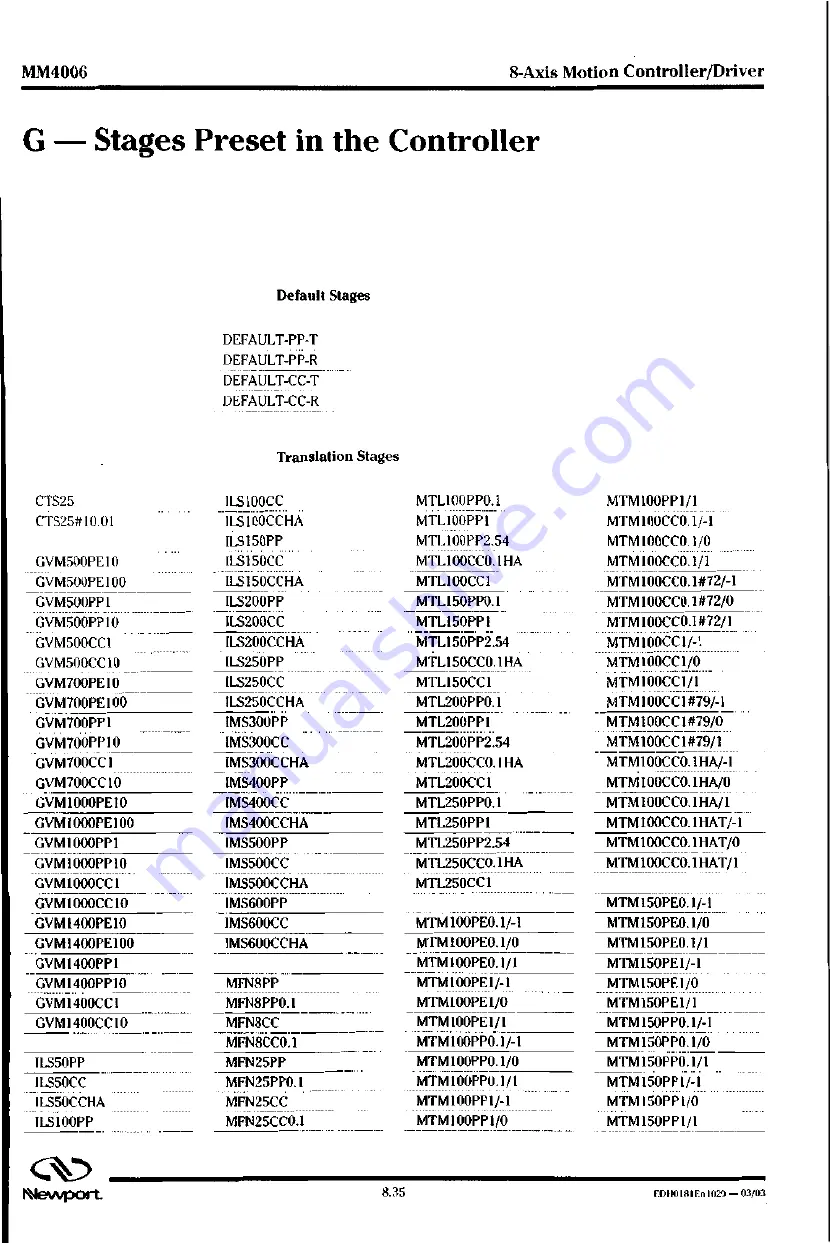
MM4006
8
-Axis Motion Controller/Driver
Translation Stages
CTS25
ILS100CC
MTL1OOPP0.1
MTM 10OPP1/1
CTS25#10.01
ILS100CCHA
MTL100PP1
MTM100CCO.1/-1
ILS15OPP
MT1,100PP2.54
MTM100CCO.1/0
GVM500PE10
ILS150CC
MTL100CCO.1HA
MTM100CCO.1/1
GVM500PE100
ILS150CCHA
MTL100CC1
MTM 100CC0.1#72/-1
GVM5OOPP1
ILS200PP
MTL15OPP0.1
MTMIOOCC0.1#72/0
GVM500PP10
ILS200CC
MTL150PP I
MTM100CCO.1#72/ I
GVM500CC1
ILS200CCHA
MTL150PP2.54
MTMIOOCC1/-1
GVM500CCI0
ILS250PP
MTL150CCO.1HA
MTM100CC1/0
GVM700PE10
ILS250CC
MTL150CCI
MTM1OOCC1/1
GVM700PE100
ILS250CCHA
MTL200PP0.1
MTM1OOCCI#79/-1
GVM7OOPPI
IMS300PP
MTL2OOPP1
MTM100CC1#79/0
GVM7OOPP10
IMS300CC
MTL200PP2.54
MTM1OOCCI#79/1
GVM700CC1
IMS300CCHA
MTL200CCO. I HA
MTM100CCO.1HA/-1
GVM700CC 10
IMS400PP
MTL200CC1
MTM100CCO.1HA/0
GVM1000PE10
IMS400CC
MTL25OPPO.1
MTMIOOCC0.1HA/1
GVM1000PE100
IMS400CCHA
MTL25OPP1
MTM100CCOAHAT/-1
GVM100OPP1
IMS500PP
MTL25OPP2.54
MTM100CCOAHAT/0
GVM1000PP10
IMS500CC
MTL250CCO.1HA
MTM100CCOAHAT/1
GVM1000CC1
IMS500CCHA
MTL250CC1
GVM1000CC10
IMS600PP
MTMI5OPE0.1/-1
GVM1400PE10
IMS600CC
MTM100PEO.1/-1
MTM150PE0.1/0
GVM1400PE100
IMS600CCHA
MTM100PEO.1/0
MTM150PE0.1/1
GVM140OPP1
MTM100PEO.1/1
MTMI5OPE1/-1
GVM1400PP10
MFN8PP
MTM100PE1/-1
MTM150PE1/0
GVM1400CCI
MFN8PP0.1
MTM100PE1/0
MTM150PE1/1
GVM1400CC10
MFN8CC
MTM100PE1/1
MTMI5OPP0.1/-1
MFN8CC0.1
MTMIOOPP0.1/-1
MTM15OPP0.1/0
ILS50PP
MFN25PP
MTMlOOPPO.1/0
MTM15OPP0.1/1
ILS50CC
MFN25PP0.1
MTM 1 OOPP0.1/1
MTMI5OPP1/-1
ILS50CCHA
MFN25CC
MTMlOOPPI/-1
MTM15OPP1/0
11510OPP
MFN2SCC0.1
MTM1OOPP1/0
MTM15OPP1/1
G S t a g e s Preset in the Controller
Default Stages
DEFAULT-PP-T
DEFAULT-PP-R
DEFAULT-CC-T
DEFAULT-CC-R
( )
N e v v p O r t .
8
.
3
5
El-M0181E01020 - 03/03
Содержание MM4006
Страница 9: ...F D110181En1020 03 03 b J e w p o r t...
Страница 10: ...Section 1 Introduction 4 4 G G 4 4 4 4 M u d Com 4k 4 66i1W406 i i r i A 0 8 y 0 9 0 0 i 0 0 40 0 4 cv Newport...
Страница 11: ...MM4006 8 Axis Motion Controller Driver evvport...
Страница 41: ...MM4006 Introduction FPI 111181Eli11120 0 1 03 1 3O tNevvport...
Страница 42: ...Section 2 Local Mode C Newport...
Страница 43: ...MM4006 8 Axis Motion Controller Driver C N e w p o r t...
Страница 96: ...Section 3 Remote Mode C klevvport...
Страница 97: ...Newport...
Страница 310: ...Section 4 Motion Control Tutorial Ilevvport...
Страница 311: ...MM4006 8 Axis Motion Controller Driver C EDI10181En 1020 03 03 2 N e V V p O r t...
Страница 313: ...MM4006 8 Axis Motion Controller Driver cv ED110181E01020 03 03 4 2 M e v v p o r t...
Страница 334: ...Section 5 Trajectory Functions Tutorial Newport...
Страница 335: ...MM4006 8 Axis Motion Controller Driver C Newport...
Страница 337: ...MM4006 8 Axis Motion Controller Driver EDH0181En1020 03 03 5 2 N e w p o r t...
Страница 346: ...Section 6 Feature Descriptions Tutorial Newport...
Страница 347: ...MM4006 8 Axis Motion Controller Driver C Nevvport...
Страница 349: ...MM4006 8 Axis Motion Controller Driver ED11018lEn I 020 03 03 6 2 N e v v p O r t...
Страница 359: ...MM4006 F e a t u r e Descriptions Tutorial cv EDI10181En1020 03 03 6 12 N e w p o r t...
Страница 360: ...Section 7 Servo Tuning rano at 1 2 2 p EOF 110 1 0 0 0 0 0 ill fpL4 cv Newport...
Страница 361: ...MM4006 8 Axis Motion Controller Driver C Nevvport...
Страница 363: ...MM4006 8 Axis Motion Controller Driver EDH0181En 1020 03 03 7 2...
Страница 368: ...Section 8 Appendices INevvport...
Страница 369: ...MM4006 8 Axis Motion Controller Driver CkJ Newport...
Страница 371: ...MM4006 8 Axis Motion Controller Driver EDI10181EnI020 03 03 8 2 N e v v p o r t...
Страница 410: ...A7 h7s z c 7...