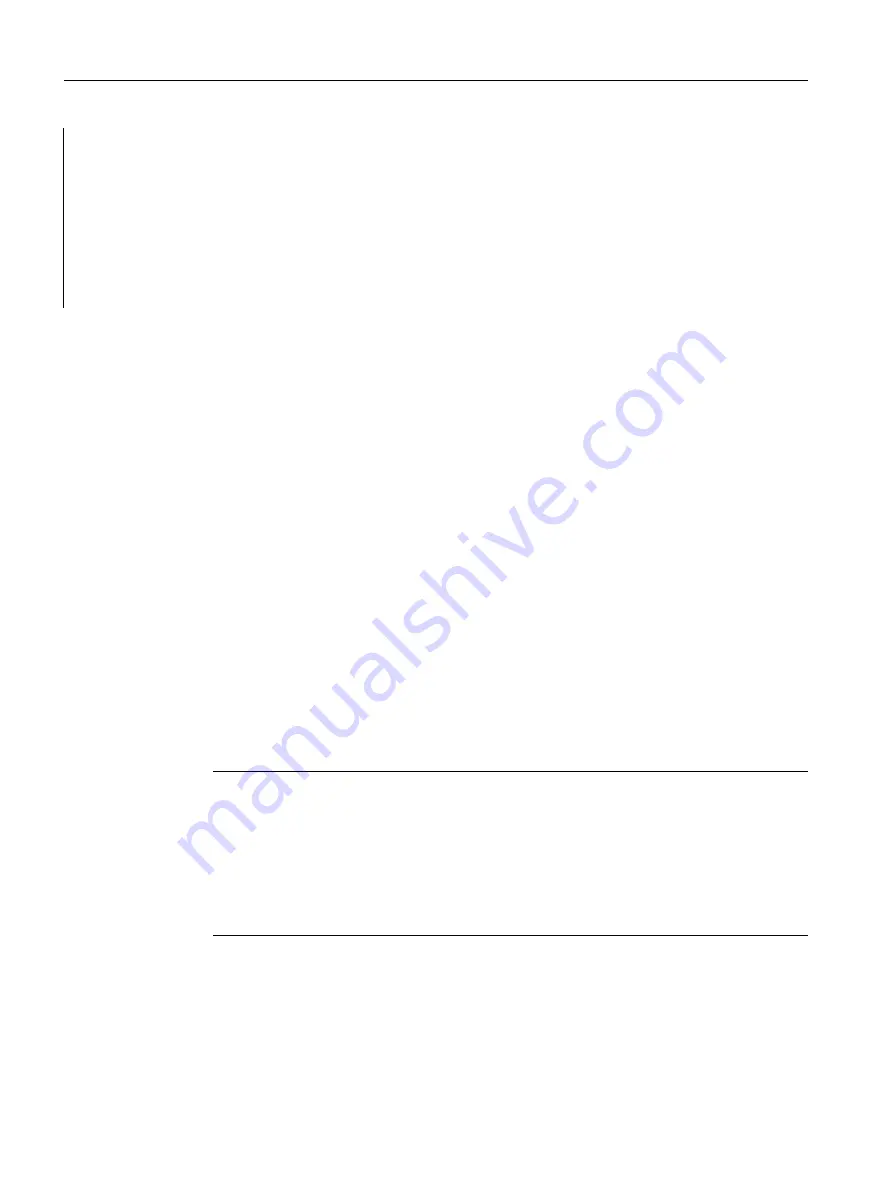
K1: Mode group, channel, program operation, reset response
9.8 Block search Type 5 SERUPRO
Basic Functions
540
Function Manual, 09/2011, 6FC5397-0BP40-2BA0
In both of the programs PROC L6 and PROC ASUPWZV2, the tool change is programmed with M206 instead of
M6.
ASUB program "ASUPWZV2" uses different system variables to detect the progress of the program
($P_TOOLNO) and represent the current status of the machine ($TC_MPP6[9998,1] ).
Spindle ramp-up
When the SERUPRO ASUB is started, the spindle is not accelerated to the speed specified in the program
because the SERUPRO ASUB is intended to move the new tool into the correct position at the workpiece after
the tool change.
A spindle rampup is performed with SERUPRO ASUB as follows:
• SERUPRO operation has finished completely.
• The user starts the SERUPRO ASUB via function block FC 9
in order to ramp up the spindle.
• The start after M0 in the ASUB does not change the spindle status.
• SERUPRO ASUB automatically stops before the REPOS part program block.
• The user presses START.
• The spindle accelerates to the target block state if the spindle was not programmed differently in the ASUB.
N1085 ASUP_ENDE1:
;
N1090 IF TNR_VORWAHL == TNR_SUCHLAUF GOTOF
ASUP_ENDE
;
N1100 T = $TC_TP2[TNR_VORWAHL]
;
Restore T preselection by tool name
;
N1110 ASUP_ENDE:
;
N1110 M90
;
Feedback to PLC
N1120 REPOSA
;
;ASUB end
Note
Modifications for REPOS of spindles:
The transitions of speed control mode and positioning mode must be taken into
consideration in the event of modifications in SERUPRO approach and spindle
functionality.
For further information about operating mode switchover of spindles, see
References: /FB1/ Function Manual, Basic Functions; Spindles (S1), 2.1 Spindle Modes.