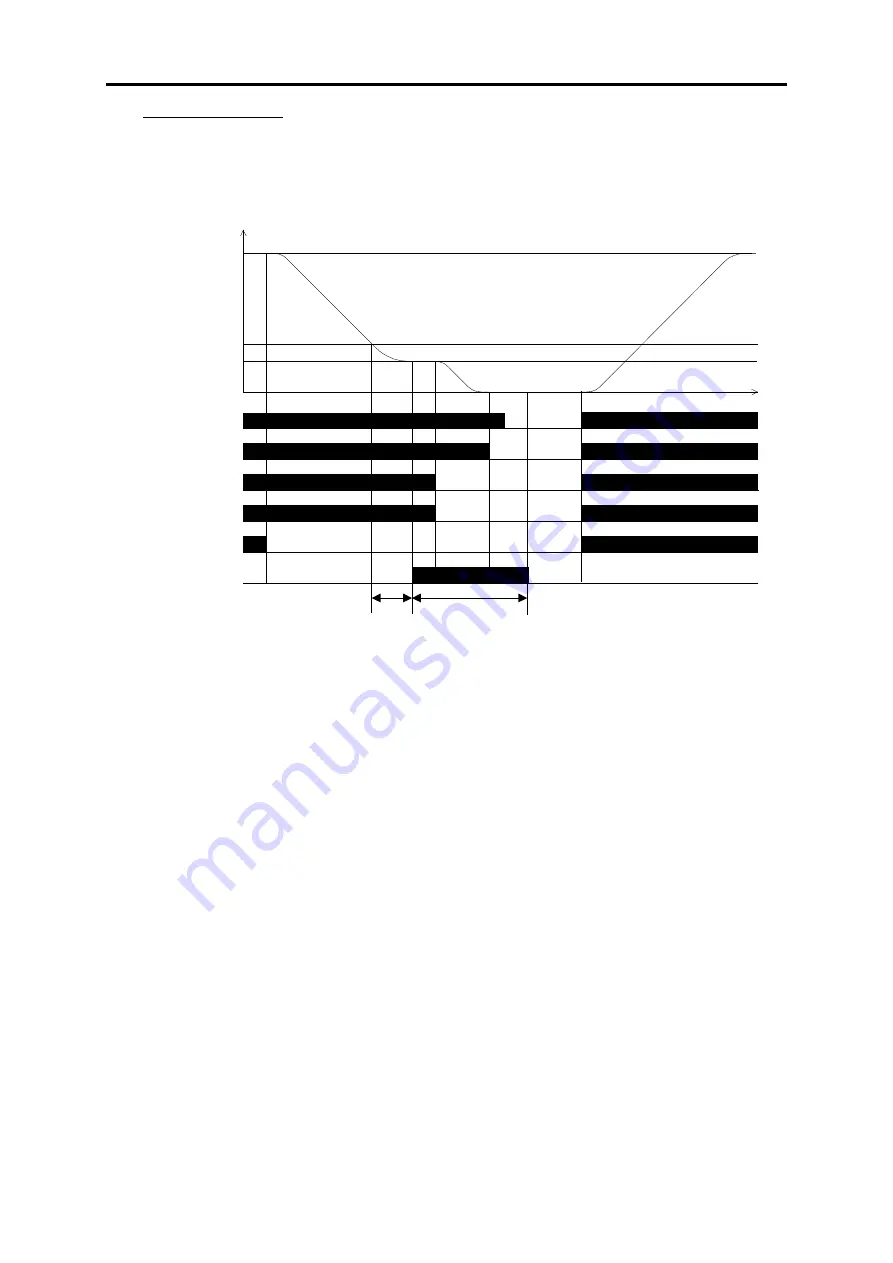
ii) When L99 bit6 is 1
After the timer of L89,
DOPEN
is turned off regardless to the state of
EN
terminal and
BX
terminal. When the terminal
BX
is turned on,
DOPEN
output signal operates as same as
EN
is
turned OFF.
High speed
Speed
ON
FWD
SS1
SS2
ON
ON
SS4
ON
Creep speed
Zero speed
Time
ON
EN
DOPEN
ON
L88
L89
ON
ON
ON
ON
ON
ON
Door open
starting speed
2-180
Summary of Contents for Frenic lift
Page 1: ...LM2A series Reference Manual INR SI47 1909a E...
Page 7: ......
Page 13: ......
Page 51: ...2 38...
Page 221: ......
Page 252: ......
Page 254: ...URL http www fujielectric com...