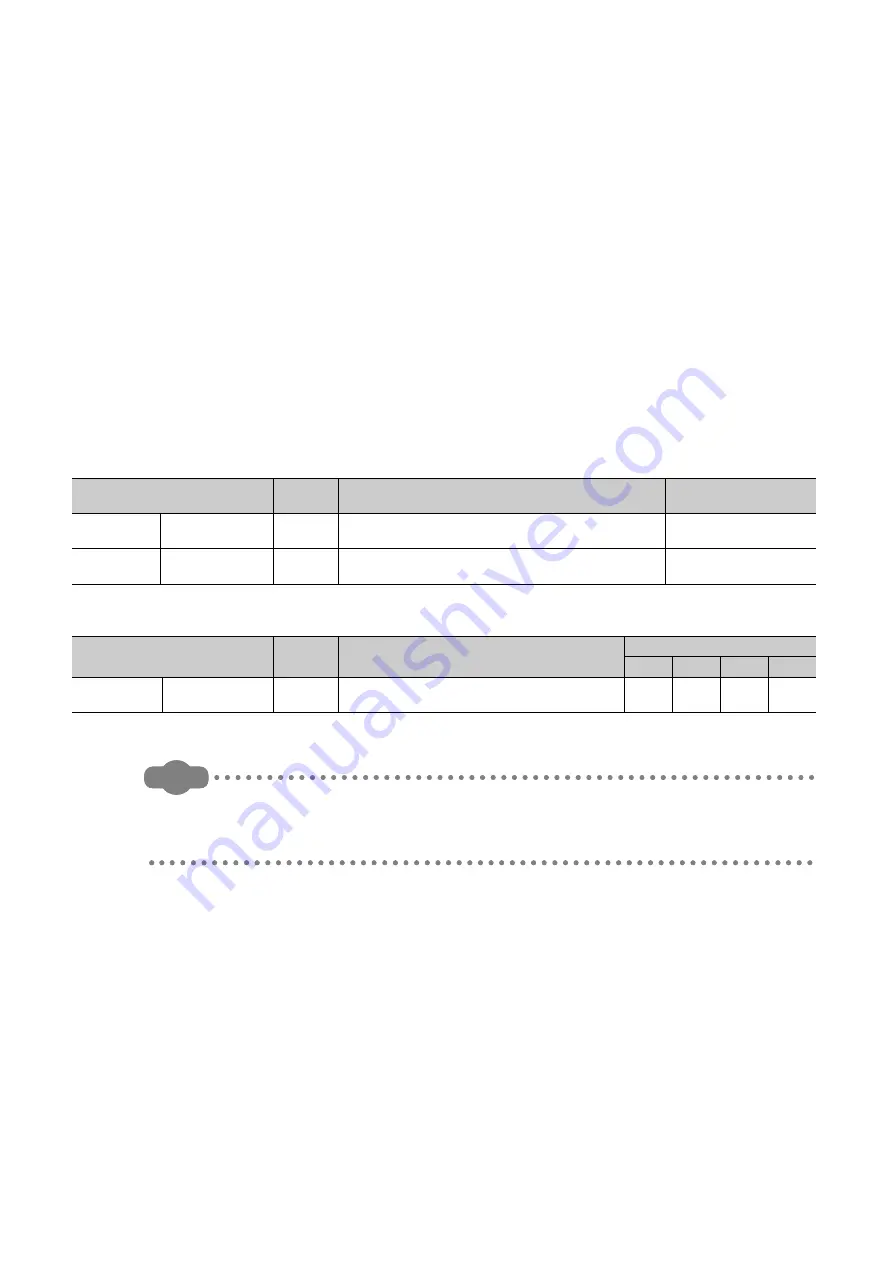
534
(4) Control precautions
• When limiting the torque at the "[Pr.17] Torque limit setting value", confirm that "[Cd.22] New torque value" is
set to "0". If this parameter is set to a value besides "0", the "[Cd.22] New torque value" will be validated, and
the torque will be limited at that value. (Refer to
Page 557, Section 12.5.4 for details about the "new
torque value".)
• When "[Pr.54] OPR shift amount" exceeds "[Pr.17] Torque limit setting value", the error "OPR torque limit
value error" (error code: 995) will occur.
• When the operation is stopped by torque limiting, the droop pulse will remain in the deviation counter. If a
"deviation counter clear" is carried out by issuing an external signal at this time, positional deviation will
occur when the operation is continued. If the load torque is eliminated, operation for the amount of droop
pulses will be carried out.
(5) Setting method
• To use the "torque limit function", set the "torque limit value" in the parameters shown in the following table,
and write them to the LD75. The set data is made valid on the rising edge (OFF to ON) of the PLC READY
signal [Y0].
Refer to
Page 118, Section 5.2 for the information on detail settings.
The following table shows the "[Md.35] Torque limit stored value" of the buffer memory address.
Refer to
Page 182, Section 5.6 for the information on detail settings.
Remark
●
Parameters are set for each axis.
●
It is recommended that the parameters be set whenever possible with GX Works2. Execution by program uses many
programs and devices. The execution becomes complicated, and the scan times will increase.
Setting item
Setting
value
Setting details
Factory-set initial value
[Pr.17]
Torque limit setting
value
Set the torque limit value as a percentage.
300
[Pr.54]
OPR torque limit
value
Set the torque limit value after the "[Pr.47] Creep speed" is reached.
Set as a percentage.
300
Monitor item
Monitor
value
Storage details
Buffer memory address
Axis 1
Axis 2
Axis 3
Axis 4
[Md.35]
Torque limit stored
value
The "torque limit value" valid at that time is stored. ([Pr.17]
or [Pr.54] or [Cd.22])
826
926
1026
1126
Summary of Contents for MELSEC-L LD75D
Page 2: ......
Page 11: ...9 Memo ...
Page 176: ...174 ...
Page 264: ...262 ...
Page 266: ...264 ...
Page 267: ...265 CHAPTER 6 PROGRAM USED FOR POSITIONING CONTROL 6 6 4 Positioning Program Examples ...
Page 268: ...266 ...
Page 269: ...267 CHAPTER 6 PROGRAM USED FOR POSITIONING CONTROL 6 6 4 Positioning Program Examples ...
Page 270: ...268 ...
Page 271: ...269 CHAPTER 6 PROGRAM USED FOR POSITIONING CONTROL 6 6 4 Positioning Program Examples ...
Page 272: ...270 Z ABRST1 instruction execution ...
Page 273: ...271 CHAPTER 6 PROGRAM USED FOR POSITIONING CONTROL 6 6 4 Positioning Program Examples ...
Page 278: ...276 ...
Page 279: ...277 CHAPTER 6 PROGRAM USED FOR POSITIONING CONTROL 6 6 4 Positioning Program Examples ...
Page 280: ...278 ...
Page 281: ...279 CHAPTER 6 PROGRAM USED FOR POSITIONING CONTROL 6 6 4 Positioning Program Examples ...
Page 282: ...280 ...
Page 283: ...281 CHAPTER 6 PROGRAM USED FOR POSITIONING CONTROL 6 6 4 Positioning Program Examples ...
Page 284: ...282 ...
Page 285: ...283 CHAPTER 6 PROGRAM USED FOR POSITIONING CONTROL 6 6 4 Positioning Program Examples ...
Page 286: ...284 ...
Page 287: ...285 CHAPTER 6 PROGRAM USED FOR POSITIONING CONTROL 6 6 4 Positioning Program Examples ...
Page 316: ...314 Memo ...
Page 685: ...683 APPENDICES A Appendix 1 Function Update Appendix 1 1 Function comparison Memo ...
Page 738: ...736 Memo ...
Page 817: ......