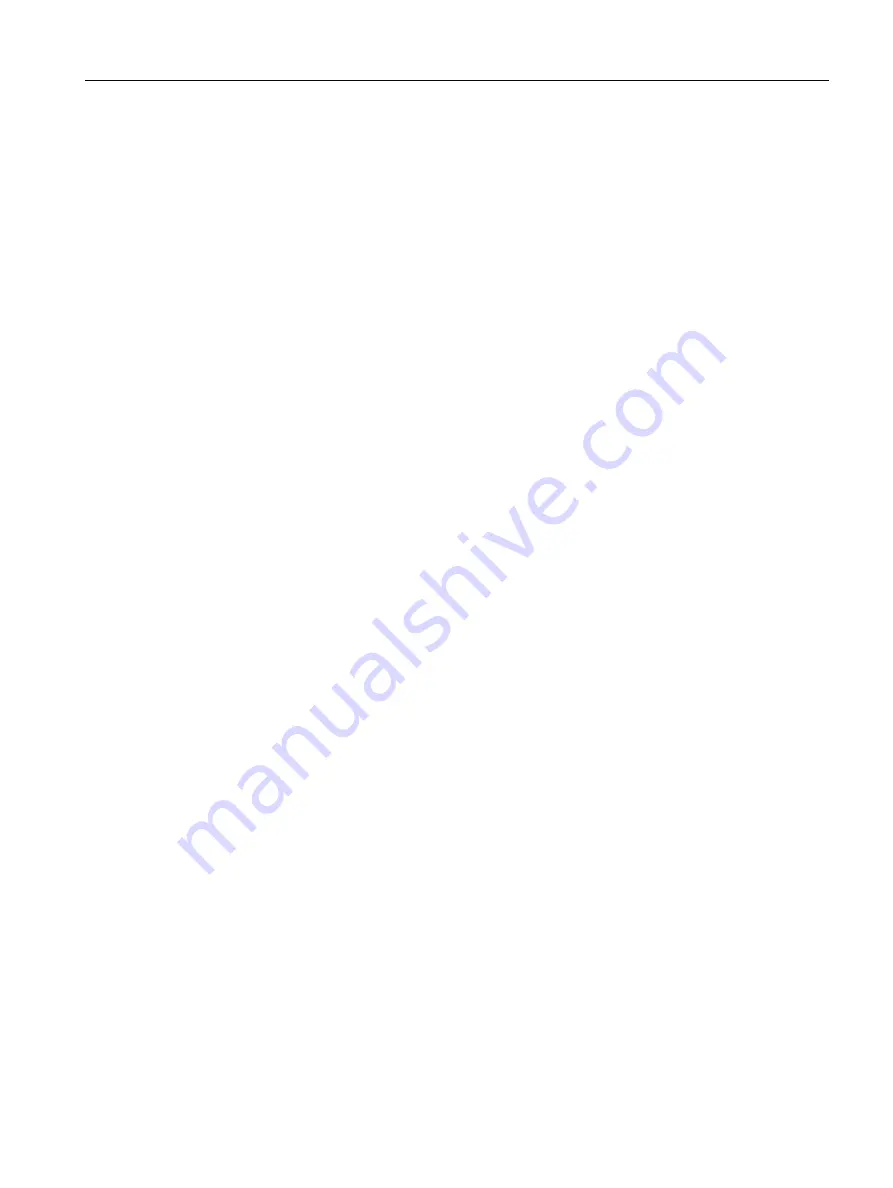
S1: Spindles
16.8 Spindle monitoring
Basic Functions
Function Manual, 09/2011, 6FC5397-0BP40-2BA0
1349
Maximum encoder limit frequency unudershot
If the maximum encoder frequency limit has been exceeded and the speed subsequently falls below the
maximum encoder limit frequency (smaller S value programmed, spindle offset switch changed, etc.), the spindle
is automatically synchronized with the next zero mark or the next Bero signal. The new synchronization will
always be carried out for the active position measuring system that has lost its synchronization and whose max.
encoder limit frequency is currently undershot.
Special points to be noted
If the following functions are active, the maximum encoder frequency cannot be exceeded:
• Spindle positioning mode, axis mode
• Thread cutting (
G33
,
G34
,
G35
)
• Tapping without compensating chuck
G331
,
G332
(does not apply to
G63
)
• Revolutional feedrate (
G95
)
• Constant cutting rate (
G96
,
G961
,
G97
,
G971
)
•
SPCON
16.8.8
End point monitoring
End point monitoring
During positioning (the spindle is in positioning mode), the system monitors the distance from the spindle (with
reference to the actual position) to the programmed spindle position setpoint (end point).
For this to work, in machine data:
MD36000 $MA_STOP_LIMIT_COARSE (Exact stop limit coarse)
and
MD36010 $MA_STOP_LIMIT_FINE (Exact stop limit fine)
two limit values can be defined as an incremental path starting from the spindle position setpoint.
Regardless of the two limit values, the positioning of the spindle is always as accurate as defined by the
connected spindle measurement encoder, the backlash, the transmission ratio, etc.