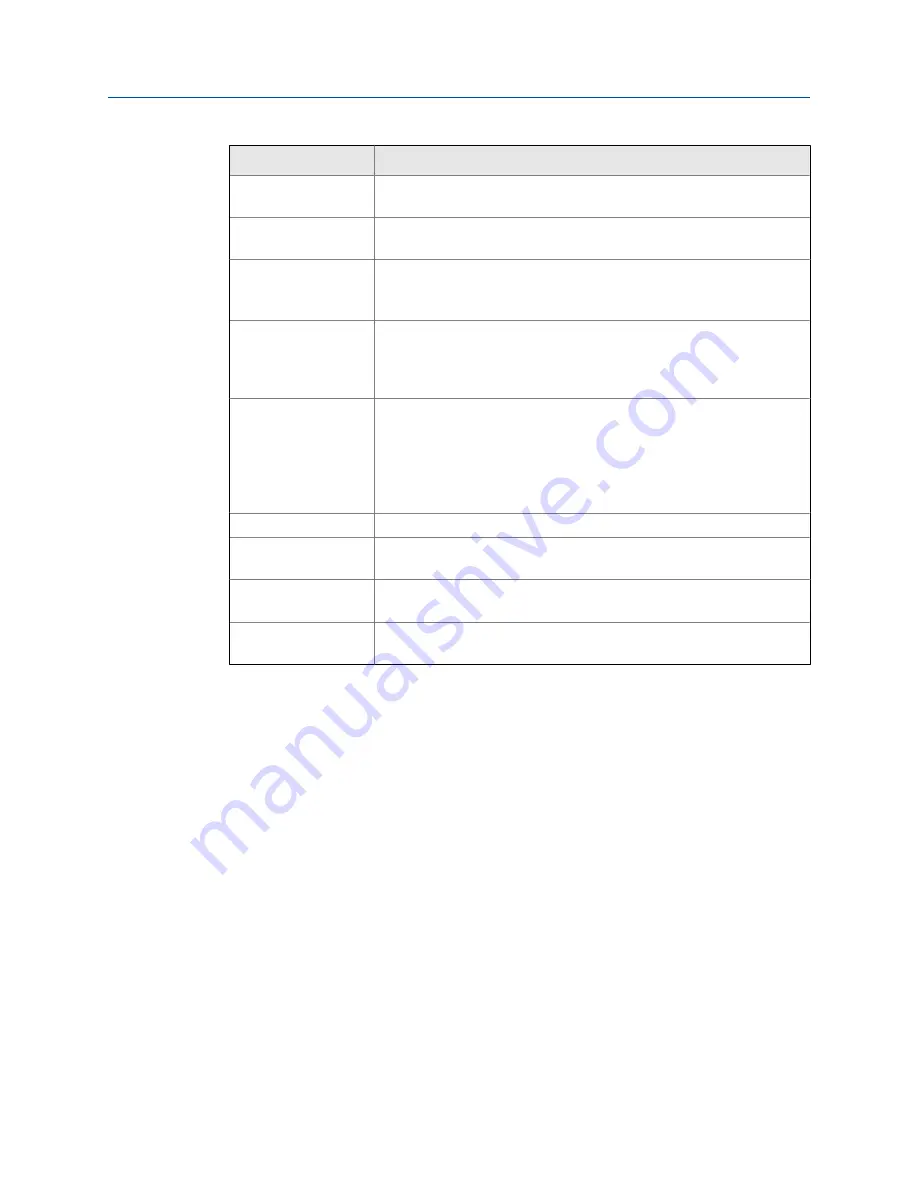
Term
Definition
Field Zero
The zero value obtained by performing a zero calibration outside the fac-
tory.
Prior Zero
The zero value stored in the transmitter at the time a field zero calibration
is begun. May be the factory zero or a previous field zero.
Manual Zero
The zero value stored in the transmitter, typically obtained from a zero
calibration procedure. It may also be configured manually. Also called
“mechanical zero” or “stored zero”.
Live Zero
The real-time bidirectional mass flow rate with no flow damping or mass
flow cutoff applied. An adaptive damping value is applied only when the
mass flow rate changes dramatically over a very short interval. Unit = con-
figured mass flow measurement unit.
Zero Stability
A laboratory-derived value used to calculate the expected accuracy for a
sensor. Under laboratory conditions at zero flow, the average flow rate is
expected to fall within the range defined by the Zero Stability value (0 ±
Zero Stability). Each sensor size and model has a unique Zero Stability val-
ue. Statistically, 95% of all data points should fall within the range defined
by the Zero Stability value.
Zero Calibration
The procedure used to determine the zero value.
Zero Time
The time period over which the Zero Calibration procedure is performed.
Unit = seconds.
Field Verification Zero
A 3-minute running average of the Live Zero value, calculated by the
transmitter. Unit = configured mass flow measurement unit.
Zero Verification
A procedure used to evaluate the stored zero and determine whether or
not a field zero can improve measurement accuracy.
Quick start
Configuration and Use Manual
9
Summary of Contents for Micro Motion 2500
Page 8: ...Contents vi Micro Motion Model 2500 Transmitters with Configurable Input Outputs ...
Page 10: ...Getting started 2 Micro Motion Model 2500 Transmitters with Configurable Input Outputs ...
Page 18: ...Quick start 10 Micro Motion Model 2500 Transmitters with Configurable Input Outputs ...
Page 237: ...NE 53 history Configuration and Use Manual 229 ...