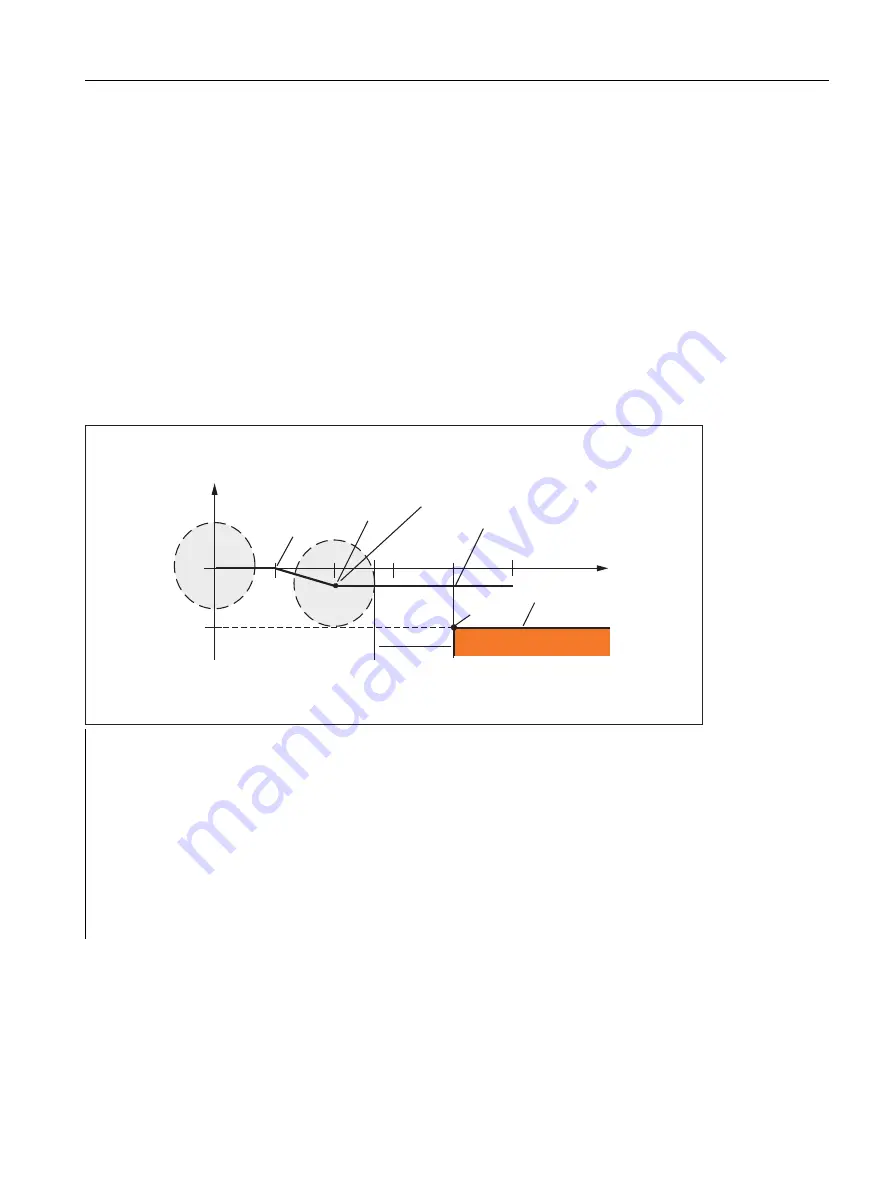
W1: Tool offset
18.5 Tool radius compensation 2D (TRC)
Basic Functions
Function Manual, 09/2011, 6FC5397-0BP40-2BA0
1469
Programming the end point P
4
(or P
0
for retraction) generally with X... Y... Z...
Possible ways of programming the end point P
4
for approach
End point P
4
can be programmed in the actual SAR block.
P
4
can be determined by the end point of the next traversing block.
Further blocks (dummy blocks) can be inserted between the SAR block and the next traversing block without
moving the geometry axes.
The end point is deemed to have been programmed in the actual SAR block for approach if at least one
geometry axis is programmed on the machining plane (X or Y with
G17
). If only the position of the axis
perpendicular to the machining plane (Z with
G17
) is programmed in the SAR block, this component is taken from
the SAR block, but the position in the plane is taken from the following block. In this case, an alarm is output if the
axis perpendicular to the machining plane is also programmed in the following block.
Example:
$TC_DP1[1,1]=120
; Milling tool T1/D1
$TC_DP6[1,1]=7
; Tool with 7 mm radius
N10 G90 G0 X0 Y0 Z30 D1 T1
N20 X10
N30 G41 G147 DISCL=3 DISR=13 Z=0 F1000
N40 G1 X40 Y-10
N50 G1 X50
...
...
N30
/
N40
can be replaced by:
N30 G41 G147 DISCL=3 DISR=13 X40 Y-10 Z0 F1000
or:
N30 G41 G147 DISCL=3 DISR=13 F1000
N40 G1 X40 Y-10 Z0
&RQWRXU
0DFKLQLQJXSWRWKLV
SRLQWZLWK*WKHQZLWK
*)
]
=
=
',65
;
3
<