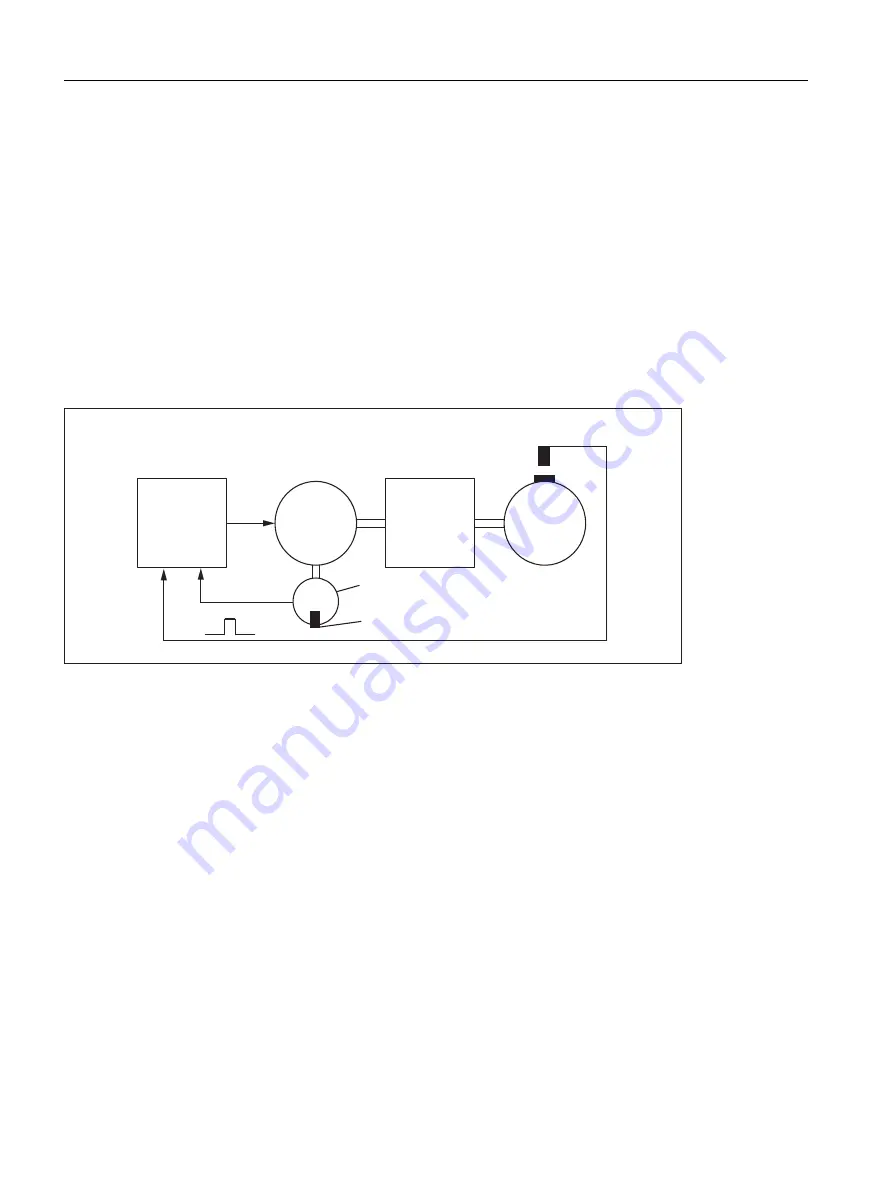
R1: Reference point approach
15.5 Referencing with incremental measurement systems
Basic Functions
1206
Function Manual, 09/2011, 6FC5397-0BP40-2BA0
15.5
Referencing with incremental measurement systems
15.5.1
Zero mark selection with BERO
Function
Referencing of incremental measuring systems is based on the unique position of the encoder zero mark relative
to the overall traversing range of the machine axis. If several encoder zero marks are detected in the traversing
range of the machine axis due to machine-specific factors, e.g., reduction gear between encoder and load, a
BERO must be mounted on the machine and connected to the relevant drive module (SIMODRIVE 611D) via a
BERO input in order to uniquely specify the reference point. The position of the reference point is then derived
from the combination of BERO signal and encoder zero mark.
Figure 15-1 Zero mark selection with BERO
Zero mark evaluation with BERO must be parameterized as the referencing mode:
MD34200 $MA_ENC_REFP_MODE = 5
Negative edge evaluation
In the case of a referencing operation with a negative edge evaluation of the BERO signal:
MD34120 $MA_REFP_BERO_LOW_ACTIVE = FALSE
synchronization is with the next encoder zero mark encountered after the BERO is exited.
Positive edge evaluation
In the case of a referencing operation with a positive edge evaluation of the BERO signal:
MD34120 $MA_REFP_BERO_LOW_ACTIVE = TRUE
synchronization is with the next encoder zero mark encountered after the BERO is approached.
If, mechanically, the BERO is sized in such a way that the positive BERO signal covers the entire width of the
encoder zero mark, the encoder zero mark will be reliably detected in both traversing directions.
'ULYH
3RVLWLRQ
0RWRU
*HDU
/RDG
6SLQGOH
0HDVXULQJV\VWHP
=HURPDUN
%(52