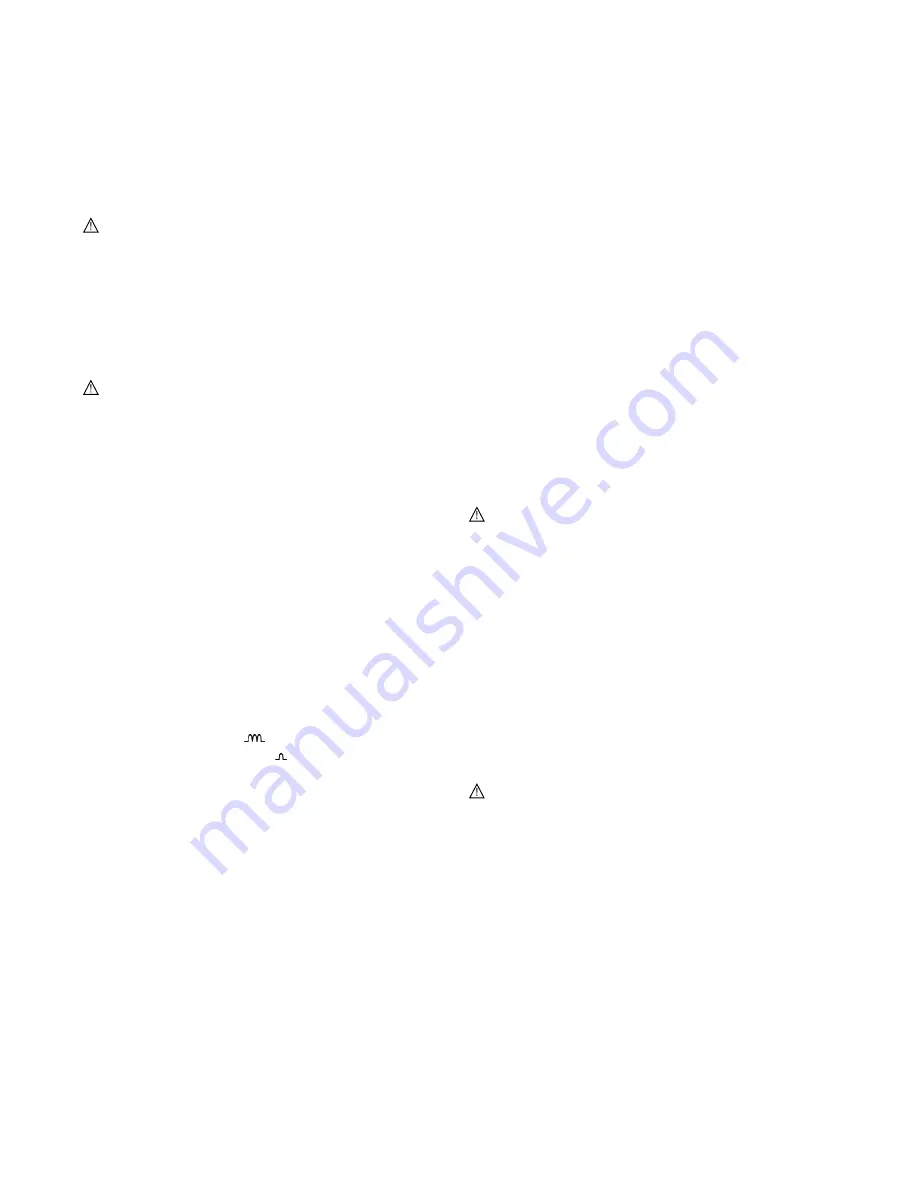
- Release the pressure counter-roller(s) and move them away from the lower
NOTE: during welding the display will show the actual value of the current.
roller(s)
(2a)
;
- It is possible to modify the wire feed rate by adjusting the spool gun potentiometer,
and the display will instantly show the corresponding value; the current reading will
- Make sure that the towing roller(s) is suited to the wire used
(2b)
.
re-appear as soon as the adjustment has been completed.
- Free the end of the wire and remove the distorted end with a clean cut and no burr;
- Under critical welding conditions, the wire diameter LED will flash.
turn the reel anti-clockwise and thread the end of the wire into the wire-guide infeed,
Important:
for each position of the switch, the welding machine stores all the
pushing it 50-100mm into the wire guide of the torch fitting
(2c)
.
parameters for the last welding job to be carried out (material, gas, wire diameter, wire
- Re-position the counter-roller(s), adjusting the pressure to an intermediate value,
feed rate).
and make sure that the wire is correctly positioned in the groove of the lower roller(s)
(3)
- Use the adjustment screw located at the centre of the spindle to apply a slight
braking pressure on the spindle itself
(1b)
.
- Remove the nozzle and contact tip
(4a)
.
- Insert the welding machine plug in the power supply outlet, switch on the welding
machine, press the torch button and wait for the end of the wire to pass through the
whole of the wire guide hose and protrude by 10-15 cm from the front part of the
torch, release the button.
__________________________________________________________________
WARNING! During these operations the wire is live and subject to
mechanical stress; therefore if adequate precautions are not taken the wire
could cause hazardous electric shock, injury and striking of electric arcs:
__________________________________________________________________
- Do not direct the mouthpiece of the torch towards parts of the body.
- Keep the torch away from the gas bottle.
- Re-fit the contact tip and the nozzle onto the torch
(4b)
.
- Check that wire feed is regular; set the roller and spindle braking pressure to the
minimum possible values making sure that the wire does not slide in the groove and
when feed is halted the loops of wire are not loosened by excessive reel inertia.
- Cut the end of the wire so that 10-15 mm protrude from the nozzle.
- Close the reel compartment door.
5.7 LOADING THE WIRE REEL ONTO THE SPOOL GUN
__________________________________________________________________
WARNING! BEFORE STARTING THE OPERATIONS TO LOAD THE WIRE
MAKE SURE THE WELDING MACHINE IS SWITCHED OFF AND DISCONNECTED
FROM THE MAIN POWER SUPPLY OR THAT THE SPOOL GUN IS
DISCONNECTED FROM THE WELDING MACHINE.
__________________________________________________________________
Fig. I
MAKE SURE THE WIRE PULLER ROLLERS, THE WIRE GUIDE HOSE AND THE
SPOOL GUN CONTACT TUBE HAVE SUITABLE DIAMETERS CORRESPONDING
TO THAT OF THE WIRE TO BE USED AND MAKE SURE THEY ARE ASSEMBLED
CORRECTLY. DO NOT WEAR PROTECTIVE GLOVES WHEN THREADING IN THE
WIRE.
-
Remove the cover by undoing the appropriate screw
(1)
.
-
Position the wire reel on the reel holder.
-
Free the pressure counter-roller and move it away from the lower roller
(2)
.
-
Free the end of the wire, cut off the distorted end with a clean cut leaving no burrs;
turn the reel anti-clockwise and thread the end of the wire into the wire-guide infeed,
pushing it 50-100mm inside the lance
(2)
.
-
Reposition the counter-roller, adjusting the pressure to an intermediate value and
make sure the wire is correctly positioned in the lower roller recess
(3)
.
-
Brake the reel holder slightly by adjusting the appropriate screw.
-
Switch on the welding machine, putting the switch to ( I ), press the spool gun button
and wait until the end of the wire runs through the complete wire guide hose and 10-
15 cm comes out of the front of the torch then release the torch button.
-
With the Spool gun connected, switch on the machine, press the spool gun button
and wait for the end of the wire to pass completely through the wire guide hose and
for 10-15 cm to come out of the front of the torch, release the torch button.
6. WELDING: DESCRIPTION OF THE PROCEDURE
- Only for the 3-phase version:
Insert the earth outlet in the desired quick (-) connector, depending on the material to
be welded
Fig. G1-L
- quick connector (-) with max. (
) reactance for aluminium material and
derivative alloys (Al), copper alloys (CuAl/CuSi).
- quick connector (-) with min. reactance (
) for stainless steel (SS), carbon steel
and low alloys (Fe).
- Connect the return cable to the piece being welded.
- Turn on and adjust the protective gas using the pressure reducing valve (5-7 l/min)
NOTE:
At the end of the job, remember to turn off the protective gas.
6.1 WELDING WITH THE MIG TORCH (Fig. B, C)
- Switch on the welding machine,
- Select the type of material, the type of gas and the wire diameter by pressing buttons
12,11,10
respectively.
- Set the welding current by means of the switch and rotary switch (if present)
(Fig.M)
.
- The display will show the welding current corresponding to the setting that has just
been made. Pressing button
6
will show the corresponding factory setting for the wire
feed rate (LED
8
DEFAULT on).
NOTE: ensure good welding results can be ensured by varying the wire feed rate
within a preset interval. This interval is indicated by LED
8
DEFAULT lighting up;
outside the DEFAULT interval the LED will go off.
- Select the welding mode by pressing button
9
.
- Press the torch button to start welding.
NOTE: during welding the display will show the actual value of the current.
- Wire feed rate can be modified by turning knob (7), and the display will instantly show
the corresponding value; the current reading will re-appear as soon as the
adjustment has been completed.
Important:
for each position of the switch, the welding machine will store all the
parameters for the last welding job to be carried out (material, gas, wire diameter, wire
feed rate).
6.2 WELDING WITH THE SPOOL GUN (Fig. B,C)
- Switch on the welding machine,
- Select the type of material, the type of gas and the wire diameter by pressing buttons
12,11,10
respectively.
- Set the welding current by means of the switch and rotary switch (if present)
(Fig.M)
.
- The display will show the welding current corresponding to the setting that has just
been made. Pressing button
6
will show the corresponding factory setting for the wire
feed rate (LED
8
DEFAULT on).
NOTE: ensure good welding results can be ensured by varying the wire feed rate
within a preset interval. This interval is indicated by LED
8
DEFAULT lighting up;
outside the DEFAULT interval the LED will go off.
- Select the welding mode by pressing button
9
.
- Press the torch button to start welding.
6.3 SPOT WELDING OPERATION (Fig. C)
- Set spot welding operation by pressing button
9.
- Press button
6
until LED
5
lights up. Use knob
7
to set spot duration.
- Press the torch or spool gun button and start welding. It will stop automatically after
the pre-set time.
- See also
Fig. N
for directions relating to the procedure.
6.4 OVERLOAD PROTECTION (Fig. C)
The thermostatic protection LED
1
lights up when there is overheating (also, the
display shows the message
ALL thr
) and cuts off the power supply; the system is reset
automatically after a few minutes' cooling.
6.5 PROGRAMMING THE WELDING PARAMETERS (Fig. C)
The DEFAULT values for the accessory welding parameters (slope up, burn-back time,
pre-gas time) are preset by the manufacturer; to customise each parameter proceed
as follows:
- Press button
6
for at least 3 seconds until the message “nor” appears on the display.
- Press button
6
until the LED (
3 or 4 or 5
) lights up for the corresponding accessory
parameter to be programmed.
- Turn knob
7
to modify the value of the selected parameter.
Wire feed rate slope up:
Adjustment range nor, r_1, ..., r_9 (nor = start without slope, r_1 = very quick start,
r_9 = very slow start).
Burn-back time:
Adjustment range 0-1sec.
Post-gas time:
Adjustment range 0-3sec.
- To restore the factory (default) setting press buttons
9
and
10
simultaneously for 3
seconds.
- To store the defined value and exit programming mode, press button
6
again for at
least 3 seconds.
6.6 RESETTING ALL PARAMETERS TO THE DEFAULT VALUES (Fig. C)
Pressing buttons
9
and
10
simultaneously (not in programming mode) will restore all
welding parameters to their default values.
7. MAINTENANCE
__________________________________________________________________
WARNING! BEFORE CARRYING OUT MAINTENANCE OPERATIONS MAKE
SURE THE WELDING MACHINE IS SWITCHED OFF AND DISCONNECTED FROM
THE MAIN POWER SUPPLY.
__________________________________________________________________
7.1 ROUTINE MAINTENANCE:
ROUTINE MAINTENANCE OPERATIONS CAN BE CARRIED OUT BY THE
OPERATOR.
7.1.1 Torch
-
Do not put the torch or its cable on hot pieces; this would cause the insulating
materials to melt, making the torch unusable after a very short time;
-
Make regular checks on the gas pipe and connector seals;
-
Every time the wire reel is changed, blow out the wire-guide hose using dry
compressed air (max. 5 bar) to make sure it is not damaged;
-
Before every use, check the wear and correct assembly of the parts at the end of the
torch: nozzle, contact tip, gas diffuser.
7.1.2 Wire feeder
-
Make frequent checks on the state of wear of the wire feeder rollers, regularly
remove the metal dust deposited in the feeder area (rollers and wire-guide infeed
and outfeed).
7.2 EXTRAORDINARY MAINTENANCE:
EXTRAORDINARY MAINTENANCE OPERATIONS SHOULD BE CARRIED OUT
ONLY AND EXCLUSIVELY BY SKILLED OR AUTHORISED ELECTRICAL-
MECHANICAL TECHNICIANS.
__________________________________________________________________
WARNING! BEFORE REMOVING THE WELDING MACHINE PANELS AND
WORKING INSIDE THE MACHINE MAKE SURE THE WELDING MACHINE IS
SWITCHED OFF AND DISCONNECTED FROM THE MAIN POWER SUPPLY
OUTLET.
If checks are made inside the welding machine while it is live, this may cause
serious electric shock due to direct contact with live parts and/or injury due to
direct contact with moving parts.
__________________________________________________________________
- Inspect the welding machine regularly, with a frequency depending on use and the
dustiness of the environment, and remove the dust deposited on the transformer,
reactance and rectifier using a jet of dry compressed air (max. 10 bar).
- Do not direct the jet of compressed air on the electronic boards; these can be
cleaned with a very soft brush or suitable solvents.
- At the same time make sure the electrical connections are tight and check the wiring
for damage to the insulation.
- At the end of these operations re-assemble the panels of the welding machine and
screw the fastening screws right down.
- Never, ever carry out welding operations while the welding machine is open.
- 6 -