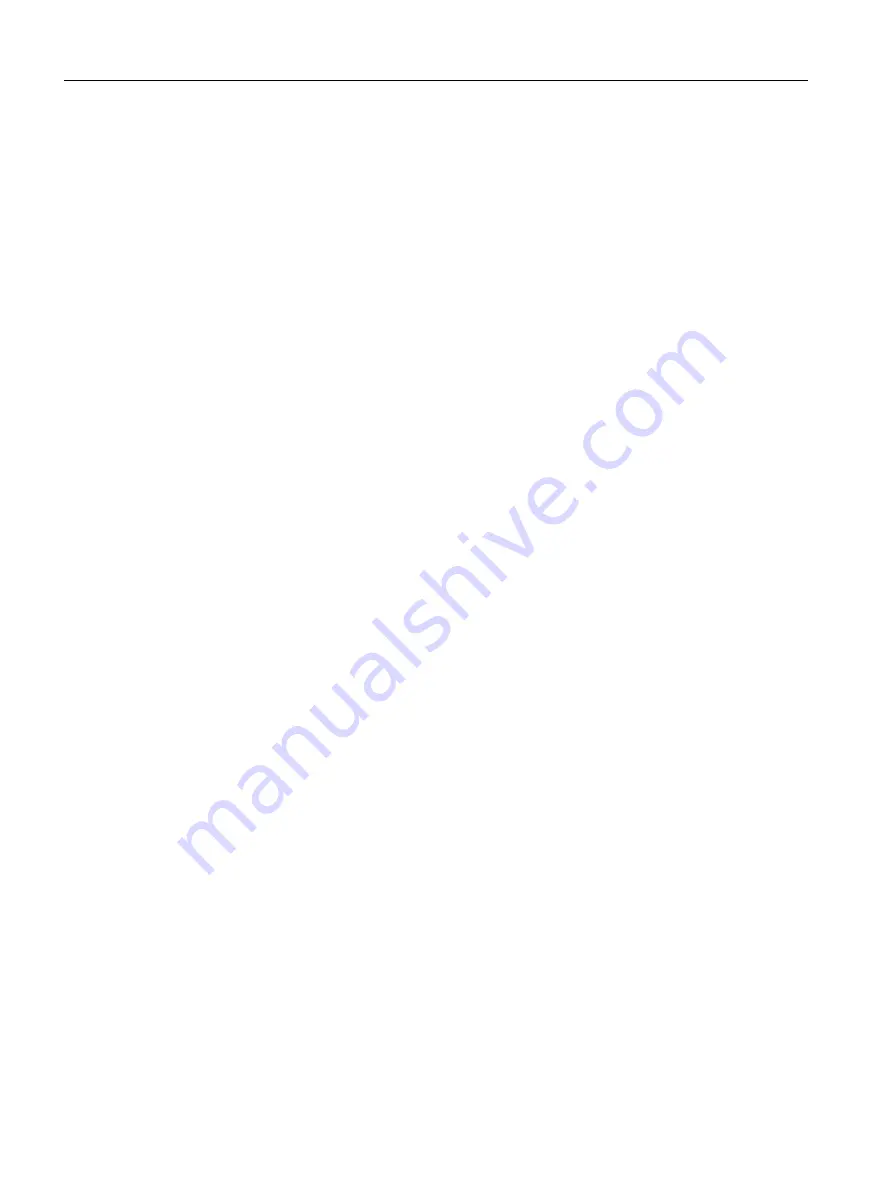
S1: Spindles
16.4 Configurable gear adaptation
Basic Functions
1312
Function Manual, 09/2011, 6FC5397-0BP40-2BA0
Functionality
Machine tools of conventional design require a gear step change of the spindle in oscillation mode.
If the machine data configuration is:
MD35010 $MA_GEAR_STEP_CHANGE_ENABLE = 1
the following sequence is implemented:
• Deceleration of the spindle.
The braking action corresponds to an M5 movement.
• Output of VDI interface signals:
DB31, ... DBX84.6 (Oscillation mode)
DB31, ... DBX82.3 (Change gear)
DB31, ... DBX82.0-82.2 (Set gear step A to C).
If position control has been enabled, it is disabled:
DB31, ... DBX61.5 = 0.
• The load gearbox can now "disengage".
• NC/PLC IS:
DB31, ... DBX18.5 (Oscillation enable)
can be set by the PLC.
The spindle motor then performs an oscillation motion with preset values.
The oscillation motion is designed to facilitate and accelerate the reengaging of the gear wheels.
• Writing of NC/PLC IS:
DB31, ... DBX16.0-16.2 (Actual gear step A to C)
by the PLC.
• Once the PLC has sent:
DB31, ... DBX16.3 (Gear changed)
to the NCK, the last movement to be active is continued, if available.
For indirect encoders (motor encoders), the homing status is cleared:
DB31, ... DBX60.4/5 = 0.
Block change
If the spindle is switched to oscillation mode
with NC/PLC IS:
DB31, ... DBX82.3 (Change gear)
, the processing of the part program remains suspended.
A new block is not executed.
If oscillation mode is terminated with NC/PLC IS:
DB31, ... DBX16.3 (Gear changed)
, the processing of the part program is resumed.
A new block is executed.