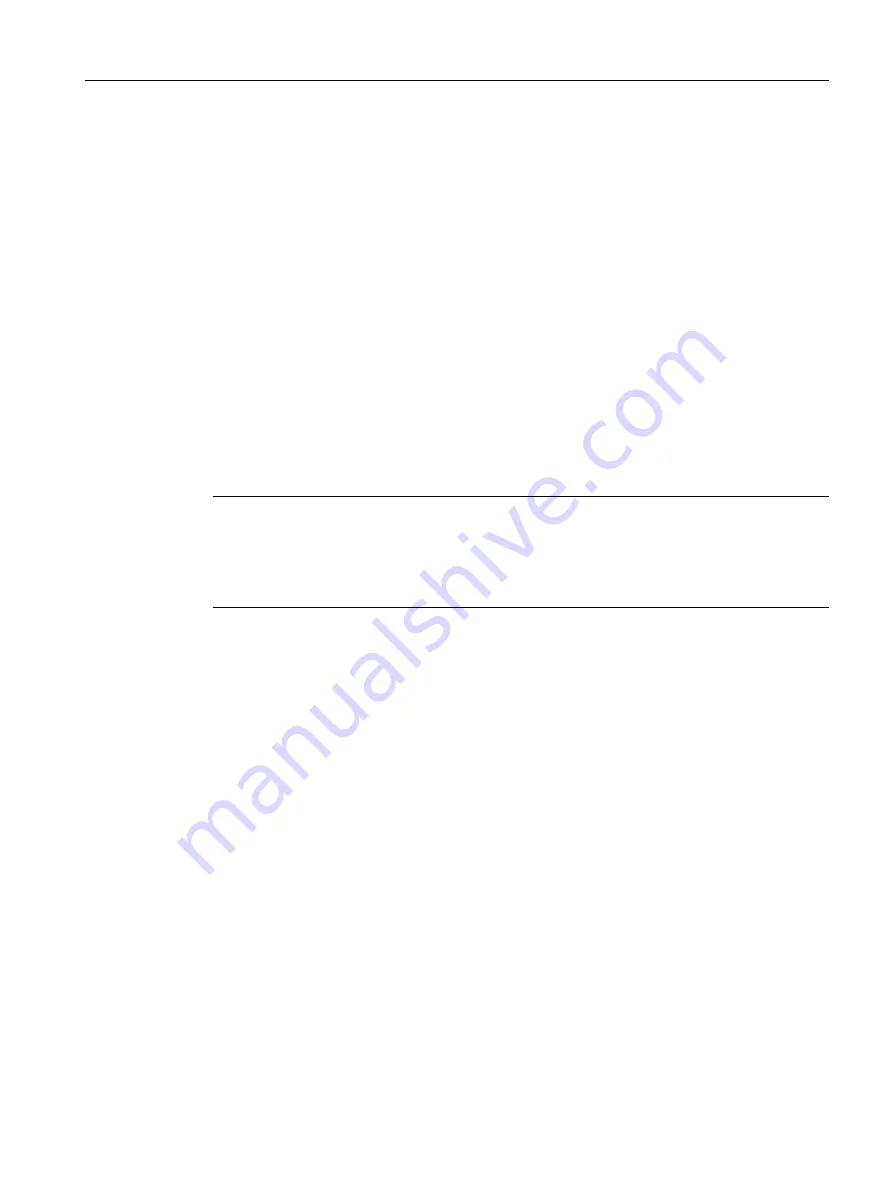
R1: Reference point approach
15.9 Referencing with absolute value encoders
Basic Functions
Function Manual, 09/2011, 6FC5397-0BP40-2BA0
1245
15.9.8
Automatic encoder replacement detection
Function
Automatic encoder replacement detection is required for absolute encoders in order to detect if the encoder has
been replaced and therefore needs to be readjusted.
The NC reads the encoder-specific serial number of the encoder from the drive every time the control is powered
up. If the serial number has changed the NC resets the encoder status to "Encoder not calibrated".
MD34210 $MA_ENC_REFP_STATE = 0
The status of the measuring system is indicated as "Not referenced":
DB31, ... DBB60.4 / 60.5 (referenced/synchronized 1/2) = 0
Serial number display
The NC stores the serial numbers read in the build-up specific to the machine in the machine data:
MD34230 $MA_ENC_SERIAL_NUMBER (encoder serial number)
Avoiding readjustments
In some special cases, for example, when a machine axis (built-on rotary axes) is removed and then mounted
again, readjustment is not necessary / desirable.
To avoid readjustment, zero must be parameterized as a serial number to be ignored for the measuring system of
the machine axis in question.
MD34232 $MA_EVERY_ENC_SERIAL_NUMBER = 0
If the NC now reads zero as the serial number, the encoder status is not reset and the serial number indicated in
the machine data is kept.
Note
Currently, only the serial numbers of absolute encoders with an EnDat interface can be read.
For all other encoders the display shows that no serial number has been read.
Automatic encoder replacement detection can therefore only be used with the specified
encoder types.