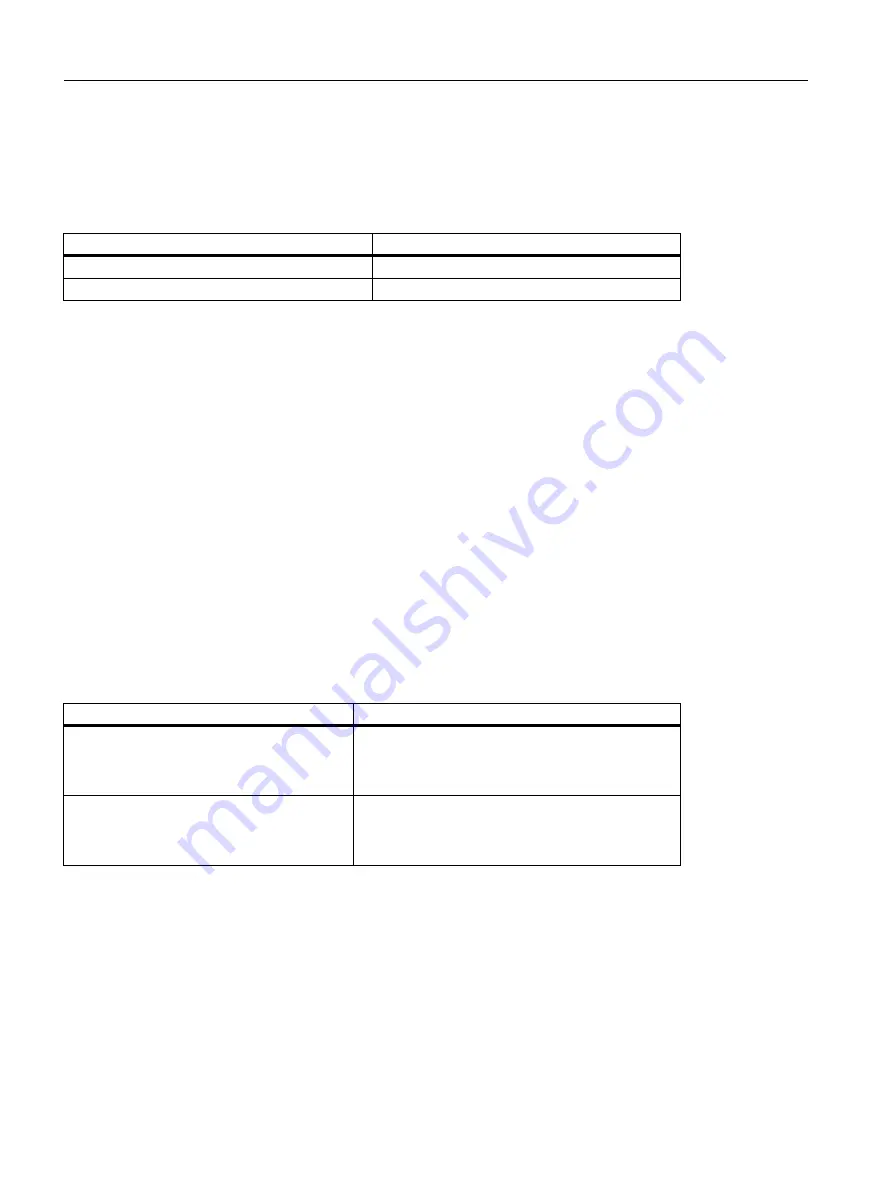
W1: Tool offset
18.9 Basic tool orientation
Basic Functions
1542
Function Manual, 09/2011, 6FC5397-0BP40-2BA0
In this example, the basic orientation points in the direction of the bisector in the L1L3 plane, i.e., the basic
orientation in the bisector for a milling tool and active plane
G17
lies in the Z/X plane.
Basic orientation of tools
The active tool orientation is unchanged in these cases and is equivalent to the original settings in $TC_DPVx[t,
d].
The basic orientation is always the direction perpendicular to the plane in which tool radius compensation is
performed. With turning tools, in particular, the tool orientation generally coincides with the longitudinal tool axis.
The setting data specified below are effective only if the basic orientation of the tool is defined by an entry in at
least one of the system variables $TC_DPVx[t, d].
They have no effect if the tool orientation is only determined by the plane selection
G17
-
G19
and is compatible
with previous behavior.
The plane of the basic orientation for a cutting edge is treated either like a milling tool or like a turning tool,
irrespective of the entry in $TC_DP1, if the following setting data is not equal to zero:
SD42950 $SC_TOOL_LENGTH_TYPE (allocation of the tool length components independent of tool type)
Plane change
A change of plane causes a change in orientation.
The following rotations are initiated:
These rotations are the same as those that have to be performed in order to interchange the components of the
tool length vector on a change of plane.
The basic orientation is also rotated when an adapter transformation is active.
If the following setting data is not equal to zero, the tool orientation is not rotated on a change of plane:
SD42940 $SC_TOOL_LENGTH_CONST (change of tool length components on change of planes).
Basic orientation of:
With :
Turning and grinding tools
G18
Milling tools
G17
When changing from:
Rotations
G17
⇒
G18
:
G18
⇒
G19
:
G19
⇒
G17
:
Rotation through -90 degrees about the Z axis
followed by rotation through -90 degrees about the X
axis
G17
⇒
G19
:
G18
⇒
G17
:
G19
⇒
G18
:
Rotation through 90 degrees about the X axis
followed by rotation through 90 degrees about the Z
axis