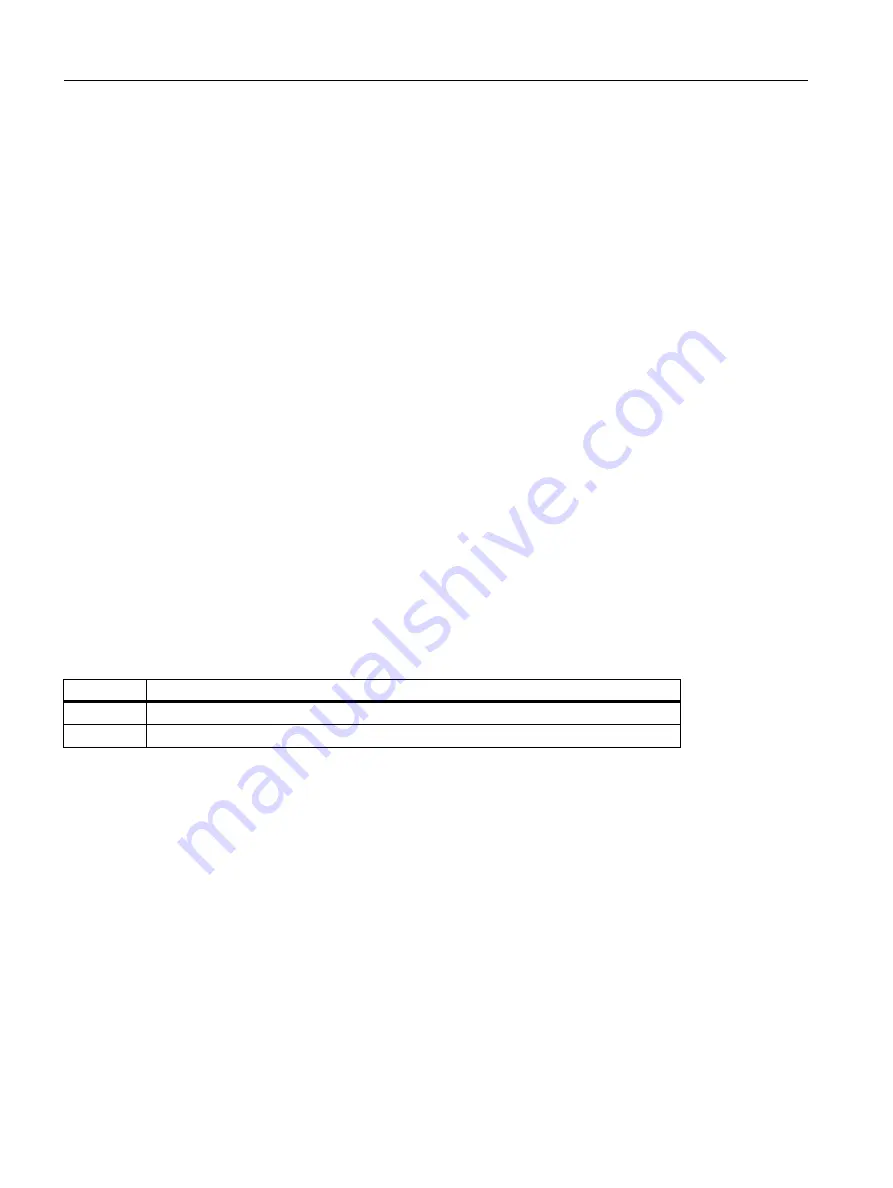
R1: Reference point approach
15.6 Referencing with distancecoded reference marks
Basic Functions
1226
Function Manual, 09/2011, 6FC5397-0BP40-2BA0
Abort criterion
If the parameterized number of reference marks is not detected within the parameterized distance, the machine
axis is stopped and reference point traversing is aborted.
MD34060 $MA_REFP_MAX_ MARKER_DIST (max. distance to the reference mark)
Features of phase 1
After phase 1 is successfully completed, the actual value system of the machine axis is synchronized.
15.6.5
Phase 2: Travel to fixed stop
Phase 2: Start
Phase 2 is automatically started when phase 1 has been completed without an alarm.
Initial situation:
• The machine axis is positioned directly behind the last of the parameterized number of reference marks.
• The actual value system of the machine axis is synchronized.
Phase 2: Sequence
In Phase 2, the machine axis completes reference point approach by traversing to a defined target position
(reference point). This action can be suppressed in order to shorten the reference point approach:
MD34330 $MA_STOP_AT_ABS_MARKER
Travel to target position (normal case)
The machine axis accelerates to the parameterized reference point position velocity and travels to the
parameterized target point (reference point):
MD34070 $MA_REFP_VELO_POS (Reference point positioning velocity)
MD34100 $MA_REFP_SET_POS (reference point value)
The machine axis is referenced. To identify this, the NC sets an interface signal for the measuring system that is
currently active:
DB31, ... DBX60.4 / 60.5 (Referenced/Synchronized 1/2) = 1
Value
Meaning
0
Travel to target position
1
No travel to target position